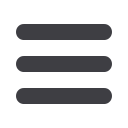
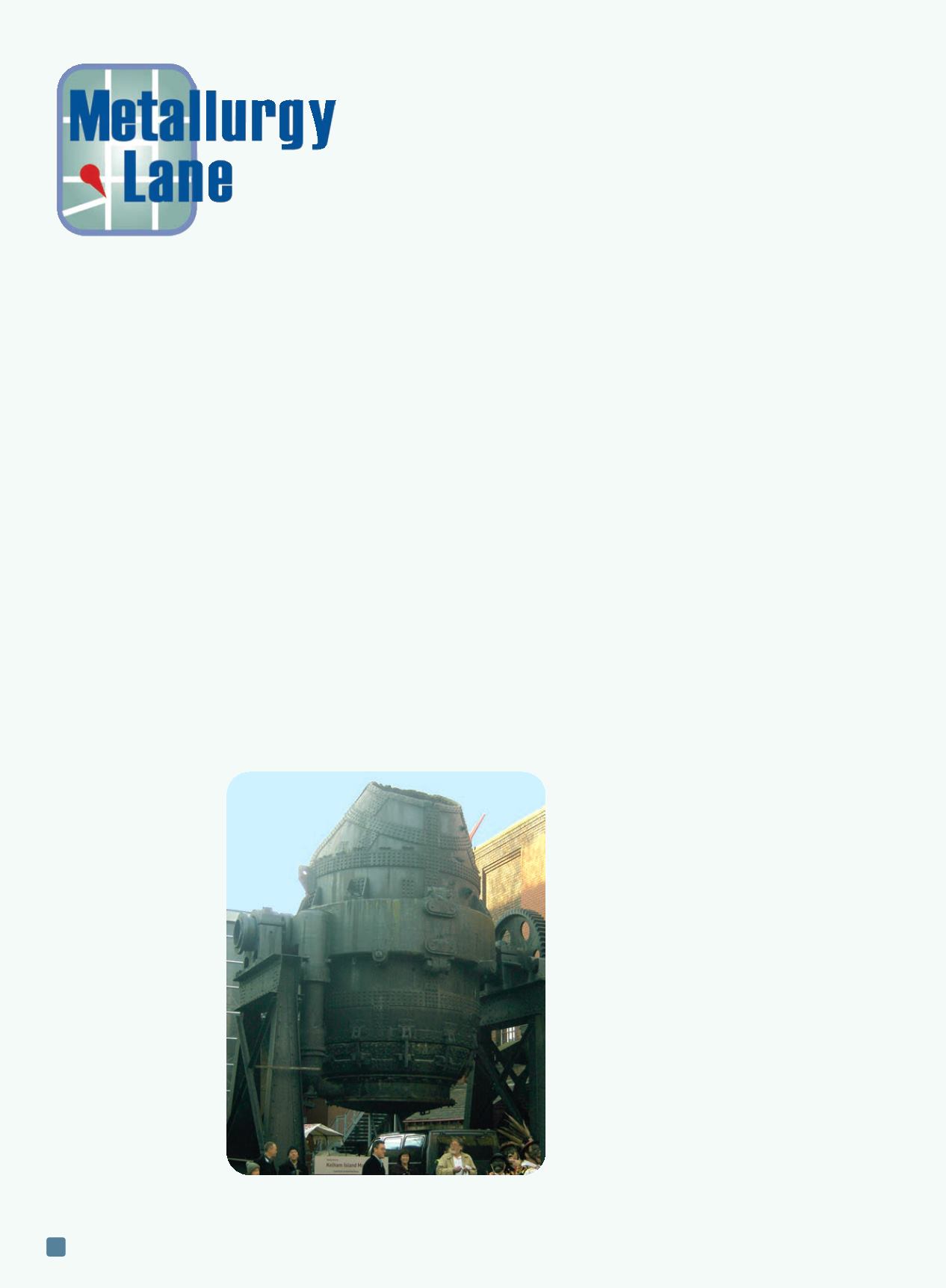
ADVANCED MATERIALS & PROCESSES •
MARCH 2014
32
I
n the latter half of the 19th century, the indus-
trial world of wrought iron experienced a revolu-
tion: A process for making steel directly from
blast furnace cast iron was being developed at two
different locations. One was at a small iron mill in
Kentucky owned by two brothers—William and
John Kelly. As usual, the men soon encountered a
fuel shortage after clearing all the timber near the
plant for charcoal. With this in mind, William Kelly
noticed that the cold air was not chilling the metal,
but was reacting with it chemically to generate heat
where the air blast impinged on the molten metal
in the finery. Kelly immediately recognized the
value of this reaction as a means of converting pig
iron to wrought iron. Although this revelation oc-
curred in 1847, he was delayed in building a con-
verter until 1851.
The second location was in England where an
engineer and inventor named Henry Bessemer—
who had invented the artillery shell—was work-
ing on a way to replace the cast iron in cannons
with steel. Bessemer’s finances were much bet-
ter than Kelly’s, allowing him to pursue his ideas
immediately.
Kelly moved his experimental operations to the
Cambria Iron Company in Johnstown, Pa., the
company where Daniel Morrell and John Fritz were
laboring to develop their three-high mill to roll
wrought iron into rails. Kelly received his patent in
1857, just as a U.S. financial panic was taking hold,
and went bankrupt along with thousands of other
businessmen. He sold the controlling interest in his
patent in 1861, and two years later a company was
formed to produce steel by his process. This en-
tity—the Kelly Pneumatic Process Company—was
located in a pilot plant in Wyandotte, Mich., out-
side of Detroit. At this point, the operation devel-
oped the same quality problem that plagued
Bessemer in England.
During Bessemer’s experimental work, he had
fortuitously used Swedish ore, which was low in
impurities. Later, when his licensees were unable
to control the carbon content and make steel that
was not brittle, respected steelmaker Robert
Mushet showed that manganese was a necessary
ingredient to overcome the “hot shortness” caused
by sulfur. He also determined that carbon content
could only be controlled by blowing until it was
completely removed, and then adding back the re-
quired amount. By this time, German iron and
steelmakers had already developed a master alloy
called “spiegeleisen” for adding carbon and man-
ganese. Thus, Mushet was a major contributor to
the success of the so called Bessemer process.
However, the patent situation was now in gridlock
with Bessemer and Kelly each holding a vital posi-
tion in the process.
Bessemer process makes headway
During this period, America was in the throes
of the terrible war between the industrial north and
the agricultural, slaveholding south. Government
agents as well as private individuals from both
areas were combing Europe looking for armaments
and other developments that would aid their cause.
One such individual was a charismatic engineer
and technical writer by the name of Alexander
Lyman Holley.
Holley was born in Connecticut in 1832. He
graduated from Brown University in 1853 in the
first engineering class and started working on rail-
road locomotives. On a trip to Europe to observe
Metallurgy Lane,
authored by
ASM life member
Charles R. Simcoe
,
is a yearlong series
dedicated to the early
history of the U.S. metals
and materials industries
along with key
milestones and
developments.
Bessemer converter at Kelham Island Museum,
Sheffield, England. Courtesy of Gunnar Larsson.
The Age of Steel: Part I
The second half of the 19th century set the stage for major U.S. industrial growth,
and the Bessemer steelmaking process played a significant role.