
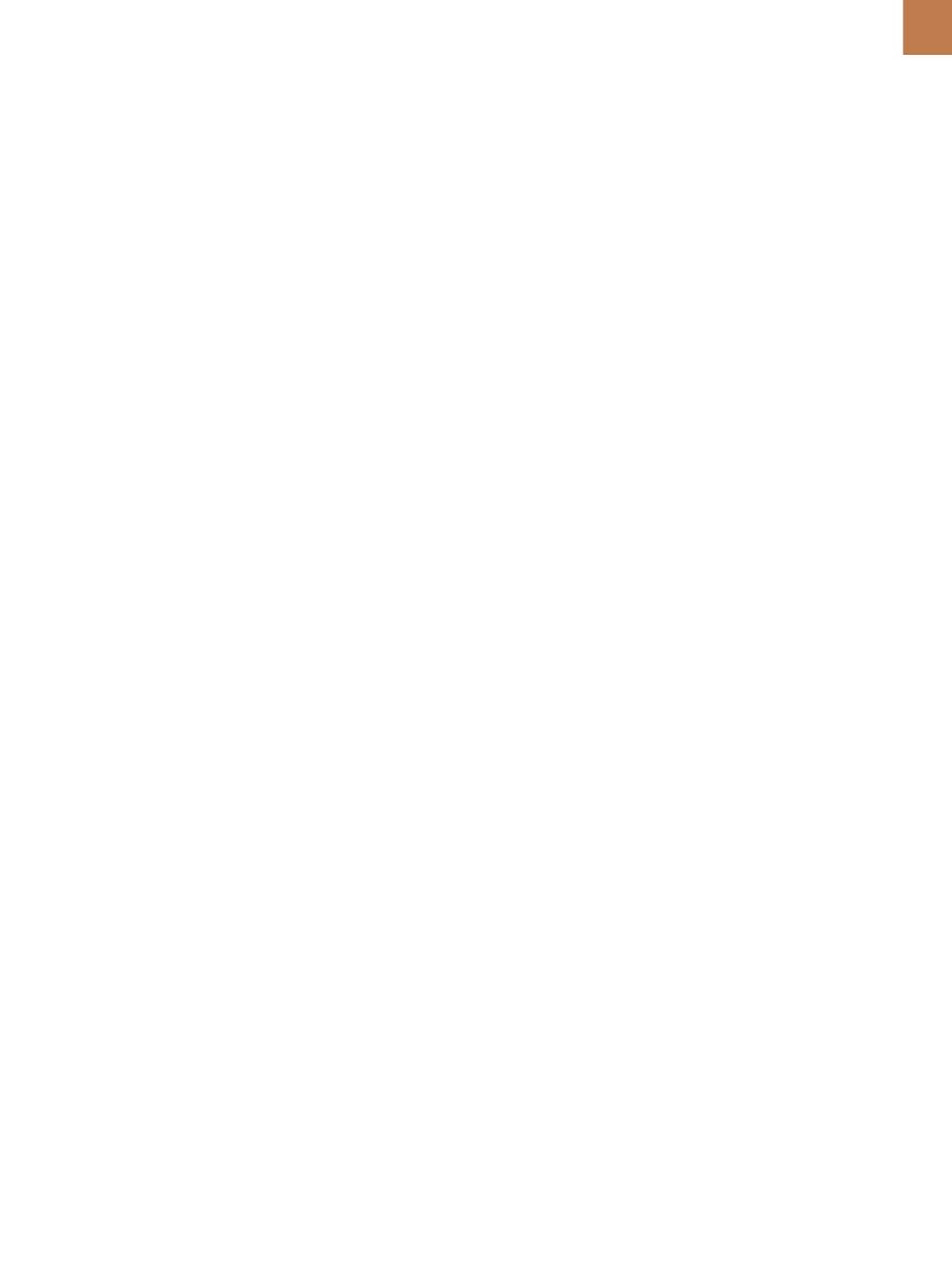
A D V A N C E D
M A T E R I A L S
&
P R O C E S S E S |
O C T O B E R
2 0 1 5
2 9
SOLVING ELECTRONIC SYSTEM
FAILURES IN AEROSPACE
APPLICATIONS
Determining the root cause of avionics failures requires a disciplined and
systematic analytical process supported by sophisticated equipment.
TECHNICAL SPOTLIGHT
T
he aerospace industry continues to
face difficult challengeswith regard
to electronic system failures. As
advanced semiconductor processes en-
able more compact devices to be created
from smaller structures, even those that
appear flawless can still exhibit perfor-
mance problems arising from as little as
onemisplacedatom. Inaddition, avionics
and other aerospace systems operate in
extremely harsh environments character-
ized by temperature and power cycling,
vibration and shock, and demanding re-
quirements related to high current flows
and thermal transfer. Determining the
root cause of avionics failures requires a
disciplined and systematic analytical pro-
cess, supported by sophisticated tools
that test and visualize the behaviors and
characteristics of sample devices.
TYPICAL AVIONICS
SYSTEM FAILURES
Aerospace systems fail for a variety
of reasons, including quality issues as
well as stresses associated with harsh
operating environments. The role of
quality issues was highlighted in a July
2011 report from the U.S. Government
Accountability Office (GAO) entitled
“Space and Missile Defense Acquisi-
tions: Periodic Assessment Needed to
Correct Parts Quality Problems in Major
Programs.” The GAO document notes
that most parts quality problems are
associated with electronic versus me-
chanical parts or materials, and they
result from “…poor workmanship, un-
documented and untested manufac-
turing processes, poor control of those
processes and materials and failure
to prevent contamination, poor part
design, design complexity, and an in-
attention to manufacturing risks.” Even
assuming a bulletproof parts quality
program, environmental stresses on
both military and commercial avionics
systems increase the likelihood of field
failures. This is especially true with the
trend toward smaller surface-mounted
and chip-scale packaged devices used
to reduce size and weight.
The GAO report lists a number of
common device failure types in Depart-
ment of Defense and NASA aerospace
systems including attenuators that
exhibit inconsistent performance due
to sensitivity to temperature changes;
printed circuit boards that fail intermit-
tently due to connection points vulner-
able to thermal stresses; and capacitors
that develop a phenomenon known
as
tin whiskers,
which can cause cata-
strophic problems to avionics systems.
These and other failures can be difficult
to diagnose without a comprehensive
and disciplined analysis process.
SYSTEMATIC PROCESS
HALLMARKS
A thorough process starts with a
broad system view and then narrows to
the power supply, board, or component
level, or even deeper to an integrated
circuit (IC) logic block or transistor. The
first phase is nondestructive, consisting
of visual examination, x-ray, and elec-
trical verification of the failure mode.
Prematurely initiating destructive anal-
ysis runs the risk of losing valuable in-
formation because some failure mech-
anisms are sensitive to temperature
and can change during desoldering or
decapsulation.
Once the failure signature is ac-
quired, analysis moves to troubleshoot-
ing failures on a printed circuit board
(PCB) or component. The goal is to find
all failing components and—in the case
of electrical overstress—identify the
current path. The ultimate goal is to
identify both the failure origin and ini-
tial failure mechanism. Bypassing full
system-level analysis can be a costly
mistake. All too often, what initially ap-
pears to be electrical overstress might
actually involve other failure mecha-
nisms that can be missed without a top-
down, system-level approach.
After acquiring electrical data to
localize failures to a PCB or component,
analysts move to IC and discrete com-
ponent analysis while looking for the
failure mechanisms. A meta-loop pro-
cess tests each failure hypothesis while
evidence either confirms or disproves
the hypothesis. If necessary, more infor-
mation is gathered so a new hypothesis
can be proposed. Applying short-loop
techniques repeatedly throughout the
analysis helps determine the underly-
ing failure mechanism.
DIAGNOSTIC TOOLS
Nondestructive test tools include
external visual examination, x-ray and
C-mode scanning acoustic microscopy
(CSAM), curve trace, and time domain
reflectometry (TDR). These tools can be
particularly useful for identifying fail-
ures related to tin whiskers, a phenom-
enon that has resurfaced with the move
to lead-free processes. The tin whiskers
shown in Fig. 1 are conductive metallic
structures that grow from the surface
of tin finishes. They can cause shorts