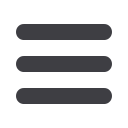
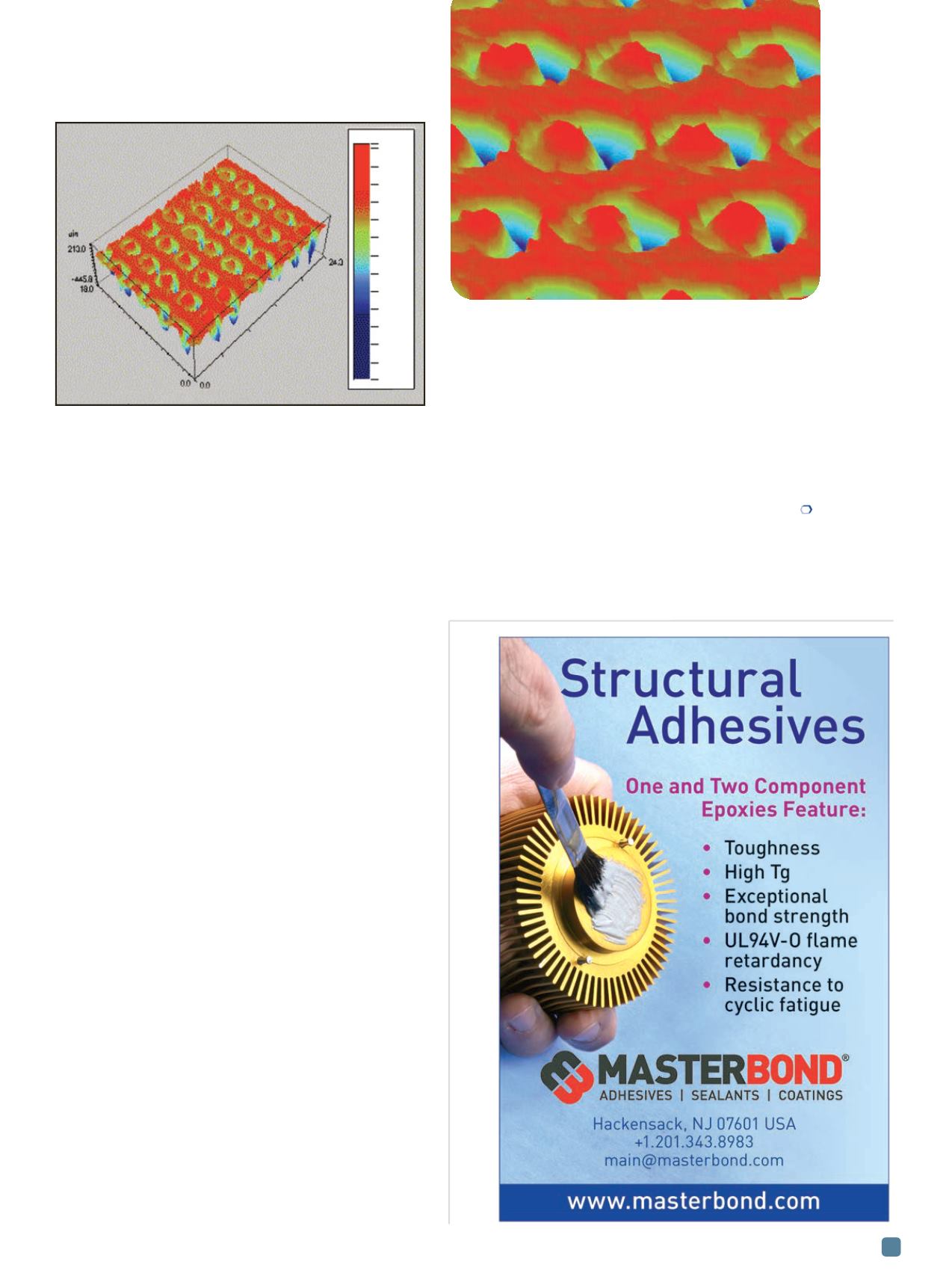
Laser finish details
State-of-the-art laser texturing, such as that developed
in Japan and now being produced as LaserMatte by Greer
Steel in North America, creates a uniform matte finish on
the work rolls by consistently imparting microcraters in the
surface of the steel. These microcraters produce a relatively
large, negative skew (Rsk) material at typical Ra levels of 25
to 50 μin. (Figs. 5 and 6), compared with the positive skew
pattern evident in the other matte finishes. 3D imaging is
used to perfect surface finishes, which provides a micro-
scopic lubrication distribution system on the metal surface
that continually feeds lubricant into the die during forming.
A 2.8-kW CO
2
laser precisely creates microcraters by
using a microscopic beam of light energy that is inter-
rupted by an aluminum chopper wheel. Highly precise
teeth chop the beam into pulses. Each segment of light
strikes the surface of the roll as it turns on a lathe, creating
localized melting on the alloy surface. A blast of assist gas
displaces the molten metal, forming a surface feature sim-
ilar to a volcanic crater. Uniformity and consistency are
achieved by repeating this process 40,000 times per sec-
ond in a helical pattern as the laser moves slowly along a
track parallel to the turning roll. Millions of small craters
are precisely placed on the roll surface, with their pitch and
size controlled by a multi-axis regulator.
Laser texturing creates a highly uniform, precise metal
surface topography that cannot be produced by conven-
tional methods. The predictable and repeatable surface
brings numerous benefits to metal formers that extend far
beyond improved lubricant-holding capabilities. Benefits
of using laser-textured materials include:
• Reduced friction and galling, resulting in improved
part quality
• Longer tool and die life
• Improved process yield
• Avoidance of costly tool and die coatings
• Increased productivity due to reduced press
downtime
• Improved metal flow in the die, as strains that cause
breakage are prevented, thus allowing the metal to
achieve its forming potential
• Lower energy costs achieved through greater process
and production efficiencies
Surface finishes affect metal formability, lubrication re-
tention, surface contact area, paint adherence, appearance,
and surface bonding area in metal forming. They also af-
fect functionality and wear rates between mating surfaces
in end-use applications. Achieving an optimummatte sur-
face is a challenge, but laser texturing technology is pro-
viding metal formers with a reliable, cost-effective process
that results in both immediate and long-term benefits.
For more information:
Todd Daenzer is chief operations and
quality officer at Greer Steel Co., 624 Boulevard St., Dover,
OH 44622, 330/343-8811,
www.greersteel.com.
ADVANCED MATERIALS & PROCESSES •
MARCH 2014
27
Fig. 5 –
Laser textured surface in 3D.
Fig. 6 –
Laser surface at high magnification in 3D.
uin
213.03
100.00
-50.00
-200.00
-445.78