
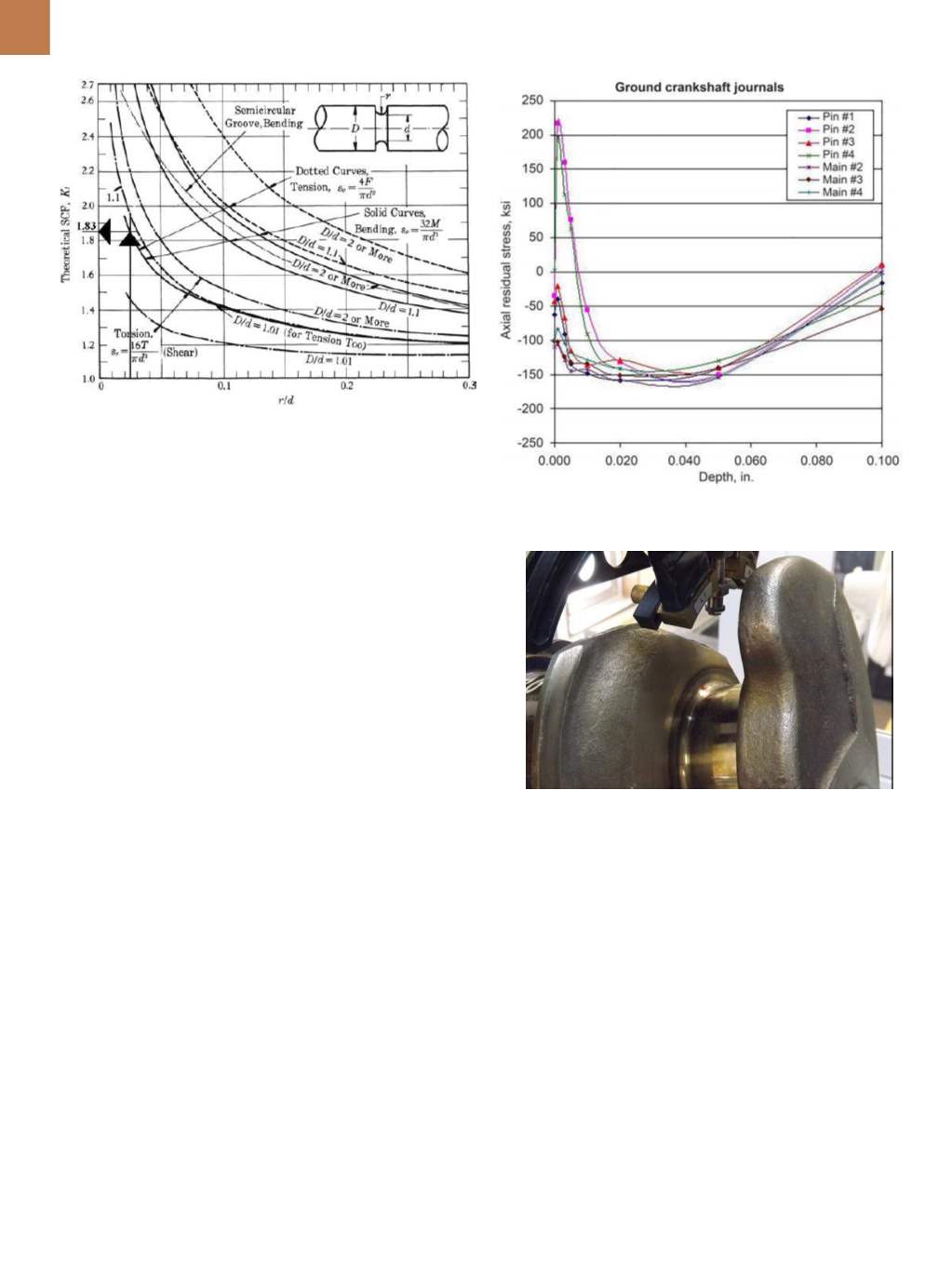
A D V A N C E D M A T E R I A L S & P R O C E S S E S | O C T O B E R 2 0 1 5
2 2
(Fig. 2) agreed with theoretical calcula-
tions within experimental error (Fig. 3).
Main bearing and pin journal sur-
faces are typically precision ground to
obtain the desired dimensional accu-
racy and surface finish. Tensile residual
stresses imparted by grinder burn can
have a significant impact on the life of
a ground journal. Detection and char-
acterization of grinder burn is there-
fore extremely important and can be
performed using XRD. In general, the
maximum tensile stresses due to grind-
er burn (abusive grinding) are found
at shallow depths below the ground
surface of a journal suffering from this
effect. In order to reliably characterize
residual stresses due to grinder burn, it
is necessary to collect subsurface resid-
ual stress profiles (Fig. 4).
When residual stress measure-
ments are required in the hoop direc-
tion of a pin journal in the fillet radius,
they can usually be performed without
sectioning at locations farthest from
the crankshaft axial centerline. How-
ever, in cases where measurements are
required adjacent to counterweights,
or for measurements in the axial direc-
tion of the crankshaft, some section-
ing may be required. This procedure
should be limited to areas where access
of the goniometer is hindered by crank-
shaft geometry or where the incident
or diffracted x-ray beam is shadowed
(blocked). The effects of
sectioning can be char-
acterized by installing a
small strain gage near
the measurement point
in the direction for stress
measurement and mon-
itoring it during the pro-
cess. Subsequent resid-
ual stress measurement
results can be corrected
for relaxation due to sec-
tioning. Current state-
of-the-art instrumenta-
tion that works in both
psi and true-chi modes
(rather than modified
chi) can minimize the need for section-
ing and certain locations can be ac-
cessed without sectioning.
Residual stress measurements
should be performed using the multi-
ple exposure technique (MET) in accor-
dance with SAE HS784 and ASTM E2860
recommended procedures, and equip-
ment should be calibrated to national
standards including ASTM E915.
Subsurface residual stress gradi-
ents can be evaluated for crankshafts
taken from various stages of manu-
facture to benchmark the subsurface
effects of each manufacturing process.
Once contributing mechanisms and
sources of potentially harmful residual
stresses are well understood, fabrica-
tion processes can then be modified
and optimized so that high-quality
components can be manufactured at
a competitive cost. In many cases, this
insight can only be achieved using XRD
techniques.
~AM&P
For more information:
James Pineault
is laboratory director, Proto Mfg. Inc.,
12350 Universal Dr., Taylor, MI 48180,
313.965.2900,
xrdlab@protoxrd.com,
www.protoxrd.com.Fig. 3 —
Theoretical SCF for geometry similar to a pin journal radius.
Fig. 4 —
Residual stress vs. depth profiles for different grinding
parameters.
Fig. 5 —
State-of-the-art Microarea instrument works in both psi
and true chi modes to characterize residual stresses at certain
features on a crankshaft without sectioning.