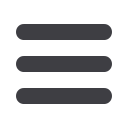
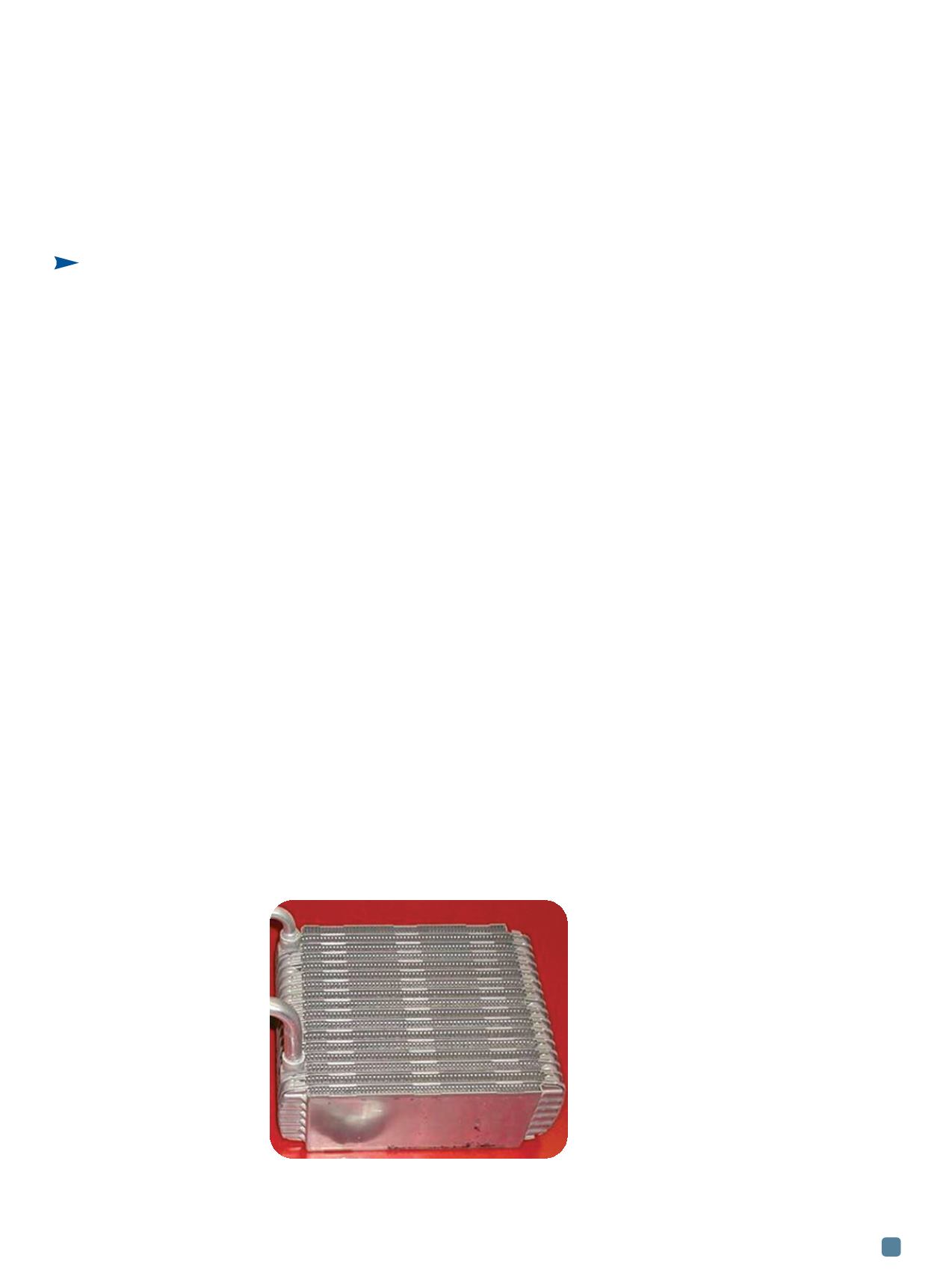
ADVANCED MATERIALS & PROCESSES •
JULY 2014
15
Understanding
Key Process Parameters of
Vacuum Aluminum Brazing
he American Welding Society defines
brazing as:
“A group of welding processes that
produces coalescence of materials by heat-
ing them to the brazing temperature in the
presence of a filler metal having a liquidus
above 840°F (450°C) and below the solidus
of the base metal. The filler metal is distrib-
uted between the closely fitted faying sur-
faces of the joint by capillary action.
[1]
”
The
solidus
is the highest temperature at
which the metal is completely solid—the tem-
perature at which melting starts. The
liquidus
is
the lowest temperature at which the metal is
completely liquid—the temperature at which
solidification starts.
Types of aluminum brazing
Flux brazing
involves the flow of flux into
the joint, which is then displaced by the liq-
uidus filler metal to remove oxides on the part,
creating a strong, solid braze. Flux comes in
several different forms—paste, liquid, or pow-
der. Some brazing rods are coated with flux or
have flux cores in order to apply necessary flux
during brazing. Flux brazing processes include
torch brazing (manual and automatic), induc-
tion, salt bath (dip brazing), and controlled at-
mosphere brazing (CAB).
Vacuum aluminum brazing
(VAB) is per-
formed in a vacuum furnace and is considered
fluxless brazing because flux is not used to cre-
ate joints. Fluxless brazing processes can be
performed using inert gas atmospheres or in
vacuum furnaces. Application examples in-
clude semiconductor manufacturing and ce-
ramic to copper brazing. Due to the vacuum’s
clean environment, flux is not needed. Magne-
sium is used as an additive, or
getter,
in vacuum
aluminum brazing.
Vacuum aluminum brazing advantages
Brazing has many advantages compared to
other metal-joining processes. Because it does
not melt the base metal of the joint, brazing al-
lows for more precise control of tolerances and
provides a clean joint without the need for ad-
ditional finishing. The meniscus (crescent
shaped) formed by the filler metal in the brazed
joint is ideally shaped for reducing stress con-
centrations and improving fatigue properties.
Applications well suited for brazing include:
• Parts with very thin or very thick cross
sections
• Compact components with many
junctions to be sealed (e.g., heat
exchangers) or deep joints with restricted
access
• Dissimilar metals such as copper and
stainless steel
• Assemblies with a large number of joints
VAB minimizes part distortion because
parts are uniformly heated and cooled com-
pared to localized joining processes. VAB also
creates a continuous hermetically sealed bond.
Components with large surface areas and nu-
merous joints can be successfully brazed this
way. Hardening can be accomplished in the
same furnace cycle if hardenable alloys are used
and the furnace system has a forced cooling
system, which reduces cycle time.
Vacuum furnace brazing offers extremely
repeatable results due to critical furnace pa-
rameters attained with every load—vacuum
levels and temperature remain uniform. Capil-
lary joint paths (even long paths) are effectively
purged of entrapped gas during initial evacua-
tion of the furnace chamber resulting in more
complete joint wetting.
VAB is ideal for oxide-sensitive materials,
as corrosive flux residue is eliminated. Post-
brazed parts are clean with a matte grey finish.
The process is relatively nonpolluting and does
not require post-braze cleaning. Examples of
VAB parts (Fig. 1) often include heat exchang-
Craig Moller*
Jim Grann
Ipsen USA
Cherry Valley, Ill.
Successful part
brazing relies
on proper joint
design, part
cleanliness, and
correct fixturing
of part
assemblies.
Routine furnace
maintenance
allows
repeatable,
quality brazing
results over
time.
*Member of ASM International
T
Fig. 1 —
Vacuum aluminum brazed radiator.
Courtesy of API Tech.