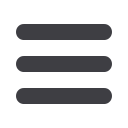
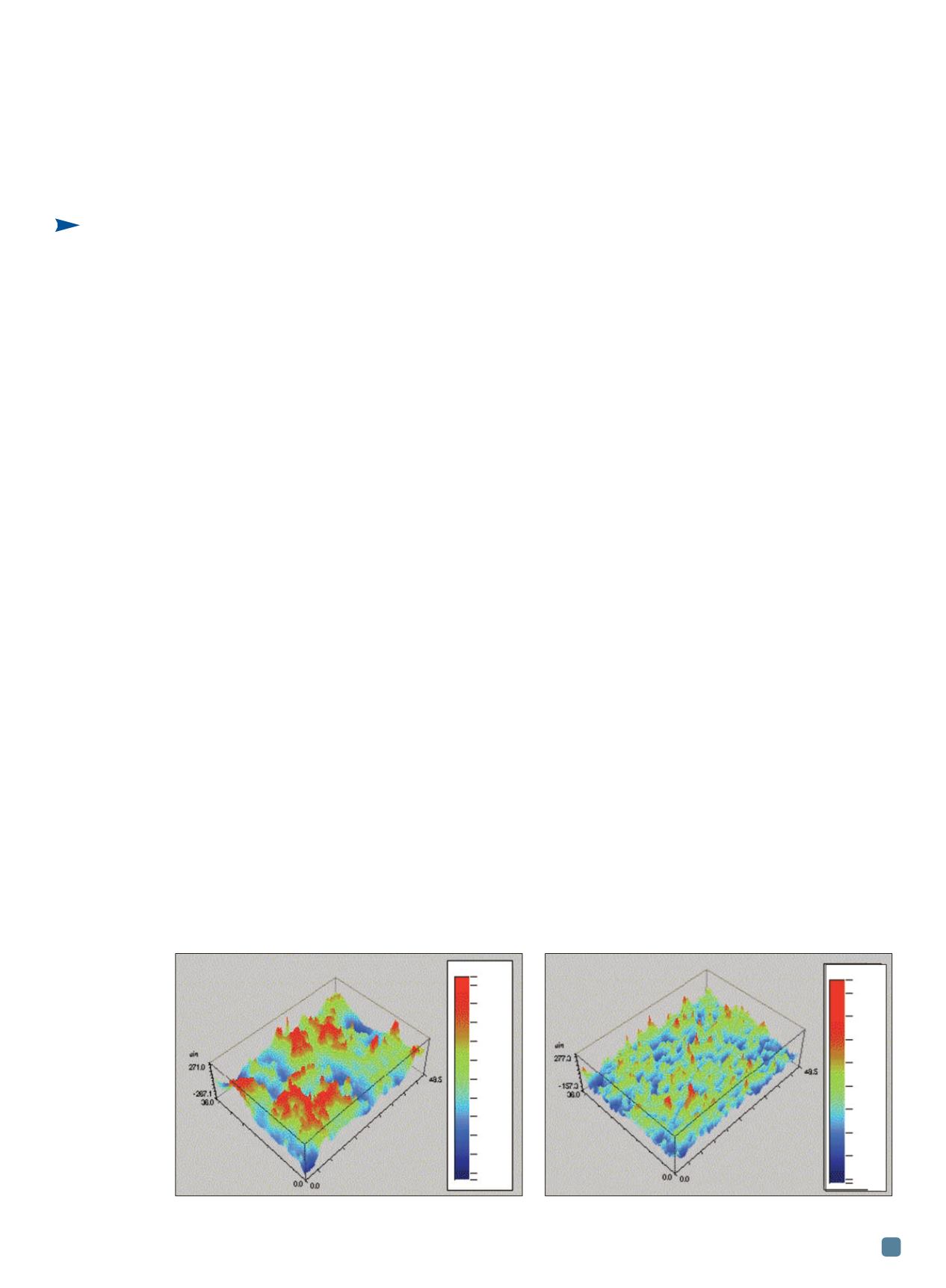
Laser Beam Texturing
for Automotive Metal Forming Applications
I
n the majority of metal drawing and forming
operations, a surface texture is applied to the
metal to aid forming. This surface texturing,
which is typically imparted as a matte finish,
primarily improves the metal’s drawability by
creating depressions in the surface and increas-
ing the lubrication carrying capacity. Addition-
ally, these types of textured finishes can
promote paint adhesion or enhance the appear-
ance of components.
In North America, most textured or matte
finishes are developed through either me-
chanical means (shot-blasting, grit-blasting,
grinding) or electro-discharge texturing
(EDT) of mill rolls that then impart the devel-
oped finish onto the metal surface during the
final rolling operation. Asia and Europe addi-
tionally use laser beam texturing (LBT) or
electron beam texturing (EBT) systems to in-
duce a matte finish on mill rolls. The finish
that these systems provide offers advantages
over more traditional methods. LBT materials
and how they differ from those produced
using traditional surface texturing techniques
will be discussed in this article.
Importance of matte/surface finishes
Lubrication is a critical factor in forming
and drawing flat rolled steels. Oil (the typical
lubricant) is applied to the surface to reduce
friction during forming and drawing. The sur-
face topography of steel impacts the lubri-
cant’s effectiveness during forming. The
matte or textured surface finish should be
consistent in surface characteristics across the
width as well as along the length to be effec-
tive. It should allow for even and consistent
contact pressure over the entire part, enhanc-
ing metal flow during forming and preventing
localized strains that could lead to failure.
Maintaining consistent lubrication greatly
reduces potential problems during forming and
drawing. Issues include:
• Die damage: Excessive die wear and/or
galling occurs due to localized strains,
increasing die maintenance costs.
• Product loss: Galling and damage to parts
can reduce yields and increase inspection
costs.
• Production delays: Extra time is needed to
service prematurely worn dies and to
make up for scrapped parts.
Advantages of
laser-beam-textured finishes
In order to adequately compare surface
characteristics of various types of finishes, it is
necessary to look beyond traditional profilome-
ter traces. While this information indicates sur-
face roughness and other parameters, each test
is a single trace across the surface. 3D imaging,
available through light interference technology,
allows for more refined analysis over a much
larger surface area, providing a more accurate
picture of the material’s topography. This tech-
nology plays a key role in quantifying the no-
table differences in the various types of matte
finishes detailed in this article.
One common method, shot/grit-blasting,
propels abrasive media at the roll surface at
high speeds, which upsets the surface and pro-
duces a roughened texture or matte finish. This
method produces a somewhat nonuniform and
variable finish. Figure 1 shows the 3D surface
of steel produced from blasted finish mill rolls
as compared to the steel surface in Fig. 2, pro-
duced by EDT-processed mill rolls. EDT in-
volves applying a pulsed electric field between
Todd Daenzer
Greer Steel Co.
Dover, Ohio
ADVANCED MATERIALS & PROCESSES •
MARCH 2014
25
An alternative
to traditional
surface
texturing
processes is
laser beam
texturing,
which offers
various
advantages
over other
commonly
used methods.
Fig. 1 –
Blasted surface finish in 3D.
Fig. 2 –
Electro-discharge textured surface in 3D.
uin
270.97
150.00
50.00
-50.00
-150.00
-267.11
uin
277.36
200.00
100.00
0.00
-157.31