
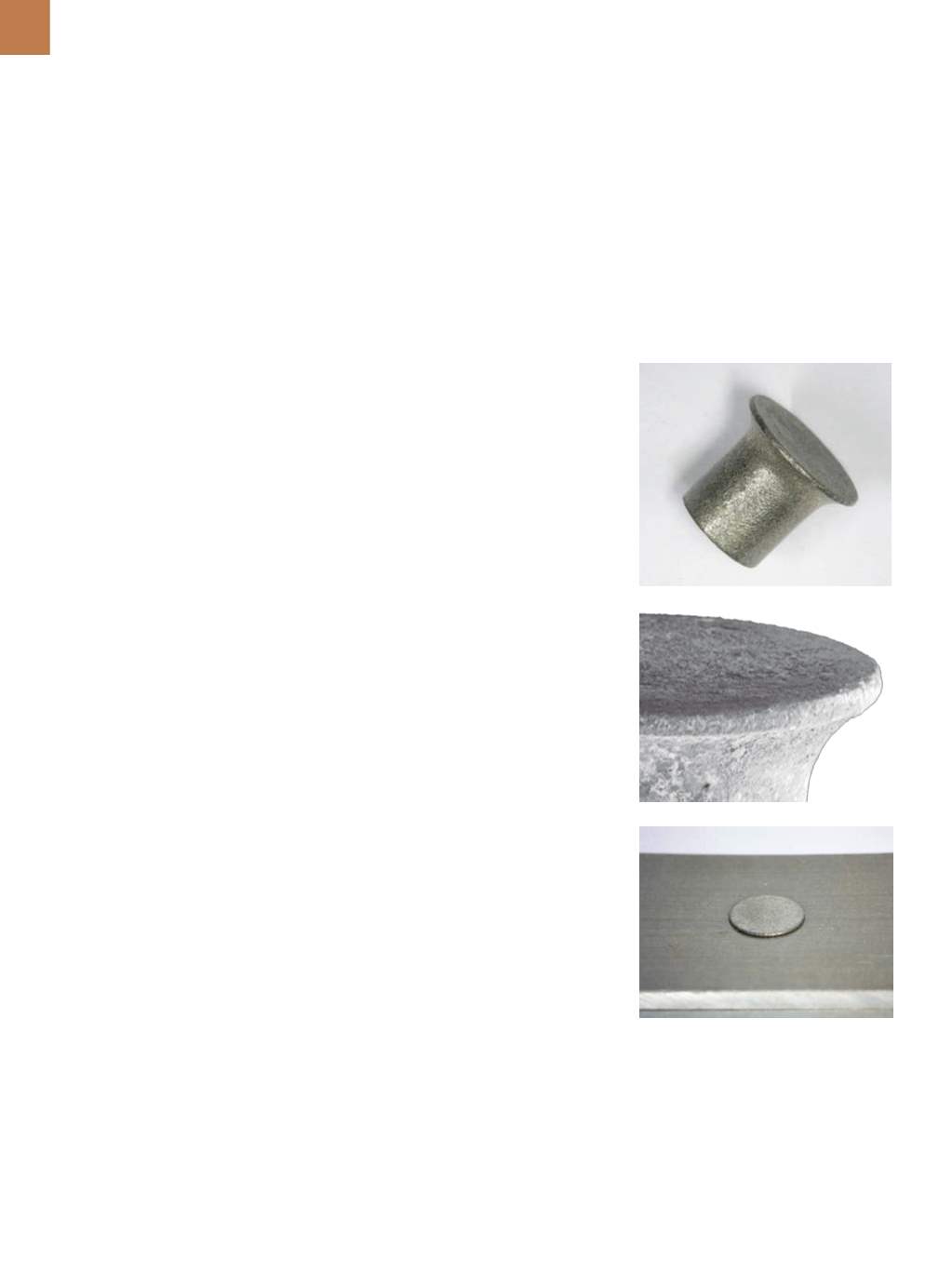
A D V A N C E D M A T E R I A L S & P R O C E S S E S | O C T O B E R 2 0 1 5
2 6
USING SIMULATION TO DESIGN
ANTICORROSIVE AUTOMOTIVE
COMPONENTS
Simulation of components and joints made of hybrid materials enables
innovative designs for corrosion protection in automotive applications.
TECHNICAL SPOTLIGHT
R
ivetsarecommonlyusedtoholddif-
ferent materials together—and can
easily be spotted on bridge support
beams, airplane doors, and car hoods, for
example. Found in metal-bodied vehicles
and support structures across the trans-
portation industry, these rivets usually
go unnoticed despite their critical role in
joining components that must withstand
enormous mechanical stress. Some cars
contain over 2000 of them. As automo-
tive designs trend toward lightweighting
and the use of multiple metals, questions
arise regarding the destructive, invisi-
ble culprit whose handiwork often goes
unnoticed until it is too late: Corrosion.
GALVANIC CORROSION
Galvanic corrosion is a constant
problem that costs the automotive
industry billions of dollars each year.
Caused by chemical reactions between
different metals coming into contact
withone another, this typeof corrosion is
often visible as a white powdery growth
that forms on the surface of metal parts
(Fig. 1, center). Bubbling paint and dete-
riorating aluminum are also signs that
metallic ions are being exchanged and
degrading a metal’s surface.
Various metal combinations react
differently to environmental impacts,
and a number of factors such as joining
techniques, material properties, and
surface roughness affect the chemical
reactions on rivets and the sheets they
bind together. Therefore, understand-
ing the underlying electrochemistry
is essential in order to develop robust
corrosion protection.
Engineers at Helmholtz-Zentrum
Geesthacht (HZG) and Daimler AG, both
Fig. 1 —
Clean rivet (top). Rivet showing
magnesium hydroxide deposit (white
growth) due to corrosion (center). Magnifica-
tion of a rivet in a test sheet (bottom).
in Germany, joined forces to investigate
corrosion prevention using multiphys-
ics simulation. The team sought ways
to streamline rivet design and develop-
ment, minimize physical testing, and
reduce the need for subsequent steps
such as surface treatment.
MODELING OFFERS INSIGHT
INTO CORROSION BEHAVIOR
To study galvanic corrosion kinet-
ics, including material loss, surface
conditions, and the long-term behav-
ior of interacting metals, Daniel Höche,
scientist at HZG, created a simulation
of a steel punch rivet joint using Multi
physics software from COMSOL, Burl-
ington, Mass. The rivet was plated with
an aluminum-zinc alloy that cathodi-
cally protects the steel. Software allows
the electrochemical interactions at the
surface and edges of the rivet to be
analyzed, predicts the decay of joined
sheets, and adjusts the geometry to
minimize corrosion.
This model consists of the rivet,
bonded metal sheets of aluminum and
magnesium, a 0.1% NaCl electrolyte
layer on the surface representing the
outside environment, and a galvanic
couple at the interface between the riv-
et and the sheets (Fig. 2). A corner burr
in the rivet geometry was also added to
simulate the presence of a sharp edge,
which increases gradients in the elec-
trolyte potential. This, in turn, increases
current flow and hastens the electro-
chemical reactions that cause galvanic
corrosion.
As the interface between the rivet
and sheets experiences corrosion, the
magnesium sheet begins to degrade
more rapidly than the other metals. The
chemical reaction produces magne-
siumhydroxide, Mg(OH)
2
, which forms a
weak barrier filmon the surface. Growth