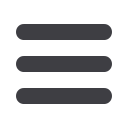
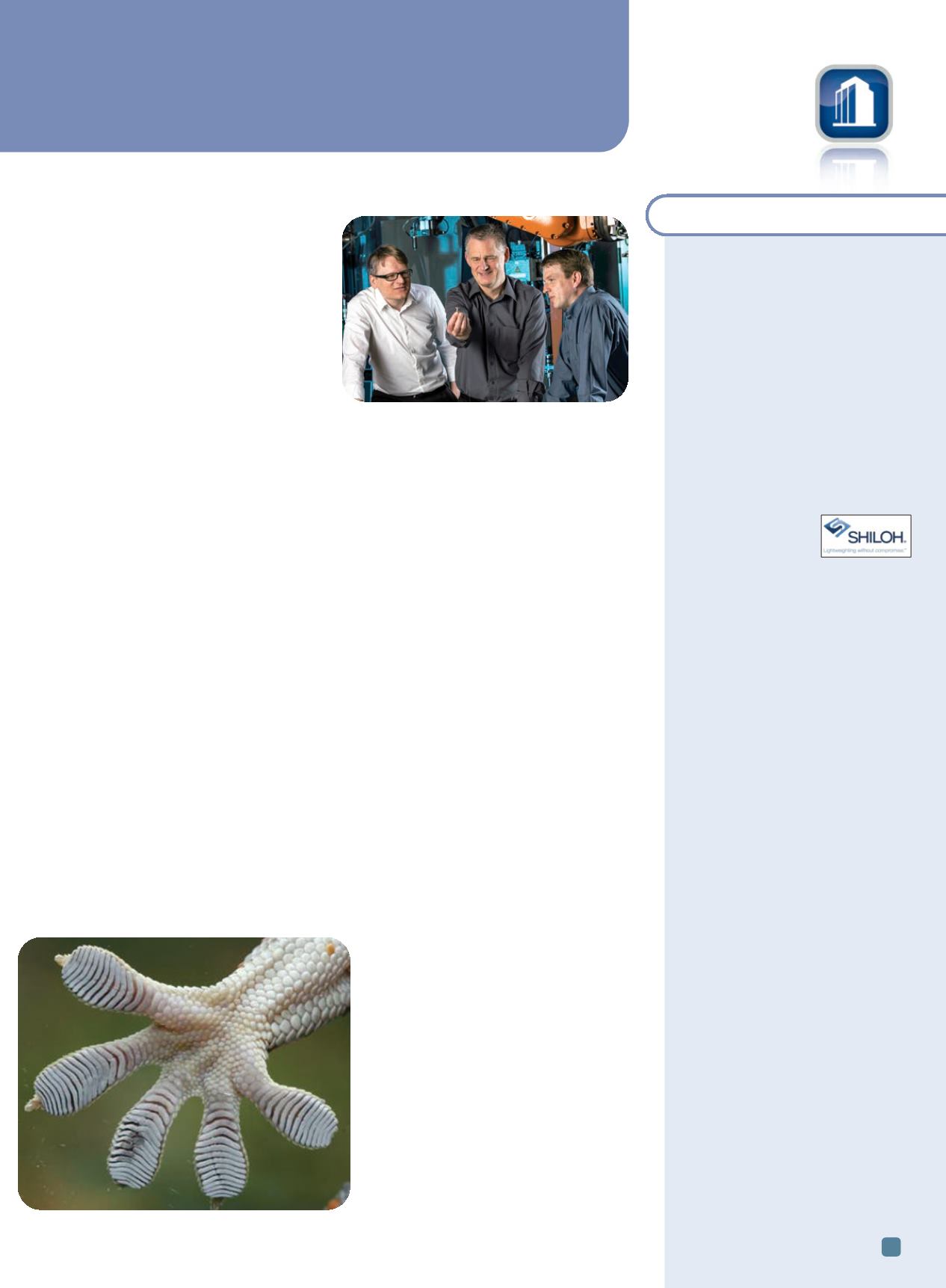
ADVANCED MATERIALS & PROCESSES •
JULY 2014
11
news
industry
briefs
Plastic Omnium Auto Exteriors,
France, is building a new facility to
supply the
Volkswagen
plant in
Chattanooga, Tenn., creating 300
jobs over the next three years. The
automotive supplier is spending $65
million on the 27-acre facility, to be
located next to the plant. Plastic
Omnium has 110 plants in 30
countries, including 15 in North
America. The company makes
bumpers, fenders, and plastic body
panels for car manufacturers around
the world.
plasticomnium.com.
Shiloh Industries Inc.,
Valley City,
Ohio, a supplier of
lightweighting, noise,
and vibration
solutions, signed an agreement with
FinnvedenBulten AB
to acquire
100% of the shares of
Finnveden
Metal Structures (FMS).
With the
$56.6 million acquisition, Shiloh
adds stamping and magnesium die
casting capabilities. Shiloh provides
design, engineering, and
manufacturing of engineered
welded blanks, complex stampings,
modular assemblies, and high-
pressure aluminum die cast and
machined components serving the
body-in-white, chassis, emission,
powertrain, structural, and seating
needs of automotive OEM and Tier 1
customers.
shiloh.com.
Liquidmetal Technologies Inc.,
Rancho Santa Margarita, Calif.,
signed an amended sublicense
agreement with
Visser Precision
Cast LLC (VPC),
Denver. Under the
new agreement, Liquidmetal is freed
from its commitment to use VPC as
its exclusive contract manufacturer,
and VPC is freed from its commitment
to use Liquidmetal as its exclusive
sales and R&D channel. Liquidmetal
develops bulk alloys and composites
that employ the performance
advantages offered by amorphous
alloys—unique materials that retain
a random structure when they
solidify. VPC offers amorphous
casting, precision machining, and
additive manufacturing (direct metal
laser sintering) services.
liquidmetal.com,
visserprecisioncast.com.
P
ROCESS
T
ECHNOLOGY
Two-step bonding technique suitable for industrial use
Adhesive bonding technology is an ef-
fective way to seamlessly join two parts,
even those made of different materials.
However, because liquid adhesives need
time to cure, they cannot be applied in
every production step. Researchers at the
Fraunhofer Institute for Manufacturing
Technology and Advanced Materials
IFAM, Germany, created a two-step
method in which adhesive is deposited on
one of the parts and then dried to form a
non-sticky layer. During a subsequent step,
the adhesive is hardened and parts are
bonded together. The technique can be
used to create a high-strength adhesive bond suitable for industrial use, which is not easy be-
cause the adhesives must fulfill different and sometimes contradictory requirements.
“Once the adhesive is applied, it can’t be tacky and it has to withstand long storage
times,” explains chemical engineer Andreas Lühring. “It also has to be very reactive and
harden quickly during joining.” The concept combines resins and hardening agents that
melt at different temperatures.
The resulting hot melt adhesive can be used to manufacture fastening bolts, for exam-
ple. The material is heated and applied to the fastener. After it cools, it solidifies again. The
fastener can then be transported and stored. To harden the actual adhesive, it must be
heated to more than 150°C in a controlled manner. In this way, two parts can be bonded
to each other within seconds.
“There is one disadvantage to reactive adhesives like these. They can be stored for a
long time, but not indefinitely,” says group manager Matthias Popp. To address this issue,
a visual monitoring method was added—if the substance has lost its functionality, it
changes color. These pre-applicable structural adhesives are also suitable for other appli-
cations, including a variable construction kit that offers adhesives based on different ma-
terials and hardening principles. The different compositions are tailored to yield the best
productivity and characteristics for a wide variety of applications.
www.fraunhofer.de.
New adhesive outperforms gecko feet
The ability to stick objects to a variety of surfaces such as drywall, wood, metal, and glass
with a single adhesive has been the elusive goal of numerous researchers until now. A team
fromUniversity of Massachusetts Amherst developed a new, more versatile version of their
invention, Geckskin, which strongly adheres to a wider range of surfaces, yet releases eas-
ily like a gecko’s feet. Unlike other
gecko-like materials, the invention does
not rely on mimicking the nanoscopic
hairs found on gecko feet, but instead
builds on
draping adhesion,
which de-
rives from the gecko’s integrated skin-
tendon-bone system. The new ability
was created by combining soft elas-
tomers and ultra-stiff materials such as
glass or carbon fiber fabrics.
umass.edu.
UMass Amherst researchers compared
three versions of Gecksin to the abilities of
a living Tokay gecko on several surfaces.
One exceeds the gecko’s performance on
all tested surfaces.
Matthias Popp, Andreas Hartwig, and Andreas
Lühring won a 2014 Joseph von Fraunhofer prize
for their work on two-part bonding techniques.
Courtesy of Dirk Mahler/Fraunhofer.