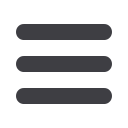
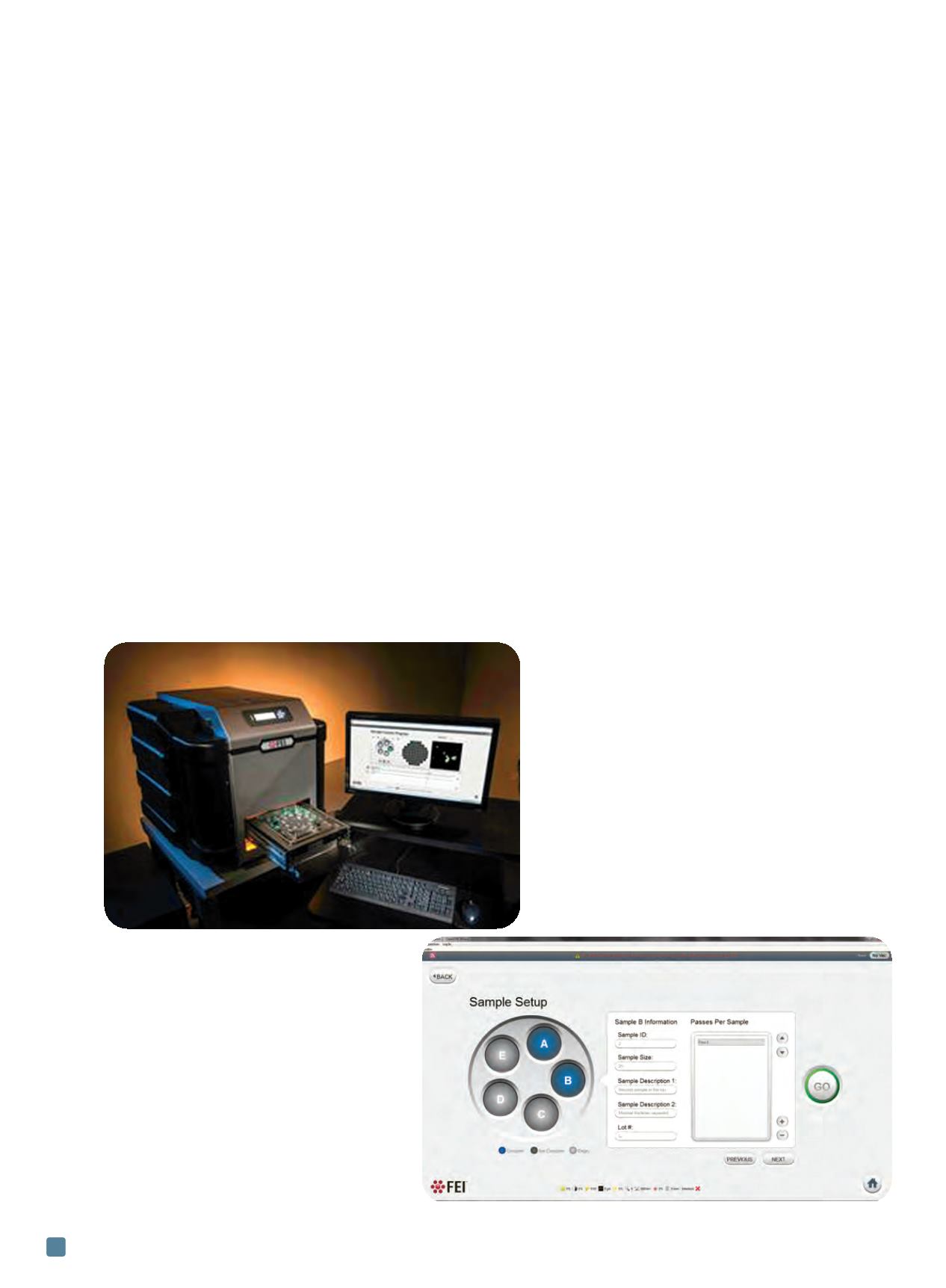
Faster, Automatic Identification of
Particle Contamination
I
ndustries such as automotive, electronics, and med-
ical devices are particularly sensitive to the perform-
ance of precision-manufactured parts. When parts
fail, sometimes due to particulate contamination that
occurs in the manufacturing process, incomplete coat-
ings or engine damage can occur.
The ability to identify particle contaminants and
their origins can be an advantage in manufacturing op-
erations. In automobile production, for example, con-
taminants range from metal shavings to abrasive
residues to small fibers. As engine tolerances tighten,
particles that impact performance have gotten smaller.
Residue can remain throughout the manufacturing
process, causing issues when engines are finally tested.
Traditional methods of monitoring surface clean-
liness such as gravimetric analysis can calculate con-
taminant total bulk weight, but do not produce
individual particle data. As a result, components may
pass gravimetric testing, yet fail to function due to in-
dividual “killer” particles that can cause issues. Some
manufacturers see dangerous abrasive contaminants,
such as aluminum oxide, that are just 2 μm, which are
not detected via traditional gravimetric testing yet
cause engines failure.
Traditional methods
Many options for monitoring particles on automo-
tive component surfaces are available. It is important
to thoroughly understand the features and benefits of
each approach.
Bulk/gravimetric testing —
Bulk/gravimetric meas-
urements have long been used to quantify foreign ma-
terial presence by measuring filter weight before and
after part flushing. The part or assembly is typically
flushed and residue is collected on a pre-weighed fil-
ter. The loaded filter is dried and weighed, indicating
the total mass of collected debris. This method only
provides a gross or an undifferentiated measure of the
amount of material present. The weight or volume of
filtered materials sheds no light on particle size, shape,
or composition, which is necessary to improve design
or control processes.
Particle counters —
Particle flow-counters disperse
particles in fluid. Particles are then passed through a
flow cell where they are detected by an optical or laser
sensor. Such devices can accurately count thousands of
particles per second, and often provide a graph of par-
ticle size distributions. However, most counters assume
particles are perfectly round. As a result, particle
counter manufacturers report out an equivalent diam-
eter using various algorithms, making comparisons be-
tween particle size reports from different
manufacturers difficult and/or inconclusive. Particle
counters also may experience false positives, which
typically result from air entrapment or water in the oil.
While these units are useful for monitoring trends of
established particle populations, they are less valuable
for understanding unknown or changing particle pop-
ulations (clear signs of changes in surface contamina-
tion on a part or component).
ADVANCED MATERIALS & PROCESSES •
MARCH 2014
28
TECHNICAL SPOTLIGHT
CleanCHK system
with automated sample setup.
Screenshot of sample setup
screen on CleanCHK.