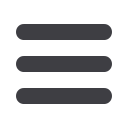
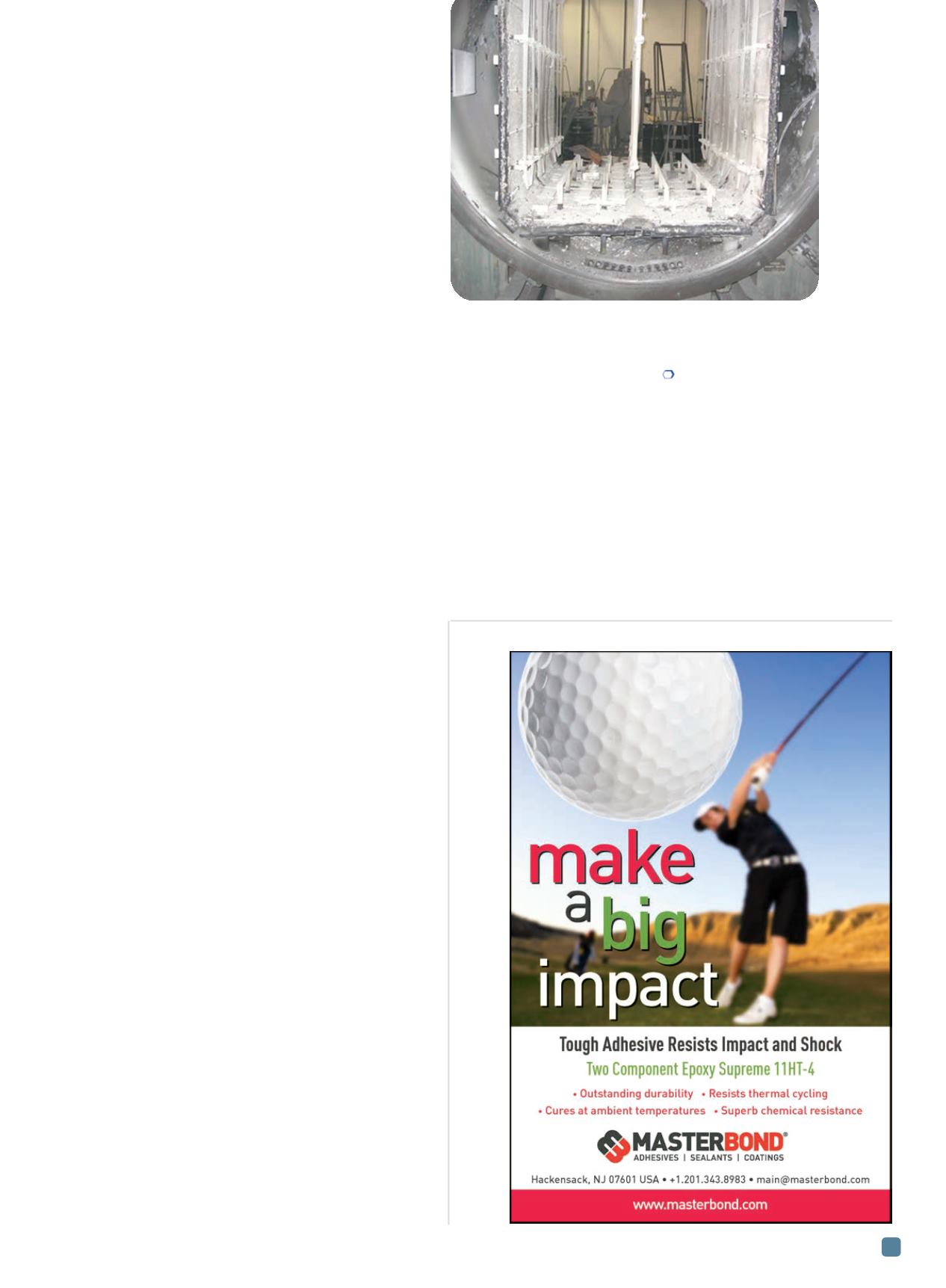
ADVANCED MATERIALS & PROCESSES •
JULY 2014
19
elements results in faster and more accurate control of
process parameters. Using many heating control zones
arranged within the hot zone provides exceptional temper-
ature uniformity [+/- 5°F (3°C)]. The wideband design pro-
vides a substantial radiating surface to the processed parts,
which facilitates faster heating and better temperature uni-
formities. Batch-type VAB furnaces that contain 10 to 20
individually controlled heating zones are common.
Heating element surface area as a percentage to load
surface area is also important. The larger the surface area
of the heating elements, the lower the watt density on that
surface, resulting in element temperatures only slightly
above load temperature at steady-state soaking conditions.
This ensures that the load’s outside surface does not be-
come overheated (Fig. 10). Vacuum furnaces that can
process two loads side by side also use center heating ele-
ment banks between the two loads. This design enables
even heating of all surfaces on dual workloads.
Furnace maintenance
The majority of maintenance time spent on a VAB fur-
nace is devoted to cleaning magnesium oxide deposits that
form inside the chamber and hot zone during the brazing
process. Figs. 11 and 12 show before and after photos of
typical VAB furnaces.
Magnesium oxide deposits tend to retain water vapor.
Excess retention of water vapor slows down vacuum
pumping. Eventually, magnesium oxide will build up
enough to negate the furnace’s ability to pump in accept-
able parameters and may prevent reaching the required
vacuum levels for quality brazing. This is when magnesium
oxide needs to be removed from the furnace system.
Mechanical cleaning is usually used to remove magne-
sium oxide. Scraping magnesium oxide from chamber
walls and hot zone shields must be done with non-ferrous
scrapers to avoid creating a spark that could ignite. If the
build-up is too heavy and difficult to scrape off, an air
burnout cycle may help crack apart large clusters. After
most of the oxide is removed from the furnace chamber
and hot zone, a normal vacuum burnout further conditions
the furnace prior to placing it back into production. Clean-
ing of diffusion pump(s) should be performed following
specific instructions from the manufacturer.
Other maintenance activities include changing vacuum
pump oils every two to six months, replacing dynamic seals
such as door seals and poppet valve seals every year, and
replacing jack panel (work thermocouple) parts every year.
Control thermocouple replacement should follow applica-
ble guidelines. Vacuum sensing gages also must be re-
placed, cleaned, or rebuilt as required.
Summary
Vacuum aluminum brazing includes several key
process parameters. Deep vacuum levels, precise temper-
ature control, and excellent temperature uniformity are all
provided by optimum furnace design and controls. Suc-
cessful part brazing relies on proper joint design with re-
gard to joint surface area and joint gaps, part cleanliness,
and correct fixturing of part assemblies. Following a rou-
tine furnace maintenance program allows repeatable, high
quality brazing results over time.
For more information:
Craig Moller is chief engineer, Ipsen
USA, 984 Ipsen Rd., Cherry Valley, IL 61016, 800.727.7625,
ipsenusa.com.
References
1.
Brazing Handbook,
AmericanWelding Society, p xvii, 1991.
2. Aerospace; Brazing and High-Temperature Brazing of Com-
ponents; Directions for Design, DIN 65169, 1986.
3.
Brazing Handbook,
American Welding Society, p 6, 1991.
4. P. McKenna, Director of Aerospace Business Development,
California Brazing, 37955 Central Ct., Newark, CA 94560,
510.790.2300,
californiabrazing.com.
Fig. 12
— Four-year-old vacuum aluminum brazing furnace.