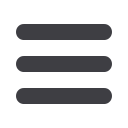
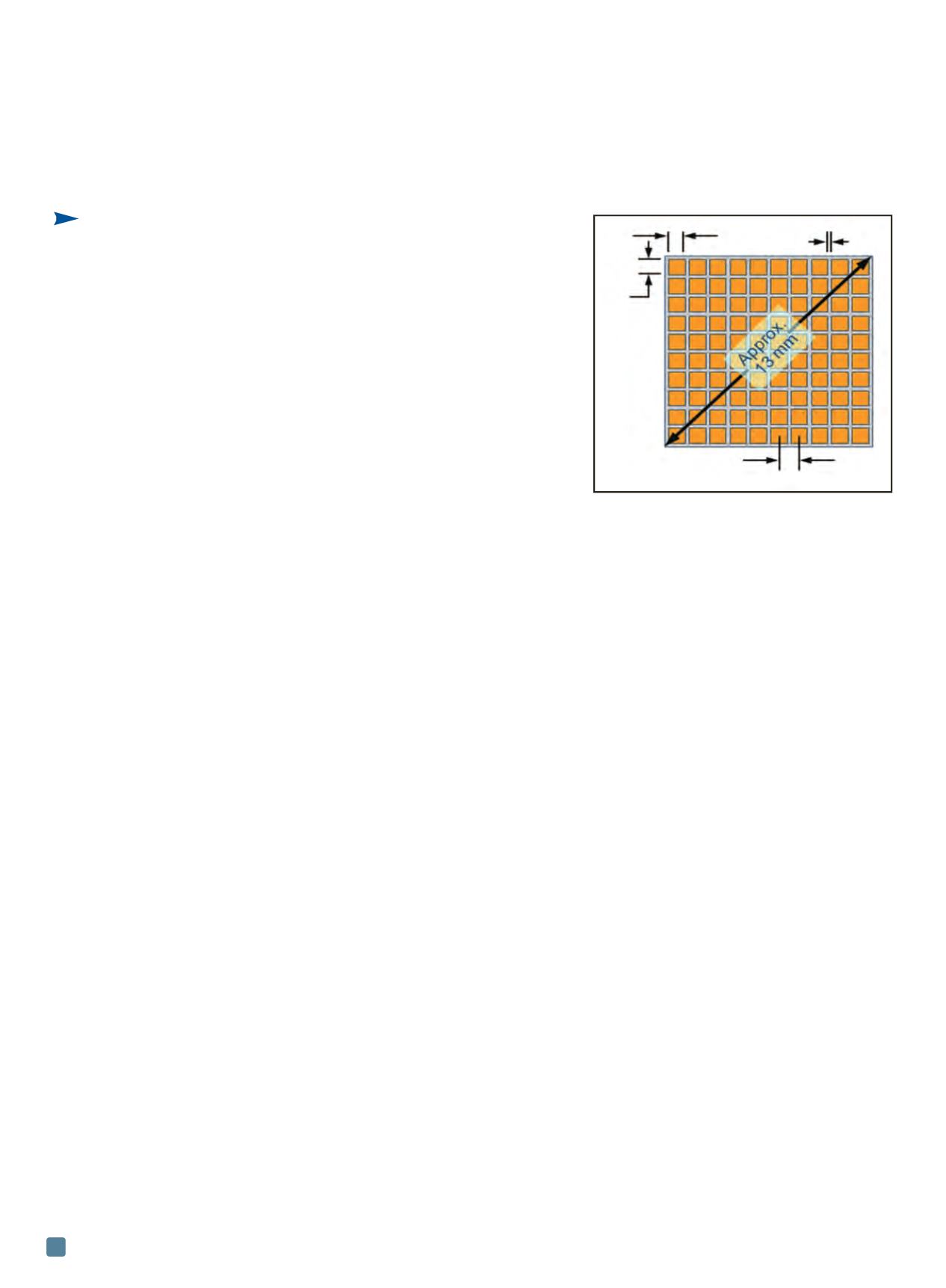
Nondestructive Inspection of Resistance Spot Welds Using
Matrix Phased Array Ultrasonic Technology
A
dvanced high-strength steels (AHSS)
were introduced to the automotive in-
dustry to reduce vehicle weight and are
gaining momentum due to initiatives that call
for increased body rigidity (driving perform-
ance) and improved crash ratings and fuel effi-
ciency. One major challenge these steels
present involves the integrity of spot welds.
There are roughly 4000-7000 resistance spot
welds on every U.S.-made automobile and the
reliability of the body structure and passenger
safety both rely on sound welds.
The stress state at the weld, fracture tough-
ness of the weldment, and presence of pores,
cracks, and embrittled regions in AHSS are driv-
ing factors resulting in different failure modes
compared to conventional steels—particularly
interfacial type failures
[1]
. Traditional resistance
spot weld (RSW) destructive test methods such
as pry-bar or chisel check and peel tests are
costly and inaccurate when applied to welds
made from AHSS. The automotive industry
therefore seeks nondestructive tests to ensure
safe implementation of AHSS steels.
Some advanced nondestructive inspection
(NDI) techniques that may provide solutions
are already used in the aerospace and power
generation industries. Unfortunately, transfer-
ring these techniques to the automotive indus-
try is limited due to fundamental differences
[2]
.
The goal is to reduce the time to validate and
increase correlation methodology confidence
with less engineering and laboratory time. To
reduce the repeatability gap, improved robust-
ness of NDI techniques and little or no depend-
ence on operator skill is needed
[2]
.
MPA probe meets the challenge
Computational modeling and simulations
helped scientists develop a reliable, high-fre-
quency matrix phased array (MPA) probe with
an appropriate delay line and an optimal prop-
agation distance for the ultrasonic beam to be
focused on a spot weld. A commercially avail-
able CIVA modeling package was used to per-
form this modeling and simulation.
It was necessary to define parameters such
as material thickness and spot weld diameter.
Research revealed that the majority of spot
weld applications are for materials in the thick-
ness range of 0.7-2 mm having a nominal weld
diameter of 5-7 mm. Initial beammodeling cal-
culations helped determine general parameters
for a probe capable of inspecting spot welds in
the targeted range. Consideration was given to
current MPA instrumentation capabilities, al-
though many MPA instruments on the market
today limit the number of elements to a maxi-
mum of 128. Figure 1 shows a schematic of a
100-element 2DMPA probe element with some
probe parameters evaluated using the beam
modeling tools. The same probe parameters
apply to 3D probes with additions of curvature
shape and radius.
To achieve good focus at a depth of 0.7-2
mm, the probe needs to have a physical delay
distance between the element and part surface.
The delay line tip was filled with water because
it conforms to surface deformations caused by
the welding electrodes. Modeling and simulation
results show that a water path length of 18 mm
produces a narrow beam with minimum side
lobes through the interface of water and metal.
A handheld probe was designed and fabri-
cated with an 18-mm-long water delay line cav-
ity at the end. Subsequent modeling
investigation for a 64-element probe with an
8×8 matrix configuration operating at a 12
MHz frequency proves the same water delay
line could be used. In this case, the probe ele-
ment was shaped to have a convex curvature
with a 50-mm radius.
From simulation to reality: Portable NDI
The EWI SpotSight inspection system
shown in Fig. 2 harnesses the power of MPA-
based ultrasonic imaging technology to accu-
rately evaluate the effectiveness of component
joints by showing weld nugget images in real-
Jeong K. Na
EWI
Columbus, Ohio
ADVANCED MATERIALS & PROCESSES •
MARCH 2014
22
Automobile
performance
and passenger
safety both
rely on sound
welds. A new,
high-frequency
ultrasonic MPA
probe performs
nondestructive
inspection of
these welds,
saving time
and cost.
0.8 mm
0.1 mm
0.8
mm
0.9 mm pitch
Fig. 1 —
Schematic of a 2D matrix phased array
(MPA) probe element.