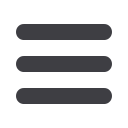
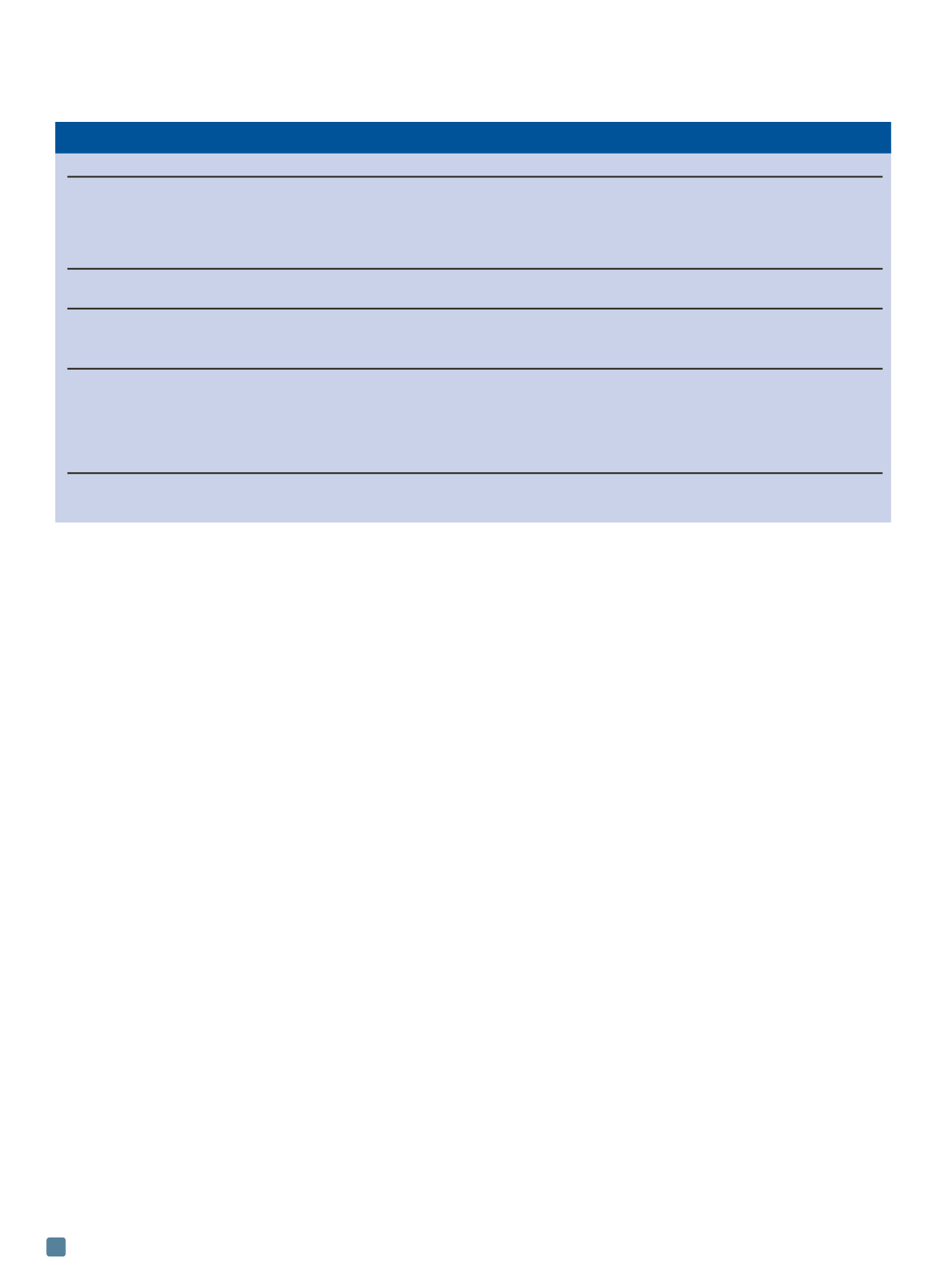
Inclusion removal
In addition to assessing the amount of inclusions in Mg
alloys, it is necessary to adapt suitable procedures and
techniques to remove them. Table 2 summarizes some sim-
ple techniques to remove inclusions from Mg alloys.
Historically, Mg melts were protected during melting
and casting using fluxes such as MgCl
2
, KCl, and CaF
2
[1]
.
While adequate at protecting Mg melts from oxidation,
fluxes can be entrapped in the melt during transfer and
casting and become inclusions. Since the 1970s, the Mg in-
dustry has largely used sulfur hexafluoride (SF
6
) to protect
Mg melts
[15]
. SF
6
modifies the magnesium oxide film that
forms naturally on the surface of the melt, thereby sup-
pressing vaporization. This compound is also attractive as
a cover gas because it is odorless, colorless, nontoxic, non-
flammable, and noncorrosive. However, SF
6
is becoming
increasingly expensive and is also an extremely powerful
greenhouse gas, with a 100-year global warming potential
(GWP), estimated at 23,900 times that of CO
2
[18]
. Nonreac-
tive gases, such as nitrogen and argon, prevent burning.
However, use of such gases is impractical outside of the
laboratory because they do not suppress Mg vaporization,
which can result in melt loss.
Even with adequate protection, high melt turbulence
increases the probability of entraining gases or oxide films
during mold filling, introducing more inclusions into the
casting. Incorporating filters into the casting process helps
reduce melt turbulence by regulating metal flow. Filters for
Mg alloys have typically been composed of ceramic (Al
2
O
3
,
SiO
2
, ZrO
2
, MgO, or a combination of these oxides) in a
foam-like structure with several open cells or as a steel
mesh. However, ceramic filters have controversial effi-
ciency because they may also react with the Mg melt.
Tardif, et al.
[16]
examined the use of knitted steel mesh fil-
ters to remove melt inclusions in permanent molds. Two-
and four-ply filter configurations entrap mostly MgO and
some Al-Mn-Fe intermetallic particles. Griffiths and Lai
[9]
observed that ceramic filters in combination with a well
designed gating system could reduce double oxide film de-
fects. Filtration is a simple and effective method for remov-
ing inclusions in Mg melts, but more research is needed to
optimize performance and understand the best methods
to incorporate filters with the gating system.
Filtration can be combined with inert gas bubbling to
further improve inclusion removal. Inert gas bubbling uses
Ar or CO
2
to float melt inclusions to the melt surface
where they can be skimmed away. The efficiency of gas
bubbling to remove inclusions depends on bubbling time,
gas flow rate, bubble size, and melt temperature
[19]
. Typical
usage of Ar gas bubbling for 6 kg of AZ91D involves a flow
rate of 1.8 l/min at a melt temperature of 740°C for a bub-
bling time of 30 minutes
[19]
. The limited availability of
quantitative results on gas bubbling efficiency has sparked
the need to determine optimal processing variables (e.g.,
Ar flow rate, residence time, bubble diameter, melt tem-
perature) to enable efficient melt refining. A steel mesh fil-
ter with Ar bubbling treatment was as effective as
degassing to improve mechanical properties and did not
release harmful hydrocarbons when added to the melt
[20]
.
Melt degassing typically uses reactive chlorine (Cl
2
)
gas or hexachloroethane (C
2
Cl
6
) to reduce hydrogen gas
content within melts. Both methods promote formation
of MgCl
2
, which can remove inclusions but may become
an inclusion itself if it becomes entrapped in the melt.
Adding C
2
Cl
6
could reduce grain size in castings, but
causes environmental problems due to chlorinated hy-
drocarbon emissions
[17]
.
Effects of inclusions on Mg casting properties
The influence of inclusions on mechanical properties
(strength and elongation), machinability, corrosion resist-
ance, and fluidity is demonstrated in Fig. 4. The presence
ADVANCED MATERIALS & PROCESSES •
MARCH 2014
18
TABLE 2 — SUMMARY OF METHODS TO REMOVE INCLUSIONS IN Mg ALLOYS
Process
Description
Advantages
Disadvantages
Flux refining
MgCl
2
, KCl, NaCl and
Simple and cost effective
Flux may become entrapped
CaF
2
based
[1]
in melt
Flux absorbs oxides to produce
Flux compositions must be
a sludge that settles to the
tailored to alloy being melted
bottom of the crucible
Protective
SF
6
forms a dense film of
Very effective even at
Potent greenhouse gas
atmosphere (SF
6
)
MgO and MgF
2
[15]
0.1-0.2 vol.%
Filtration
Ceramic foam and steel
Can entrap MgO bifilms
[9]
,
Must be incorporated into
mesh types
particles and some Al-Mn-Fe
mold/casting design
Placed in mold cavity
intermetallics
[16]
Inert gas
Ar or CO
2
gas is used to float
Can be combined with
Large inclusions cannot
bubbling
inclusions to the melt surface
filtration
be removed
for skimming
Low purity gases or moisture
Can introduce porosity
Efficiency depends on bubbling can introduce more inclusions
Optimization of parameters
time, gas flowrate, bubble
size and melt temperature
required
Degassing
Cl
2
gas or C
2
Cl
6
Very effective
Releases toxic chlorinated
Formation of MgCl
2
(flux)
hydrocarbons
[17]