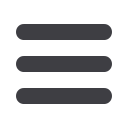
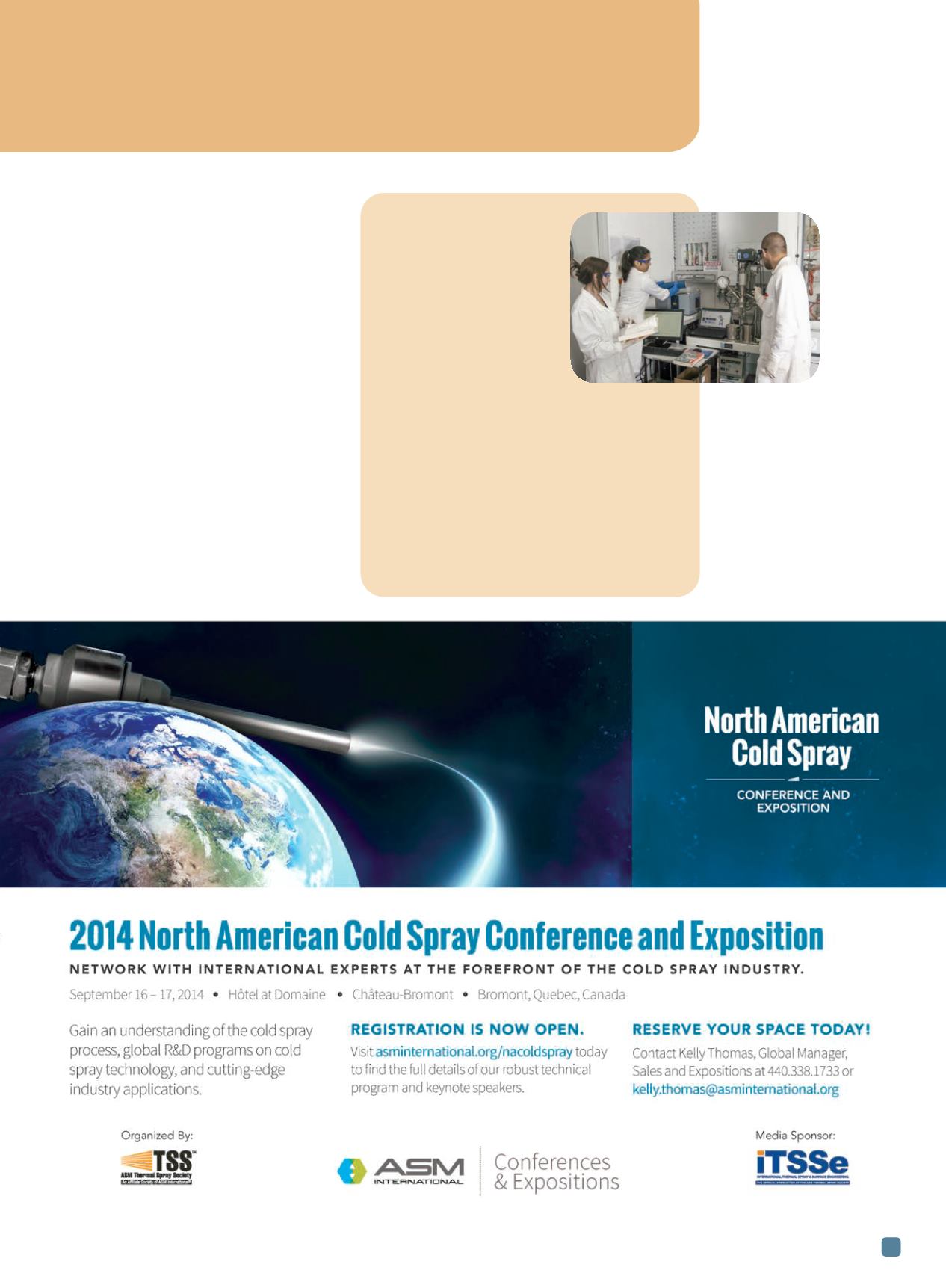
ADVANCED MATERIALS & PROCESSES •
JULY 2014
7
bars. Next, bars were normalized and
stress relieved. Tensile and impact speci-
mens were machined from the bars and
then normalized, gas quenched, and tem-
pered at 450°-500°F. ASTM tensile and
impact tests show a hardness HRC of 54-
55, yield strength of 243-255 ksi, ultimate
tensile strength of 287-300 ksi, elongation
of 9-10%, reduction of area of 32-35%,
and Charpy V-notch impact toughness
energy of 15-18 ft/lb. Properties varied
depending on austenizing and tempering
temperatures.
After the heat treatment, M-Steel had a
tempered martensite microstructure com-
prised of martensitic lathes, retained austen-
ite, and carbides as centers of growth of the
martensitic lathes, and ASTM grain size of
7-8. M-Steel can be welded by conventional
methods in annealed and normalized con-
ditions
. For more information: Gregory Var-
tanov, 289.400.1154,
supersteel@cogeco.ca.
The earth’s crust works like a
pressure cooker—minerals
typically do not form under
standard conditions, but at
high temperatures and pres-
sures. However, an environ-
ment of extreme heat and
pressure is considered to be
highly unsuitable for organ-
ic molecules. Scientists at
Vienna University of Tech-
nology,
Austria, found that
under such seemingly hostile
conditions, organic materials
with remarkable material
properties, such as Kevlar,
can be synthesized. At 200°C
and 17 bars, the team syn-
thesized organic polymers, which are usually ex-
tremely hard to create and require highly toxic
additives. Instead of hazardous solvents, water vapor
was used, making the new method eco-friendly as
well.
www.tuwien.ac.at/en.The Vienna team
prepares an
experiment using a
reactor and infrared
probe. Courtesy of
Vienna University of
Technology.