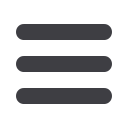
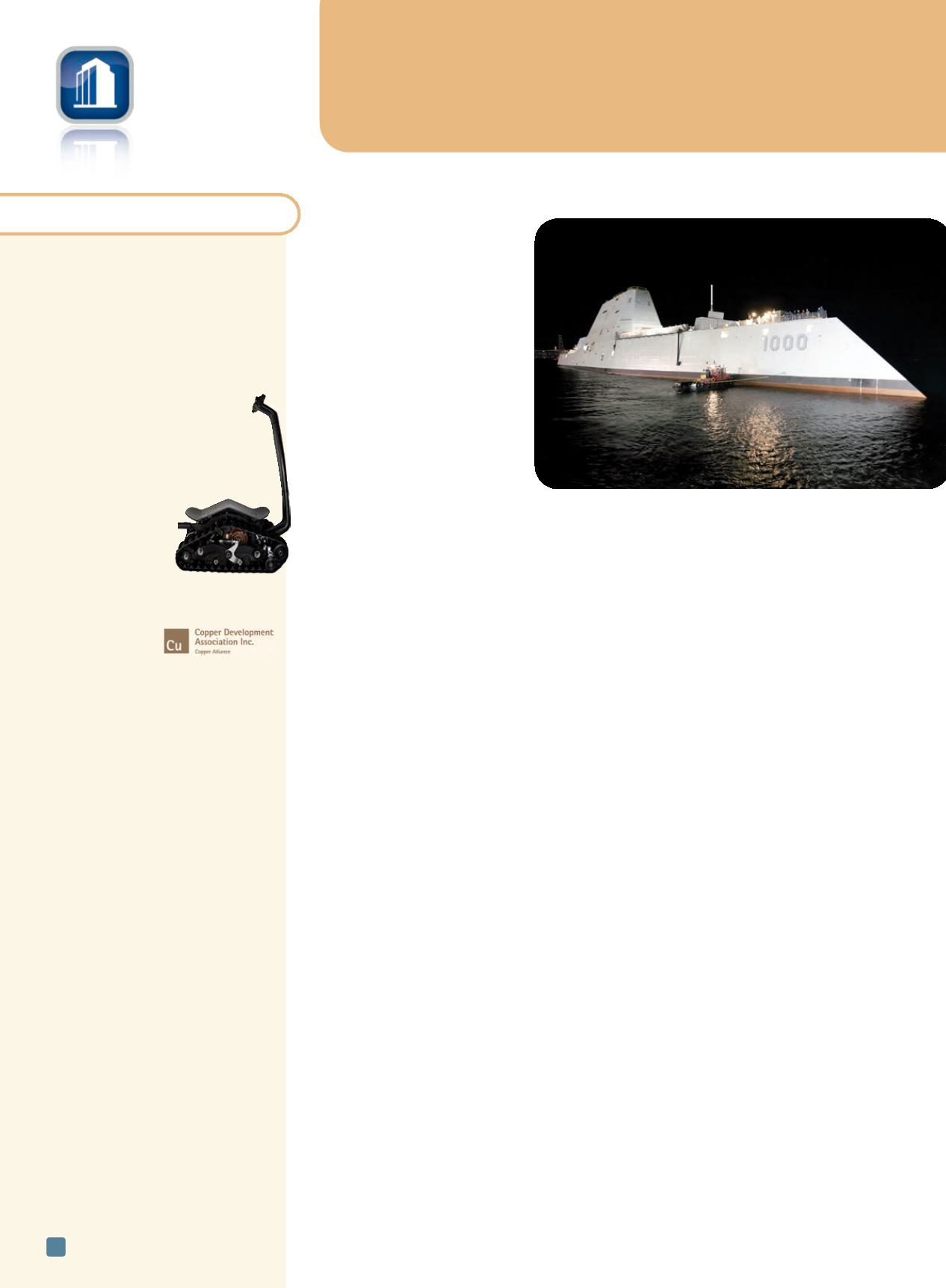
Nanocrystalline ceramic for military windows
Scientists at the U.S. Naval
Research Laboratory, Wash-
ington, developed a method
to fabricate nanocrystalline
spinel that is 50% harder than
the current spinel armor mate-
rials used in military vehicles.
With the highest reported
hardness for spinel, it demon-
strates that the hardness of
transparent ceramics can be
increased simply by reducing
the grain size to 28 nm. This
harder spinel offers the poten-
tial for better armor windows
in military vehicles.
To create the new spinel,
researchers sinter commercial
nanopowders into fully dense
nanocrystalline materials. While sintering is a common method used to create large ce-
ramic and metal components from powders, the team is the first to succeed in making
harder spinel through the enhanced high pressure sintering (EHPS) approach, according
to researchers. The EHPS approach uses high pressures (up to 6 GPa) to retard bulk diffu-
sion rates, break powder agglomerates, and reposition nanoparticles very close to each
other to help eliminate porosity in the sintered ceramic. The increased surface potential of
nanoparticles can then be exploited for surface-energy-driven densification without coars-
ening.
www.nrl.navy.mil.
Recycling is key to energy efficiency in metal manufacturing
The production of iron, steel, and aluminum is a highly energy-intensive process, ac-
counting for 10% of total manufacturing energy use. Recycling in the manufacturing
process of these metals is a key driver of energy efficiency improvement. Primary produc-
tion, in which steel is made from iron ore and aluminum from bauxite ore, is energy inten-
sive. However, secondary production, which involves the use of recycling scrap to make
steel and aluminum, is much more energy efficient. The Environmental Protection Agency
estimates that secondary steel production uses about 74% less energy than the production
of steel from iron ore, while the U.S. Department of Energy reports that secondary alu-
minum production requires 90% less energy than primary production.
Secondary production accounts for nearly 60% of U.S. aluminum production,
counting both old and new scrap. Similarly, recycling is used in most steel production.
According to the U.S. Geological Survey, 40% of U.S. steel production in 2011 came
from basic oxygen furnaces, whose inputs are almost 80% pig iron (molten iron),
whereas 60% of production came from electric arc furnaces, which use more than 90%
scrap.
eia.gov.New steel competes with AISI 4340
A newly designed and patented, quenched and tempered high strength low alloy
steel (M-Steel), by Advanced Materials Development Corp., Ontario, reportedly ex-
hibits strength superior to AISI 4340 steel at the same level of ductility and toughness.
Further, the cost of raw materials of the M-Steel is lower than the cost of AISI 4340
steel, while the cost of melting, hot forging/rolling, annealing, and heat treatment are
similar. To verify the mechanical properties, an ingot of the M-Steel with a 6-in. di-
ameter and weighing 125 lb was air melted, homogenize annealed, and hot forged to
news
industry
briefs
BPG Werks,
Boston, creators of
the innovative all-terrain dual
tracked vehicle (DTV) called the
Shredder, harnessed a high-
performance polymer, VICTREX WG,
from
Victrex,
UK, to construct a
strong and efficient overmolded
steel drive shaft segment gear.
Replacing a coated brass gear, the
rugged thermoplastic enables
more durable and reliable
transmission performance with
smooth torque and acceleration, as
well as reduced vibration.
victrex.com.
BPG Werks specified
the VICTREX WG
polymer for its DTV
Shredder. Courtesy
of Victrex.
The Copper Development
Association (CDA),
New York,
launched the latest
video in its
Do it
Proper With Copper
series:
Soldering of No-Lead Copper Alloy
Fittings, Valves and Components.
The video not only demonstrates
proper soldering techniques for
new alloys, but also offers an
explanation as to why they must
be treated differently from the old
ones. “The answer lies in the
metallurgy, or physical properties
of the alloy,” says project manager
David Powell. “Some of the new
alloys, especially those containing
silicon, have much lower thermal
conductivity than their earlier
counterparts, or than the copper
parts that they are being joined
with.”
copper.org.
Alcoa Inc.,
New York, signed a
long-term agreement to supply
aluminum sheet to
Spirit
AeroSystems Inc.,
Wichita, Kan.,
in a contract valued at
approximately $290 million over
five years. Spirit is one of the
largest designers and
manufacturers of aerostructures for
commercial, military, business, and
regional jets in the world. Alcoa will
provide Spirit with aluminum sheet
products for fuselage skins from its
Davenport, Iowa, facility.
alcoa.com,
spiritaero.com.
M
ETALS
P
OLYMERS
C
ERAMICS
ADVANCED MATERIALS & PROCESSES •
JULY 2014
6
Spinel windows serve as electro-optical/infrared deckhouse
windows in a new class of U.S. Navy destroyers, such as the
USS Elmo Zumwalt pictured here. Courtesy of U.S. Navy
and General Dynamics.