
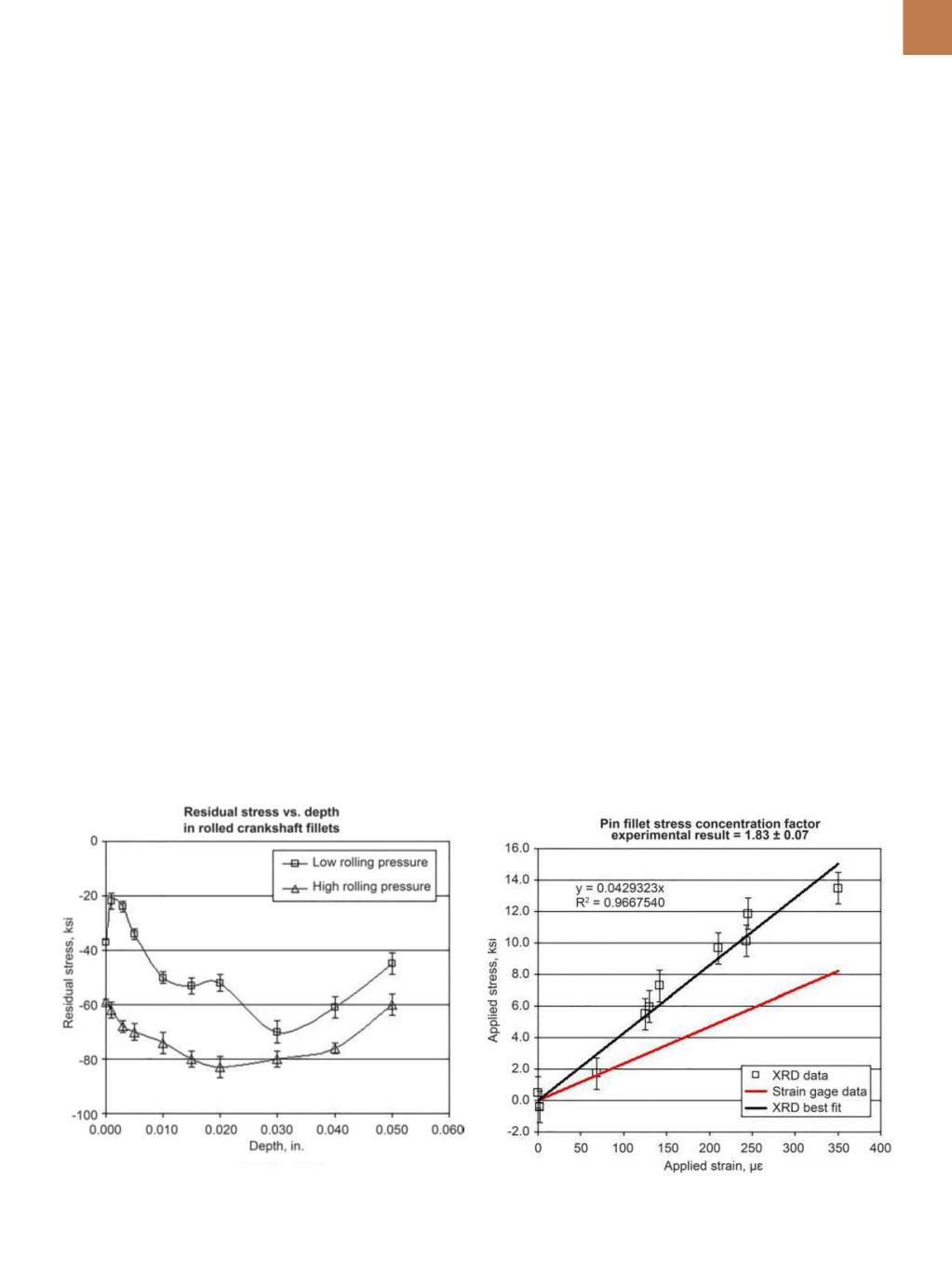
A D V A N C E D
M A T E R I A L S
&
P R O C E S S E S |
O C T O B E R
2 0 1 5
2 1
P
rocessing engine components
such as crankshafts, gears, shafts,
springs, rotors, cylinder heads, and
engine blocks poses several difficulties
for manufacturers. For example, manu-
facturing a finished product with the su-
perior material characteristics required
for a given application is often challeng-
ing. Among the characteristics of interest,
residual stress can have a significant im-
pact on the effective service life of engine
components. Because residual stresses
are introduced in nearly every step in
manufacturing, the effect of processing
on failure-critical locations must be well
understood, controlled, and optimized.
The x-ray diffraction (XRD) tech-
nique can be used to characterize re-
sidual stresses in crankshafts and is of-
ten the only viable method to measure
these stresses at certain failure-critical
locations, for example, in the rolled
fillet radius of a crankshaft. Surface
residual stress measurements can be
performed nondestructively for inline
quality control and for tracking stresses
through processing and in-service cy-
cling. Crankshaft subsurface gradients
can also be evaluated at various stages
of manufacture to benchmark the ef-
fects of each manufacturing process.
The service life of engine compo-
nents often varies greatly as a result of
as manufactured
residual stress levels
found in failure-critical locations. With
increased demand from consumers for
quality, reliability, and seamless perfor-
mance, manufacturers must meet or ex-
ceed specified warranty periods and re-
duce recalls and warranty repairs. Thus,
the stress state of critical components
must be accurately characterized so that
contributingmechanisms and sources of
potentially harmful residual stresses are
well understood. Fabrication process-
es can then be modified and optimized
to ensure high-quality components are
manufactured at a competitive cost.
CHARACTERIZING
RESIDUAL STRESS
When residual stress is thought to
be a contributing factor to premature
failure, such suspicions may be validat-
ed by both experiment and measure-
ment. XRD can also be used to verify
the effectiveness of heat treatment pro-
cesses and the impact of surface treat-
ments such as grinding, turning, rolling,
or shot peening.
In order to increase crankshaft
life, fillets are commonly burnished
or rolled to introduce sufficient com-
pressive residual stresses that inhibit
initiation and propagation of fatigue
cracks. The effect of the rolling process
is often characterized as a function of
depth because stress gradients normal
to the rolled surface are introduced
by the process. Residual stress versus
depth profiles are also typically collect-
ed at different angles around the cir-
cumference of the fillet because man-
ufacturers often vary rolling pressure
with angular position around the fillet
(Fig. 1). This is particularly important
in the case of pin journals, especially
when a split pin design is used. In order
to segregate rolling induced stresses
from those caused by heat treatment
and other cold working processes, re-
sidual stress as a function of depthmust
be characterized at various stages. This
also includes effects that result from
any straightening processes potentially
applied as a final manufacturing step.
Stress concentration factors (SCFs)
used to estimate applied loads in ser-
vice are often based on calculation or
modeling, or quoted from literature.
XRD techniques have been used to ex-
perimentally measure the effective SCF
for a given undercut radius geometry.
As an example, known bending loads
were applied to a test crankshaft and
stress as a function of applied load
was measured in the rolled fillet. The
SCF was experimentally derived from
this data and the result of 1.83 ± 0.07
Fig. 1 —
Residual stress vs. depth profiles collected on a crankshaft
using x-ray diffraction in areas of high pressure and low pressure rolling
in a pin journal fillet radius.
Fig. 2 —
Experimental determination of the stress concentration factor
(SCF) in a pin journal fillet radius.