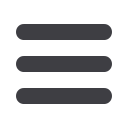
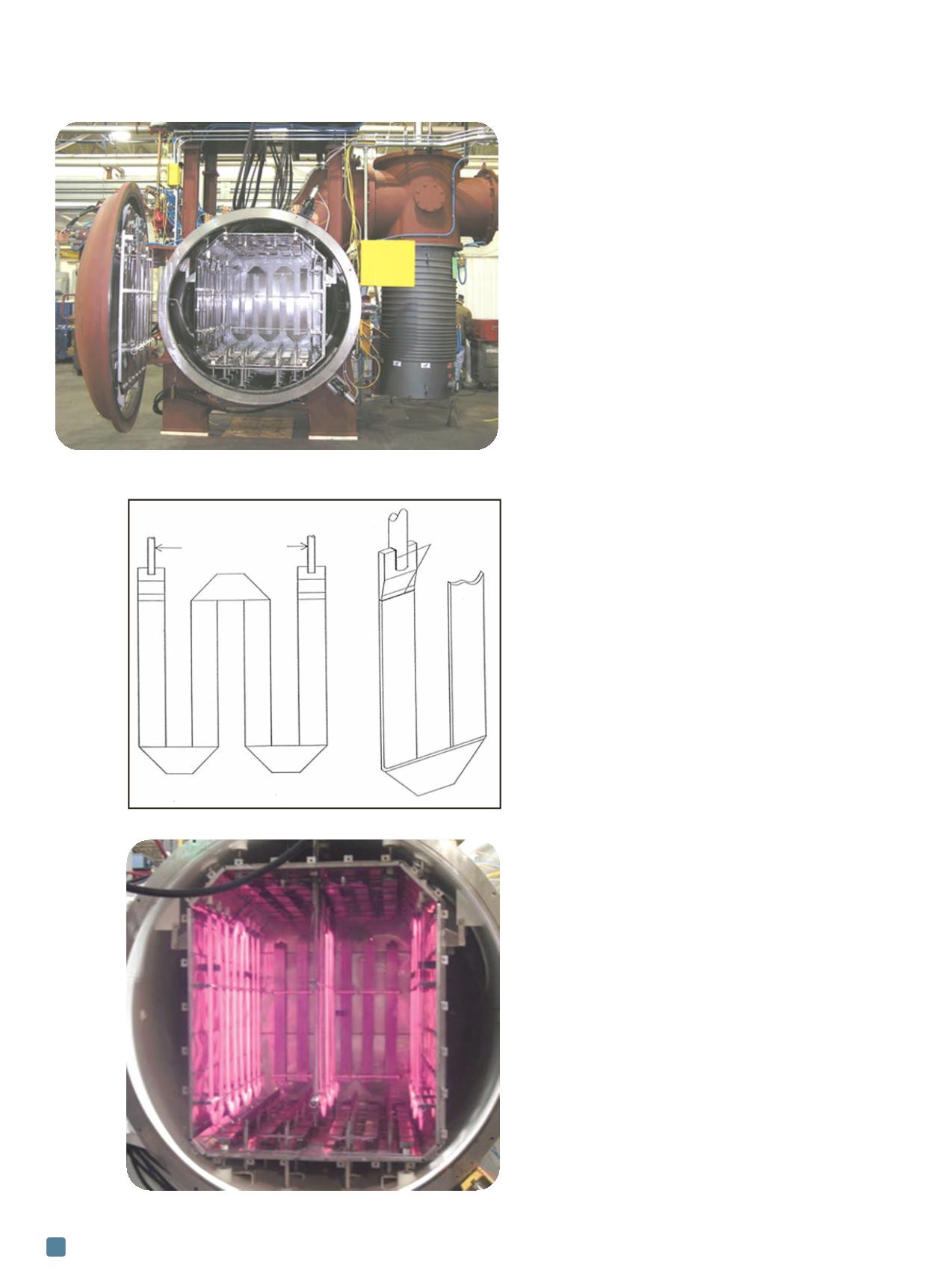
ADVANCED MATERIALS & PROCESSES •
JULY 2014
18
in order to maintain joint gaps, joint alignment, flow pas-
sage alignment, and overall assembly tolerances. Fixturing
materials must be chosen carefully due to different coeffi-
cients of expansion for varying materials. Fixture designs
are also extremely part dependent, thought out in great de-
tail, and are proprietary in some cases because they are an
integral part of the manufacturing process.
Along with proper joint design and fixturing, braz-
ing requires part assemblies to be cleaned properly prior
to assembly then properly handled in order to avoid
contamination prior to brazing. All grease, oil, and par-
ticulates must be cleaned off the parent and filler metal
surfaces, and assemblers must be careful not to transfer
oils from their skin to these surfaces when stacking
parts together. Typical cleaning methods include vapor
degreasing, hydrocarbon wash, aqueous washing, acid
etching, and vacuum de-oiling.
Furnace characteristics
As noted previously, one key process parameter of VAB
is a deep vacuum level and adequate pumping throughput
to keep up with the significant outgassing that takes place
during the heating cycle due to magnesium vaporization.
Typical VAB furnaces include large diffusion pumps and
backing pumps to accomplish these requirements. Figure
9 shows typical pumping arrangements for these furnaces.
The pumping capacity required for a given aluminum
brazing furnace depends on the load, specifically the load
surface area being brazed. The larger the load surface area,
the larger the required pumping capacity. Due to the fact
that most of the magnesium vaporization occurs in the
10
-4
to 10
-5
torr range, diffusion pump(s) must handle the
gas load during mag burst with adequate backing pumps.
To facilitate vacuum pumping in the furnace, the
cooling jacket around the vacuum vessel runs at higher
than ambient temperatures. This warm wall design helps
prevent water vapor condensation inside the vessel when
the door is open for loading/unloading. Water vapor is
the enemy of aluminum brazing—it slows pumping speed
and breaks down, releasing oxygen into the furnace. The
warm wall design lessens the bonding strength of the
magnesium oxide that forms during brazing and ulti-
mately condenses on the chamber’s inner wall, making it
easier to mechanically clean.
VAB furnaces must maintain a low leak-up rate to
prevent the outside atmosphere from entering the fur-
nace during brazing. Vacuum quality contains a very low
PPM of oxygen throughout the brazing cycle. Good de-
sign practices for vacuum chambers that have a low leak-
up rate typically include minimal use of pipe thread
joints, using a 63 micro-finish or better on sealing sur-
faces for O-rings, and using the correct O-ring material
for the sealing area’s temperature.
Heating elements
Other important process parameters include precise
temperature control and temperature uniformity. Placing
the sensing junctions of thermocouples near the heating
Fig. 9 —
Large diffusion pump on a vacuum aluminum brazing furnace.
Fig. 10 —
Wide band heating element.
Fig. 11 —
New vacuum aluminum brazing furnace.
Power terminals
Welds