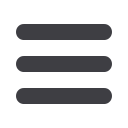
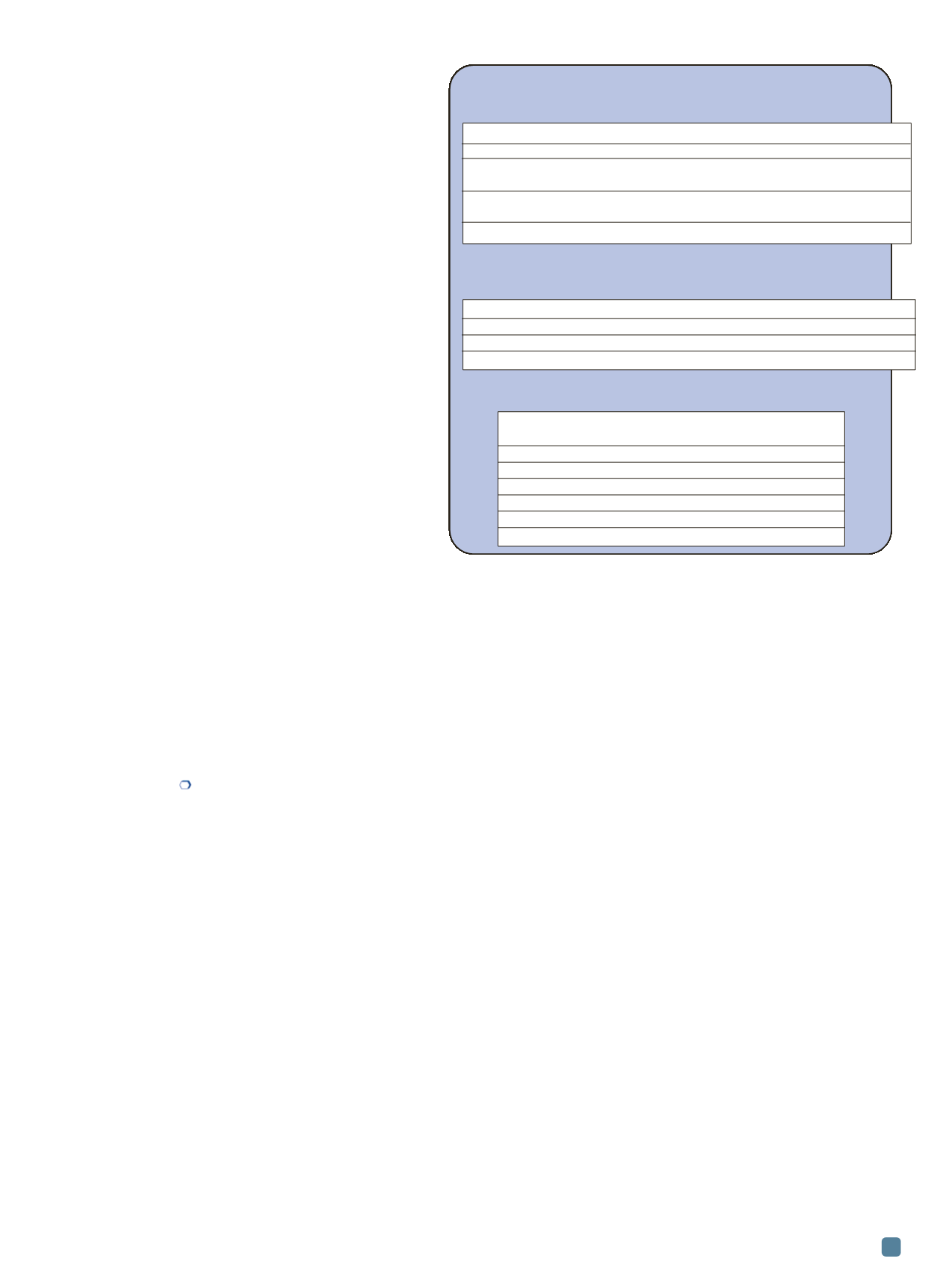
of inclusions can reduce both the corrosion resistance and
melt fluidity of castings because they promote galvanic
coupling with the matrix—leading to pitting corrosion—
and increase melt viscosity, making castings more difficult
to form. The presence of nonmetallic inclusions also pre-
maturely degrades cutting tools, resulting in reduced
machinability of Mg alloys. Results show that in all cases,
removing inclusions improves the properties of Mg alloys.
Summary and perspectives
Compared to Al alloys, limited information is available
regarding Mg alloy refining. Inclusions present in molten
Mg can be categorized into two major groups: Nonmetal-
lic (mainly oxides and chlorides) and intermetallic (iron-
rich phases). The majority of inclusion-related issues with
Mg alloys appear to originate frommolten Mg exposure to
moisture or oxygen, which can occur during melting, melt
transfer prior to pouring, and mold filling. A better under-
standing of the behavior of the magnesium oxide surface is
required to improve Mg melt cleanliness.
Various techniques have been developed, ranging from
simple methods such as metallographic analysis to highly
advanced approaches such as LiMCA. Each has advantages
and disadvantages, and considerations such as cost and
type of inclusion detection limits must be recognized.
None of the techniques developed to assess Mg alloy melt
cleanliness is universally accepted, so there is still a need
for an efficient and economical assessment method. A
combination of approaches may be the best solution.
Several methods to control inclusions in Mg alloys such
as fluxes, protective atmospheres, filtration, inert gas bub-
bling, and degassing are available. Filtration and inert gas
bubbling can be used in combination with relative ease and
at low cost to further improve inclusion removal efficiency
in Mg alloys. Properties significantly improve when inclu-
sions are removed.
A
cknowledgements
The authors are indebted to Prof. Alexander McLean for
his review and valuable comments. They also thank the
members of the Centre for Near-net-shape Processing of
Materials and sincerely acknowledge the Natural Sciences
and Engineering Research Council of Canada for financial
support.
For more information:
C. (Ravi) Ravindran is Professor of
Advanced Materials, Dept. of Mechanical and Industrial En-
gineering, Ryerson University, 350 Victoria St., Toronto, ON
M5B 2K3, Canada, 416/979-5000 ext. 6423,
rravindr@ryer- son.ca,
www.ryerson.ca.
References
1. M.M. Avedesian and H. Baker, Magnesium and Magne-
sium Alloys, ASM International, Materials Park, OH, 1999.
2. W. Wang, et al.,
J. Alloy Compd.,
480(2), p 386-391, 2009.
3. S. Lun Sin, A. Elsayed, and C. Ravindran,
Int. Mater. Rev.,
58(7), p 419-436, 2013. Link to the full article at
www.maneyonline.com/doi/full/10.1179/1743280413Y.000 0000017.4. A. Ditze and C. Scharf, Recycling of Magnesium,
Clausthal-Zellerfeld, Papierflieger Verlag, 2008.
5. D. Oymo, et al., Light Metals 1994 Conference, San Fran-
cisco, TMS, p 1017-1024, Feb. 27-March 3,1994.
6. C.J. Simensen and B. Oberlander,
Praktische Metallogra-
phie/Practical Metallography
, 17(3), p 125-136, 1980.
7. P. Bakke and D.O. Karlsen, 1997 SAE Intl. Congress and
Exposition, Detroit, SAE International, p 61-73, Feb. 24-27,
1997.
8. H. Hu and A. Luo,
JOM
, 48(10), p 47-51, 1996.
9. W.D. Griffiths and N.W. Lai,
Metall. Mater. Trans. A,
38A,
p 190-196, 2007.
10. B. Bronfin, et al., Magnesium Technology 2002, Seattle,
TMS, p 55-60, Feb. 17-21, 2002.
11. A.G. Haerle, B.A. Mikucki, and W.E. Mercer II,
Light
Met. Age
, 54, p 22-29, 1996.
12. J.M. Tartaglia, et al.,
JOM
, 53(11), p 16-19, 2001.
13. H. Westengen and T.K. Aune, Magnesium Casting Al-
loys-Casting Alloys, in
Magnesium Technology: Metallurgy,
Design Data, Automotive Applications,
eds. H. Friedrich, et
al., Berlin, Heidelberg, Springer-Verlag, 2006.
14. S. Poynton, M. Brandt, and J. Grandfield, Light Metals
2009 Conference - TMS 2009 Annual Meeting and Exhibi-
tion, San Francisco, TMS, p 681-687, 2009.
15. S.P. Cashion, N.J. Ricketts, and P.C. Hayes,
J. of Light
Metals
, 2(1), p 43-47, 2002.
16. S. Tardif, R. Tremblay, and D. Dubé, 40th Annual Con-
ference of Metallurgists of CIM, Toronto, Canadian Insti-
tute of Mining, Metallurgy and Petroleum (CIM), p 225-235,
Aug. 26-29, 2001.
17. D.O. Karlsen, et al., 32nd Annual Conference of Metal-
lurgists of CIM, Québec City, p 397-408, Aug. 29-Sept. 1,
1993.
18. M. Maiss and C.A.M. Brenninkmeijer,
Environ. Sci.
Technol.,
32, p 3077-3086, 1998.
19. C.D. Yim, G. Wu, and B.S. You,
Mater. Lett.
, 48(10), p
2778-2781, 2007.
20. A. Elsayed and C. Ravindran,
J. Mater. Eng. Perform.
, in
press, p 1-9, 2013.
ADVANCED MATERIALS & PROCESSES •
MARCH 2014
19
Fig. 4 —
Effect of inclusions on the properties of Mg alloys
[2, 10, 20]
.
Tensile strength and elongation
Both average tensile strength and average elongation of AZ91D
increased with filtration, Ar bubbling or Ar+filtration.
Corrosion resitance
Increasing inclusion content increased the corrosion rate of
Mg-10Gd-3Y-0.5Zr alloy.
Fluidity
The fluidity of AZ91 decreased with increasing MgO content.
Refining treatment
UTS (MPa) Elongation (%)
No treatment
153
2.3
Filtration
167
3.1
(steel filter, 0.81 mm square, 0.38 mm thick)
Ar bubbling
188
3.3
(flowrate: 1.7 L/min; bubbling time: 5 min)
Ar bubbling + filtration
198
4.9
MgO content
Average fluidity
AZ91 alloy
(ppm)
length (mm)
1
35 ± 6
225
2
42 ± 12
220
3
75 ± 19
203
4
93 ± 24
192
5
125 ± 64
185
6
472 ± 345
172
Average volume fraction of inclusions (%)
Corrosion rate (mg/cm
2
d)
4.07
2.0
2.84
1.8
0.87
1.3