
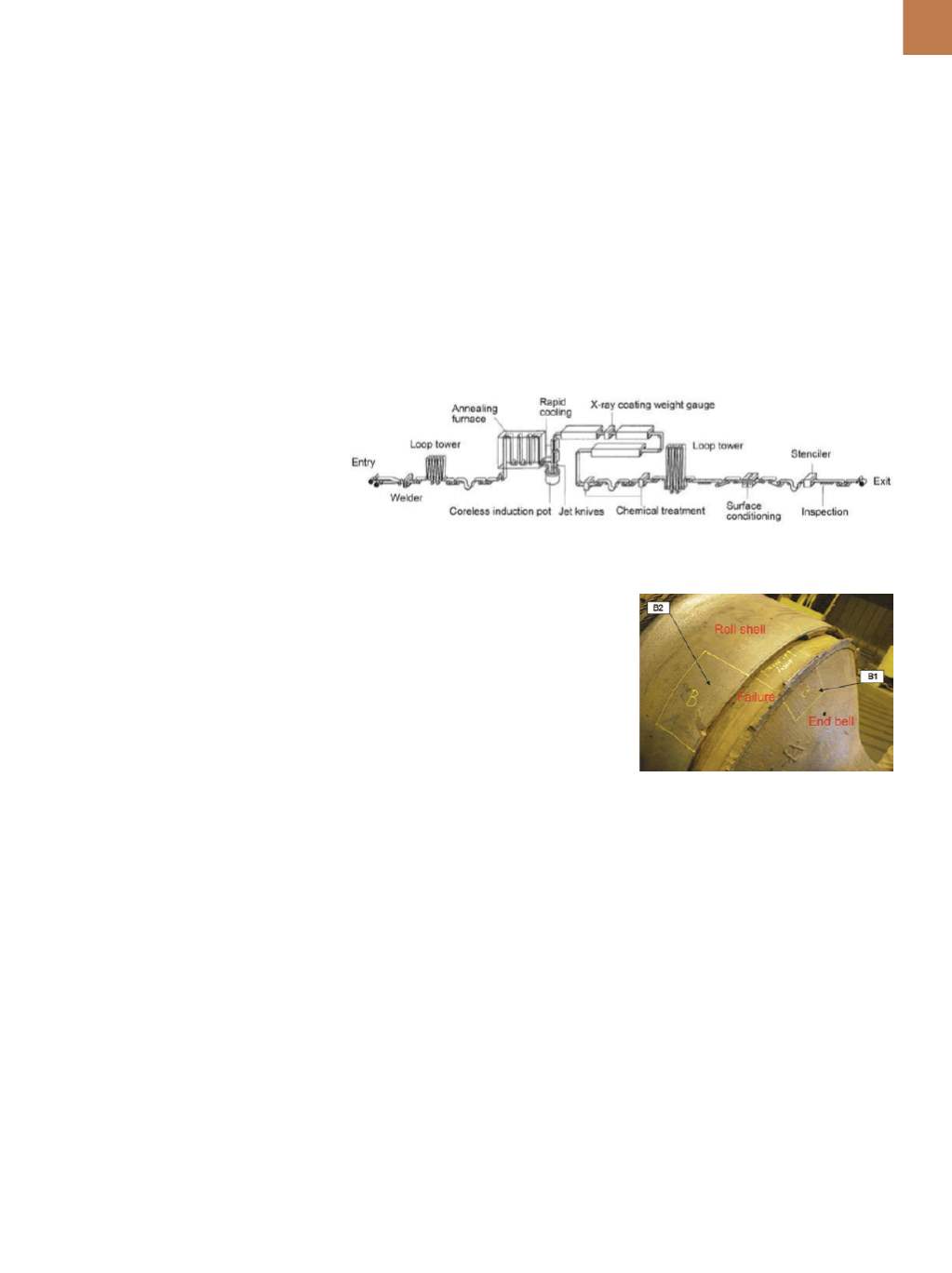
A D V A N C E D
M A T E R I A L S
&
P R O C E S S E S |
O C T O B E R
2 0 1 5
2 3
FURNACE ROLL FAILURE ANALYSISON
HOT-DIP COATING LINE SPURSNEW
DESIGNANDWELDINGPROCESS
A new design and welding process may extend the life of furnace rolls in hot-dip
coating lines, which often fail in less than one year.
Yu-Ping Yang* and William Mohr,* EWI, Columbus, Ohio
S
teels are commonly coated for
commercial applications by clad-
ding, electrolytic coating, or hot-
dip coating methods. The hot-dip pro-
cess provides a tight metallurgical bond
between the steel substrate and pro-
tective coating. This method results in a
material with the strength of steel, the
corrosion protection of a robust coat-
ing, and the synergistic heat defense of
a coated alloy.
ROLL FAILURE CASE STUDY
A continuous hot-dip coating line
is schematically illustrated in Fig. 1
[1]
.
Rolls in the production line transport
the steel strip through the line. At the
entry point on the left, a steel coil is
loaded onto reels. The leading edge of
the coil is welded to the tailing edge of
the preceding coil. Next, the strip enters
the first cleaning stage, an alkaline bath
that removes oils, dirt, and residual iron
fines from the rolling process, and then
goes into the looping tower, which acts
as a sheet reservoir. After exiting the
looping tower, the strip surface is fur-
ther cleaned by mechanical brushing
and electrolytic alkaline cleaning
[2]
. Fol-
lowing cleaning, the sheet passes into a
preheating furnace where the steel strip
is heated by direct fire.
The steel strip then enters a pot
containing a bath of molten coating
metal where the actual hot-dip coat-
ing process takes place. An intermetal-
lic layer is formed between the coat-
ing and steel sheet during the hot-dip
process, which may consist of either a
single phase or more than one phase
depending on dipping temperature
and time
[3]
. As the strip exits the pot, a
film of molten coating adheres to the
surface while forced-air cooling reduc-
es temperature. This prevents coating
damage due to contact with the turn-
around roll at the top of the upper leg
run. The sheet may be subjected to one
or more post-treatments before being
rewound into coil form or sheared into
cut lengths at the end of the line.
In the case study explored in this
article, catastrophic roll failure was
observed in the preheating furnace of
the continuous hot-dip coating line,
as shown in Fig. 2. The failed roll had
been in service for approximately seven
months. Failure occurred in the weld
that joined an end bell to a roll shell,
which resulted in the complete 360
°
separation of the bell from the shell.
The roll shell and end bell were made
of high-temperature alloy 22-H, while
the journal was made of stainless steel
310. Inconel welding electrode 117 was
used as weld filler material. The roll
shell and end bells were shrink fitted
before welding and the specific weld
process was flux-cored arc welding.
Upon completion of welding, post weld
heat treatment was applied for three
hours at 1093
°
C to the entire roll. His-
torically, this type of roll exhibits a short
lifespan—less than one year—which is
an ongoing problem.
FAILURE ANALYSIS
Service records of the failed roll
document its thermal and mechanical
loading history. The recorded furnace
temperature in the 160 days prior to
failure—in a location near the failed
roll—shows that the roll was routine-
ly exposed to operating temperatures
between 982
°
–1066
°
C, with frequent
temperature fluctuations of more than
500
°
C. Occasionally, the furnace tem-
perature dropped to roughly 200
°
C.
Fig. 1 —
Process diagram of a continuous hot-dip coating line
[1]
.
Fig. 2 —
Welded joint failure in a furnace roll.
*Member of ASM International