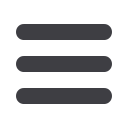
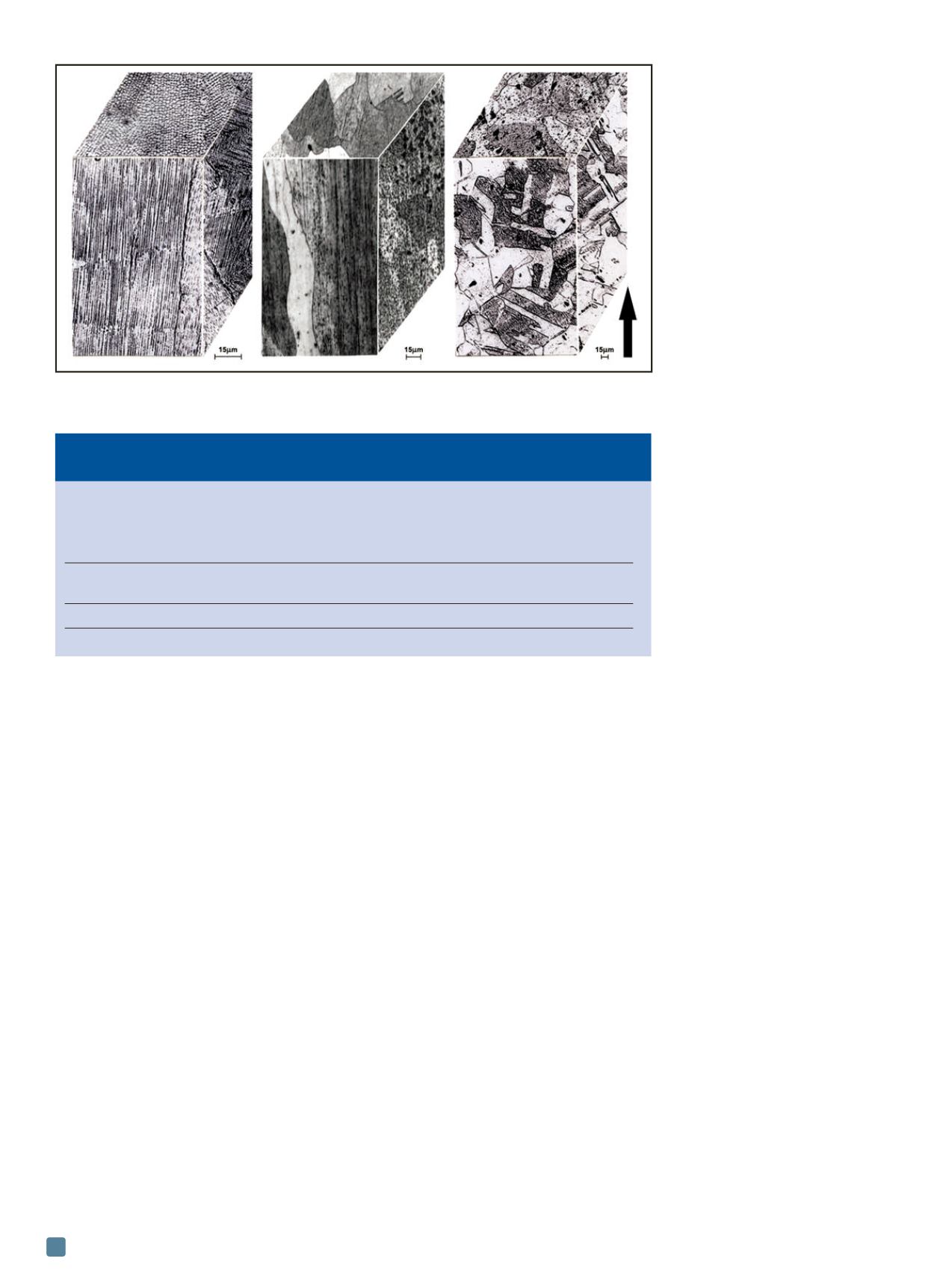
ADVANCED MATERIALS & PROCESSES •
JULY 2014
22
table oxide (Cu
2
O) in the grain boundaries and a corre-
sponding SEM image for 99.99% Cu powder B (Fig. 2b)
with a lower density of grain boundary oxides (arrows).
While the atomization and rapid solidification of the pow-
der manufacturing process itself incorporates various
oxide concentrations, residual oxygen and water vapor in
the EBM system is also absorbed in the unconsolidated
powder during processing. This feature is shown in Figs.
2c and 2d, which compare optical metallographic cross-
section views for the initial (precursor) powder B and used
powder particles, showing recognizably increased oxides
at the grain boundaries.
Evident from these figures is that the powder parame-
ters (especially the oxide or oxygen content), combined
with the EBM build parameters, must be carefully consid-
ered in order to fabricate products with desirable proper-
ties, particularly high electrical conductivity.
EBM processing of copper samples
Powder A was selected for further study. Although this
powder exhibited relatively poor raking characteristics due
to its irregular shape, its significantly lower cost made it an
attractive candidate for EBM parameter development.
EBM parameters were assigned to each cylinder based on
a previous feasibility study
[5]
designed to provide a starting
point for subsequent parameter
optimization. The EBM process
was operated in automatic mode,
in which parameters such as beam
current and speed are calculated
for each layer and adjust with
changes in part geometry to main-
tain a stable process. The desired
surface temperature is specified
and a “speed function” is selected.
Both substrate starting tem-
perature and desired surface tem-
perature are critical for the build,
as over-melting or over-sintering
makes powder recovery difficult
or impossible. These tempera-
tures also affect surface quality,
porosity, and microstructure. The
speed function is a parameter
that adjusts beam rate during
hatching, with higher values re-
sulting in higher beam speeds.
Other adjusted parameters in-
clude hatch spacing and contours
functions. An experiment was de-
signed where 24 cylinders in six
builds were fabricated with 24
different sets of process parame-
ters. The goal was to find a set of
process parameters to produce
fully dense copper cylinders with
an acceptable surface finish and
desired microstructure.
Early experiments resulted in cylinders with severe de-
lamination, hypothesized to be caused by a significant
thermal gradient within each layer. The high thermal con-
ductivity of the copper powder (particularly after sinter-
ing/melting) was suspected to be the cause. To balance
heat transfer throughout the build area, three stainless steel
plates (210 × 210 × 10 mm) were installed under the cop-
per start plate. After analyzing all specimens, a parameter
set was developed to consistently produce acceptable parts.
From this theme, samples were prepared for examination
of metallurgical, mechanical, thermal, and electrical prop-
erties. Finally, prototypes of the RF photoinjector were fab-
ricated for field testing.
Sample evaluation
Figure 3 shows corresponding and comparative 3D op-
tical metallographic image composites illustrating oxide
influenced, directionally solidified microstructures or mi-
crostructural architectures. In Fig. 3a, using a mixture of
the high-oxide containing powder C and powder A, EBM
processing produces columnar oxide architectures ori-
ented in the build direction (arrow). In contrast, Fig. 3b
shows columnar grain structures intermixed with colum-
nar oxides when the high-purity powder B was employed.
In Fig. 3c, powder B was again used to build a smaller com-
Fig. 3
—
3D construction shows EBM-built Cu components from a mixture of 99.80% Cu powder C
and a prior, high oxide powder A (a); 99.99% Cu powder B (b); and 99.99% Cu powder B built at
elevated temperature (c). Arrow denotes build direction.
TABLE 1 — SUMMARY OF MEASURED EBM FABRICATED COPPER
MATERIAL PROPERTIES
Wrought
Wrought
EBM
Ti6Al4V
EBM
C10100
Ti6Al4V
*
(ASTM F1472)
Copper
Copper
Density
>99.9% — 8.84 g/cm
3
8.90 g/cm
3
Electrical conductivity
—
— 97% IACS 102% IACS
@ 20˚C
Thermal conductivity
—
— 390 W/m*K 391 W/m*K
Yield strength (Rp 0.2)
950 MPa 860 MPa
76 MPa
69 MPa
Summary of measured EBM-fabricated copper material properties compared to wrought copper and the Arcam-
developed titanium alloy.
*
Arcam Ti6Al4V Material Data Sheet,
(www.arcam.com/CommonResources/Files/www.arcam.com/ Documents/EBM%20Materials/Arcam-Ti6Al4V-Titanium-Alloy.pdf)(a) (b) (c)