
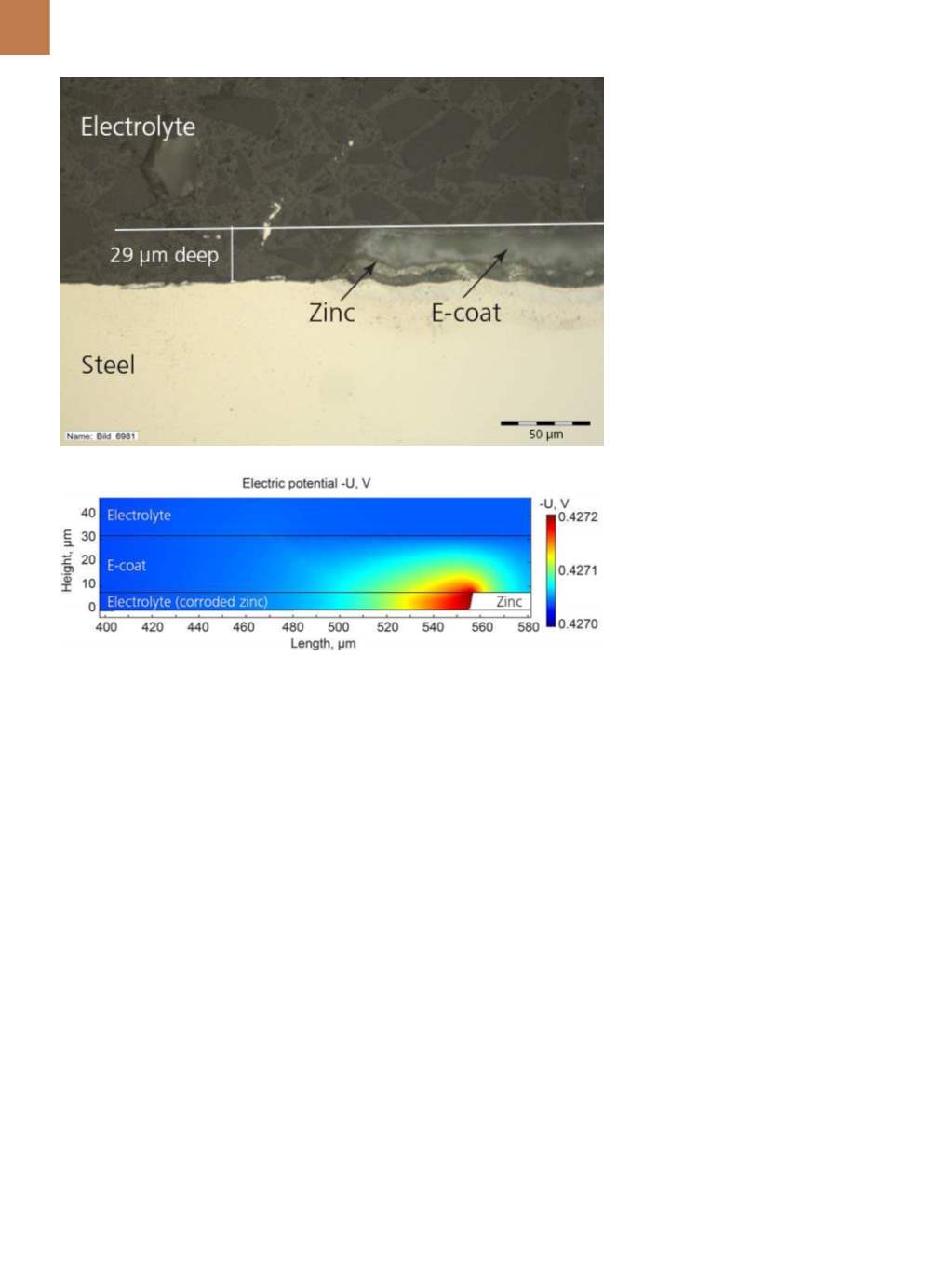
A D V A N C E D M A T E R I A L S & P R O C E S S E S | O C T O B E R 2 0 1 5
2 8
components are also at risk from expo-
sure to natural elements. Seemingly
superficial imperfections, such as a
scratch in the coating or paint on a
panel, allow moisture and environmen-
tal electrolytes access to electrically
conductive surfaces. In car paneling,
small impairments can create a galvan-
ic couple that causes delamination—
the debonding of coatings on metal
sheets—which significantly weakens
the corrosion protection.
To analyze this additional risk,
Höche worked with Nils Bösch of
Daimler AG to study delamination on a
zinc-plated steel test sheet electrocoat-
ed with a layer of cathodic paint called
an
e-coat
(Fig. 4). If a scratch extends
down to the steel surface, a galvanic
couple occurs between the zinc and
steel causing the zinc to corrode. This
results in a crevice that grows continu-
ously between the e-coat and steel in a
horizontal direction, rather than verti-
cally through the layers. This behavior
is similar to crevice corrosion, which
digs between two surfaces and creates
fissures in the metal. Stress fractures at
the base of these cracks can eventual-
ly cause part failure, even though the
obvious damage and overall material
loss may appear small.
Höche and Bösch used paramet-
ric sweeps in the simulation software
to study the electric potential in the
electrolyte and e-coat for different
e-coat barrier properties. Their model
reports the corresponding horizontal
growth of the crevice as it consumes
the zinc (Fig. 5).
The quest to understand how the
size of these surface defects impacts
the rate of zinc consumption is ongo-
ing. So far, the model indicates that
the width of these defects has a great-
er influence than the depth—a smaller
cathode/anode ratio and more limited
diffusion is present in the narrower
scratches, which slows the corrosion
process compared to a wider impair-
ment. Existing results are being used
to further investigate coating flaws for
their negative influence on corrosion
protection.
LONGER-LASTING
STRUCTURAL SUPPORT
Although corrosion cannot be
avoided entirely, it can be minimized
through expert design and careful anal-
ysis. Höche and Bösch reduced the
sharp edges in the rivet joint and honed
the geometry to minimize the exposed
area while maintaining mechanical
stability. They also recommended an
e-coat for the sheet metal that, based
on the parametric study, exhibits the
lowest electric current and therefore,
the least decay in the paneling. Their
computer models offer valuable insight
into relevant electrochemical behavior,
providing engineers the tools to opti-
mize rivet joints to offer the best corro-
sion resistance.
Computer-aided analysis can
enhance recent progress regarding
lightweight, multi-material designs
and enable identification of possi-
ble corrosion problems early in the
development cycle. Despite corrosion
being an enemy to the automotive
rivet, control of magnesium corrosion
through knowledge-based processing
and careful geometric design is within
reach.
~AM&P
For more information:
Lexi Carver is
technical marketing engineer, COMSOL
Inc., 1 New England Executive Park, Bur-
lington, MA 01803, 781.273.3322,
lexi. carver@comsol.com,
www.comsol.com.Fig. 5 —
Close-up of a cross-section of the test sheet where a scratch destroyed part of the
e-coat and zinc layers (top). Simulation software results show the electric potential in the e-coat
and electrolyte. The white region shows remaining zinc after much of it was already consumed
(bottom).