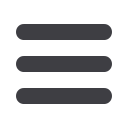
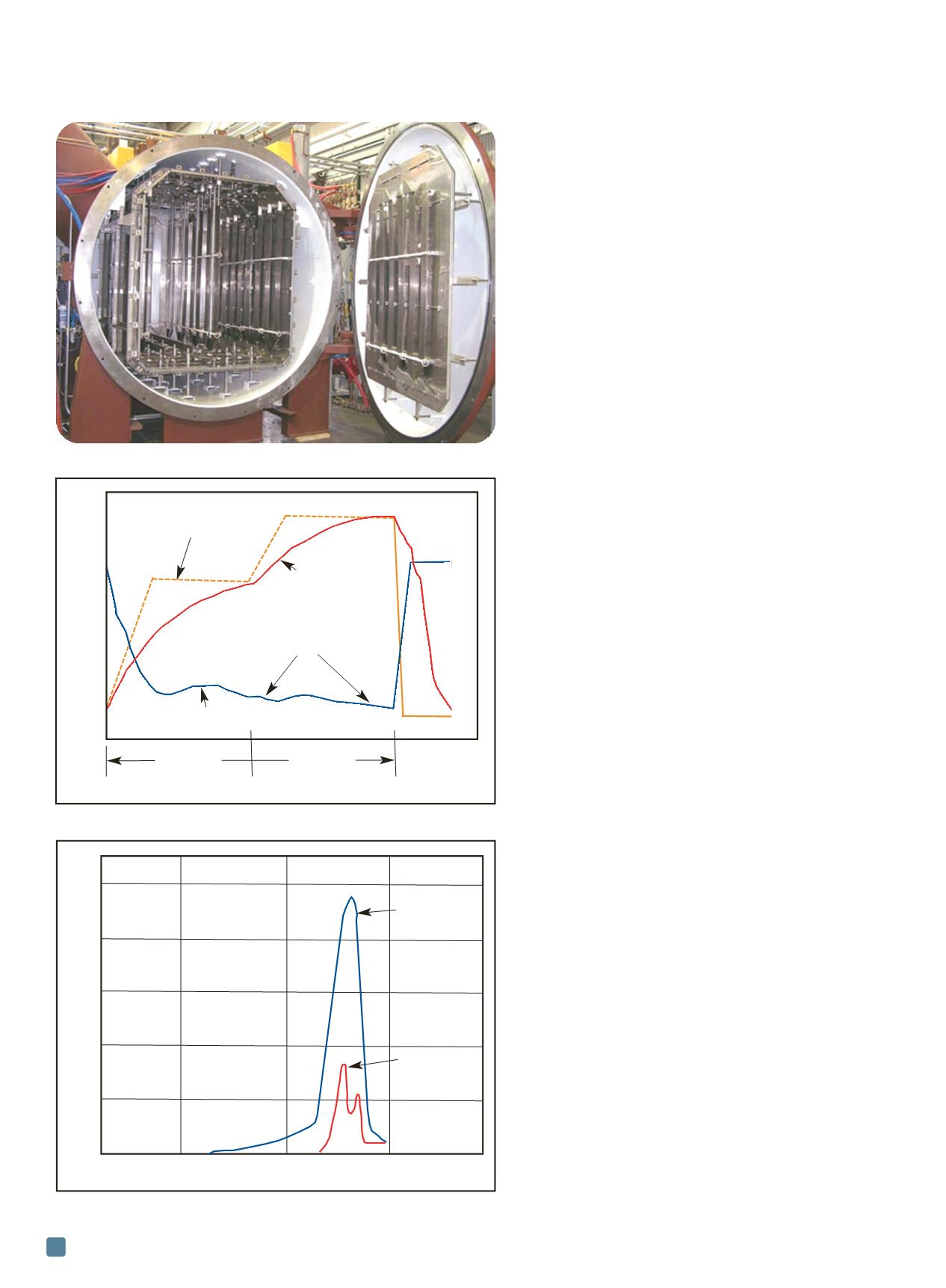
ers, condensers, and evaporators used in automotive, aero-
space, nuclear, and energy industries.
Vacuum aluminum brazing furnaces
Typical VAB furnaces are either single-chamber (batch
type) or multiple-chamber (semi-continuous). Batch type
furnaces are usually loaded horizontally, but can be de-
signed for vertical loading. Semi-continuous furnaces are
horizontally loaded and are typically automated using load
carriers and external conveyor systems.
Batch furnaces tend to be simpler in design (one load-
ing/unloading door), less expensive, and easier to maintain
(Fig. 2) than semi-continuous furnaces. Semi-continuous
furnaces have higher production rates because of the
multi-chamber design and operate more efficiently by not
having to cool heating zones or heat cooling zones.
The VAB process is typically a relatively short cycle due
to the fast pumping and heating characteristics of the fur-
nace, excellent temperature uniformity at soak tempera-
tures, and high thermal conductivity of the aluminum parts
being brazed. Figure 3 shows a typical VAB cycle.
Vacuum pumping capacity must be adequately sized in
order to minimize pump downtime of a new load to a deep
vacuum level, so as to initiate the heating cycle and have
adequate throughput to keep up with outgassing taking
place during the heating cycle. This outgassing takes place
due to magnesium vaporization. Deep vacuum level is an
important process parameter because it ensures a relatively
pure environment for brazing (less PPM of oxygen).
Magnesium plays key role
A key component of VAB is magnesium use as an ad-
ditive to the filler metal and/or base metal of the parts to
be brazed. It is necessary in this fluxless brazing environ-
ment because:
• Magnesium vaporizes at roughly 1058°F (570°C) and
acts as a “getter” for oxygen and water vapor, thus
improving the brazing vacuum purity
• Magnesium reduces alumina oxide on aluminum’s
surface, promoting uniform accelerated wetting of
joint surfaces
The following reactions occur during the vacuum braz-
ing process:
Mg + H
2
O —> MgO + H
2
Mg + O
2
—> 2 MgO
3 Mg + Al
2
O
3
—>
3
MgO + 2 Al
Mg + N
2
—> Mg
3
N
2
Magnesium vaporization in a vacuum environment can
be seen in Fig. 4. Also known as a “mag burst,” magnesium
vaporization produces heavy outgassing for a short period.
Figure 4 shows that slower heating rates reduce the magne-
sium vaporization rate. Due to this gas load, vacuum
pumps must be adequately sized to maintain a good work-
ing vacuum (10
-4
to 10
-5
torr range).
Precise temperature control and uniformity are also
important process parameters. Accepted temperature uni-
ADVANCED MATERIALS & PROCESSES •
JULY 2014
16
Fig. 2 —
Batch vacuum aluminum brazing furnace.
Fig. 3 —
Typical vacuum aluminum brazing cycle.
Fig. 4 —
Magnesium vaporization in vacuum vs. temperature.
Time
1/2 cycle
1/2 cycle
Vacuum
temperature
Program
Part temperature
10
-5
torr range
≥ 1.10
-4
torr
500
550
600
Temperature, °C
Heating rate
10°C/min
2°C/min
1.0
0.8
0.6
0.4
0.2
Mg loss rate