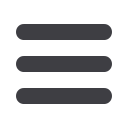
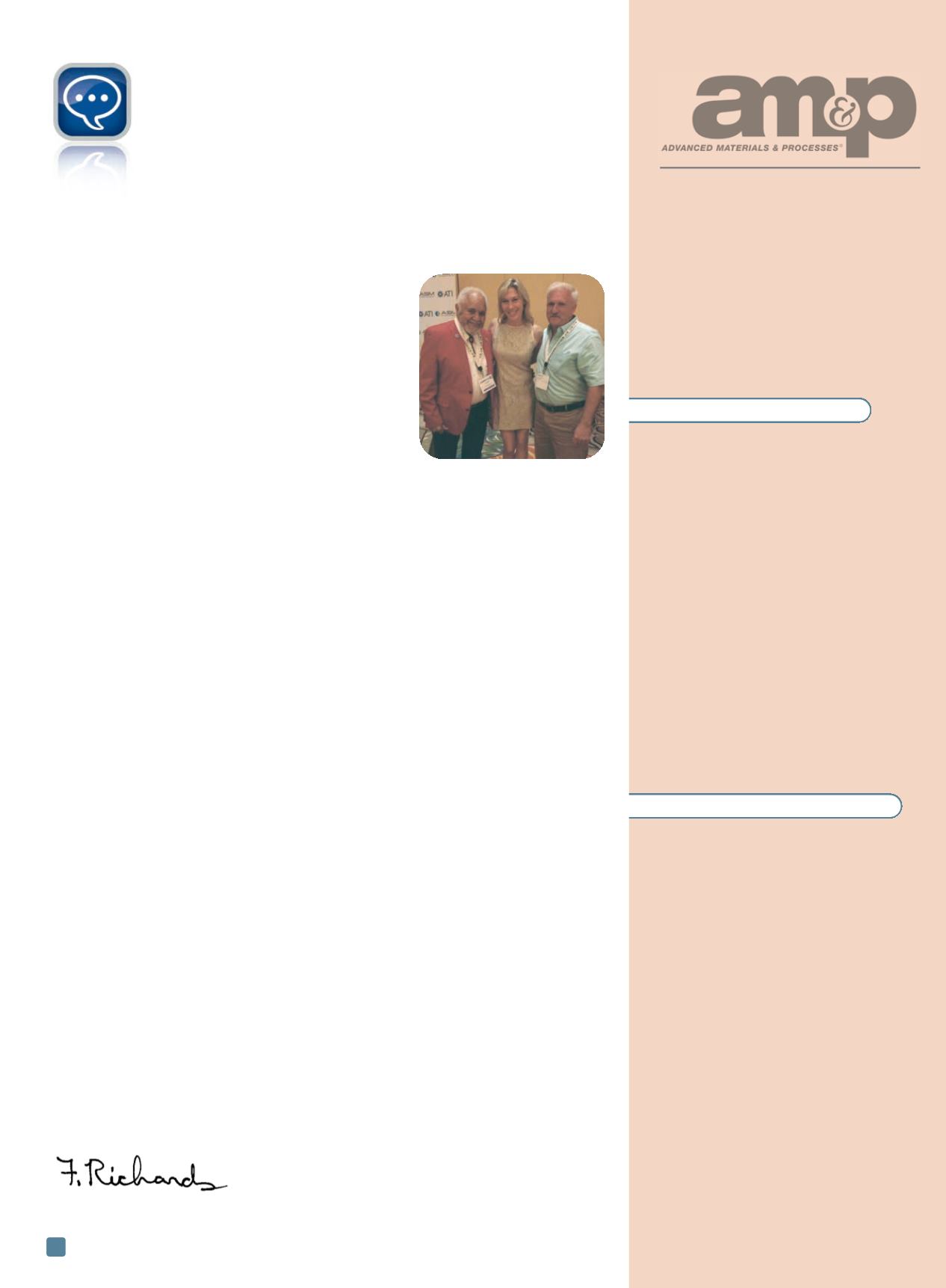
9639 Kinsman Road
Materials Park, OH 44073
Tel: 440.338.5151 • Fax: 440.338.4634
Frances Richards
,
Senior Editor
frances.richards@asminternational.orgJulie Kalista
,
Editor
julie.kalista@asminternational.orgBarbara L. Brody
,
Art Director
Joanne Miller
,
Production Manager;
Editor, ASM News
joanne.miller@asminternational.orgPress Release Editor
magazines@asminternational.orgEDITORIAL COMMITTEE
Mario Epler,
Chair,
Carpenter Technology Corp.
Yu-Ping Yang,
Vice Chair,
Edison Welding Institute
Ellen Cerreta,
Past Chair,
Los Alamos National Lab
William Lenling,
Board Liaison
Laura Addessio,
PCC Structurals Inc.
Arvind Agarwal,
Florida International University
Gerald Bruck,
Siemens Westinghouse Power Corp.
Steven Claves,
Alcoa Inc.
Adam Farrow,
Los Alamos National Lab
Nia Harrison,
Ford Motor Co.
Alan Luo,
The Ohio State University
Roger Narayan,
UNC-NCSU
Scott Olig,
Vision Point Systems
Nina Pang,
Boston University
Somuri Prasad,
Sandia National Lab
Fei Ren,
Oak Ridge National Lab
Michael Rigsbee,
North Carolina State University
Kumar Sridharan,
University of Wisconsin
Jaimie Tiley,
U.S. Air Force Research Lab
Cong Wang,
Saint-Gobain High Performance
Materials
ASM BOARD OF TRUSTEES
C. Ravi Ravindran,
President
Sunniva R. Collins,
Vice President
Robert J. Fulton,
Treasurer
Gernant E. Maurer,
Immediate Past President
Jeffrey A. Hawk
William J. Lenling
Linda S. Schadler
Iver Anderson
Mitchell Dorfman
James C. Foley
Jacqueline M. Earle
John R. Keough
Zi-Kui Liu
Thomas S. Passek,
Secretary and Managing
Director
STUDENT BOARD MEMBERS
Virginia K. Judge,Anthony Lombardi, Myrissa N. Maxfield
Individual readers of Advanced Materials & Processes may,
without charge, make single copies of pages therefrom for per-
sonal or archival use, or may freely make such copies in such
numbers as are deemed useful for educational or research pur-
poses and are not for sale or resale.Permission is granted to cite
or quote from articles herein, provided customary acknowl-
edgment of the authors and source is made.
materials wi tness
ADVANCED MATERIALS & PROCESSES •
JULY 2014
2
Standing on the edge of a revolution
A
lthough some people may feel that additive
manufacturing—aka 3D printing—is overly
hyped these days, it’s clear that many others believe
we are truly on the edge of another Industrial Revo-
lution. The ability to design and print complex parts
layer-by-layer is being compared to the transforma-
tive power of the cotton gin and steam engine. It’s
creating a lot of buzz and significant research is
being poured into figuring out the best way to take
advantage of this amazing technology.
In fact, I just returned from a week at the 25th
AeroMat Conference and Exposition in Orlando, Fla.,
which featured a theme of “the latest word in aero-
space materials.” Several presentations discussed ad-
ditive manufacturing, including an excellent and well attended plenary session starring
William Frazier, FASM, of NAVAIR, and David Abbot of GE Aviation. Frazier’s talk, “The
Transformative Potential of Additive Manufacturing,”called the quickly developing tech-
nology “disruptive, transformative, and enabling,” and said it will change the very way
we do business. He spoke in detail about potential benefits, using the Navy’s challenges
and goals as concrete examples. While discussing the country’s aging weapons systems
and aircraft, he bluntly stated that it is simply too expensive and time consuming to
make replacement parts for old systems using traditional subtractive techniques.
In contrast, the Navy’s bold vision is to one day be able to print parts on demand,
where and when they are needed. He also affirmed that we have a long way to go to-
ward reaching that goal. He stressed that using additive methods, rather than subtrac-
tive processes, enables shorter lead times, mass customization, reduced part counts,
more complex shapes, less material waste, and the ability to reverse engineer parts as
needed. Frazier mentioned that although the Navy is implementing additive processes
for blade and vane tip repairs, the biggest roadblock is the need for faster, low cost part
qualification and certification. Other challenges include the need for validated models
and in situ nondestructive inspection as the additive process is taking place, as well as
a way to account for machine-to-machine variability.
David Abbott then spoke about additive manufacturing efforts at GE Aviation and
interestingly points out that design engineers will need to change the way they think
about designing parts from the outset—that these new additive processes will revolu-
tionize the way we
think
in addition to how parts are physically made. He also said that
by 2020, GE plans to additively produce 40,000 fuel nozzles per year. Abbott stressed the
need for companies to learn from each other—he is a part of EWI’s additive manufac-
turing consortium and is also involved with America Makes, the National Additive Man-
ufacturing Innovation Institute.
On a celebratory note, ASM and ATI partnered to put on a VIP reception featuring
Lieutenant Colonel Leo Gray, one of the 27 remaining Tuskegee Airmen fromWorldWar
II. Gray shared some very interesting, funny, and personal stories from his time flying
P-51 Mustangs over Germany, during nearly four years of active duty. The event was
enjoyed by all and serves as a stark reminder of why aerospace innovation remains such
an important endeavor.
frances.richards@asminternational.orgTuskegee Airman Lt. Col. Leo
Gray (left) with Frances Richards
and Donald Baldwin (of GE) at
AeroMat 25.