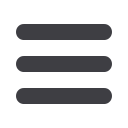
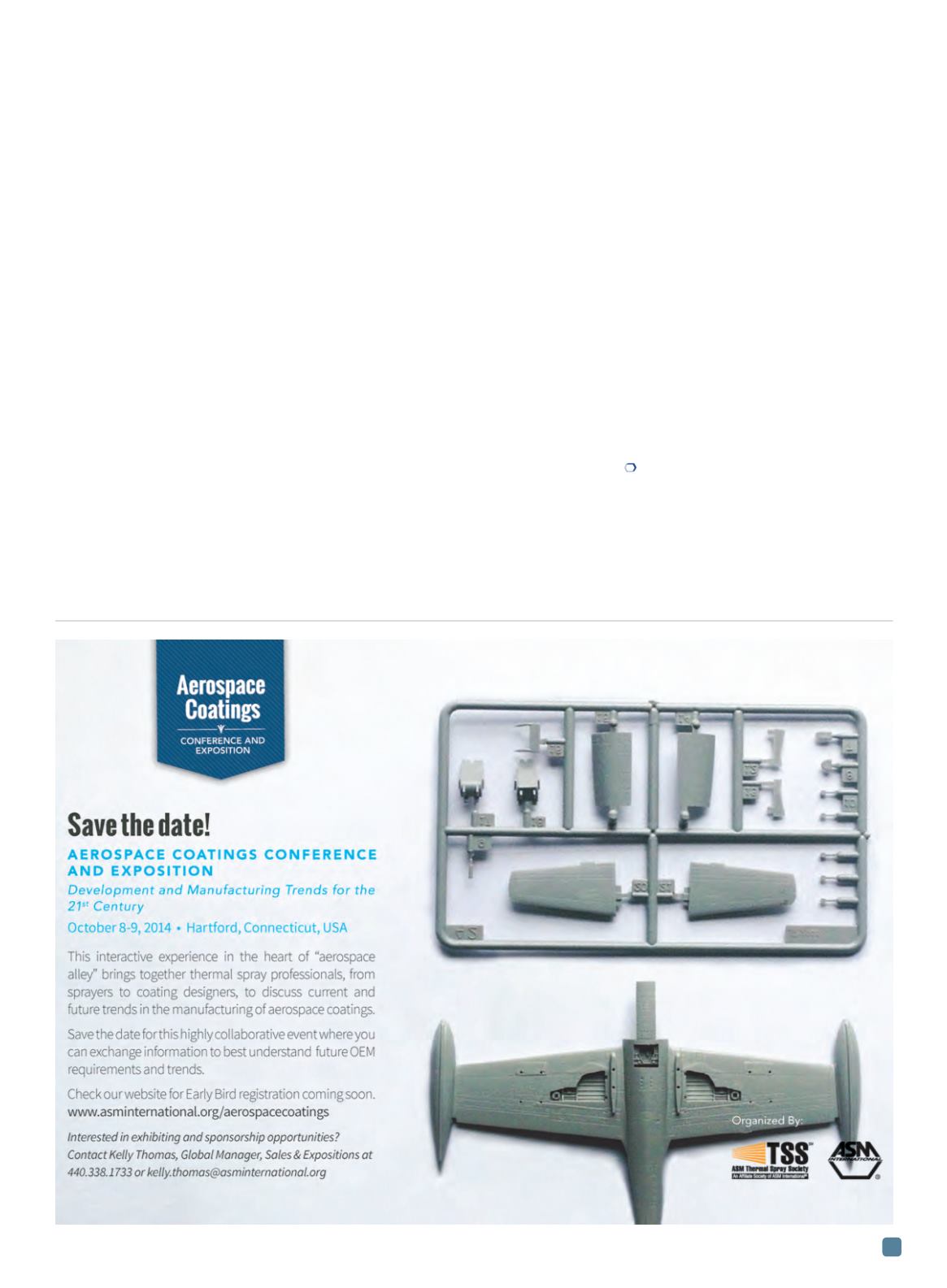
ADVANCED MATERIALS & PROCESSES •
MARCH 2014
31
Case study
As the automotive industry has become increasingly
sensitive to part cleanliness, implementing integrated,
automated, and rapid monitoring at the production
level in plants helps improve part quality. One client
maintains that its field failure rate (failure within the
first 10,000 miles) decreased by 70% while using the
CleanCHK Analyzer.
Engineers at the plant developed a study focused on
understanding the levels and sources of contamination
present in their manufacturing process. Within a fuel
injection system, the tight tolerances between moving
parts and the small dimensions of a new fuel injection
nozzle led engineers to conclude that quantity, size, and
shape were all critical factors in understanding their
processes. A steel shaving was found to be considerably
more detrimental to components than a dust particle
of similar dimensions. Elemental composition of the
particulate was determined to be a key factor in devel-
oping new cleanliness standards.
A cleanliness monitoring process was put in place
using the CleanCHK analyzer. The system provides the
means to measure performance against cleanliness
standards. The process began by collecting samples
using a 47-mm-diameter membrane filter with pore
sizes between 0.3-20 μm. To ensure a representative
sample was collected, cleaning fluid from each part was
passed through the filter using vacuum filtration. Fil-
ters were then placed directly in the system using a
5-filter sample holder.
The CleanCHK reporter allowed easy management
of produced data. Reporting was based on preset inter-
nal standards and presented in predetermined tem-
plates, which ensures reproducibility from user to user
as well as filter to filter. Component specifications in
this manufacturing plant are expressed today in the fol-
lowing format: Particles present should (1) have a value
less then X mg/surface area, (2) no particle larger than
X may be present, and (3) no more than X particles may
be present with sizes between X µm and X µm. Compo-
sitional analysis for each particle was monitored based
on size and shape in relation to a particular chemistry.
Compositional information allowed for pinpointing is-
sues even faster. This helps the manufacturer reduce
field failure rates by 75%.
For more information:
Susan Benes is Product Marketing
Manager for FEI Co., 5350 NE Dawson Creek Dr., Hillsboro,
OR 97124, 503/726-7500,
susan.benes@fei.com,
www.fei.com.