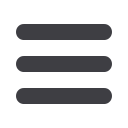
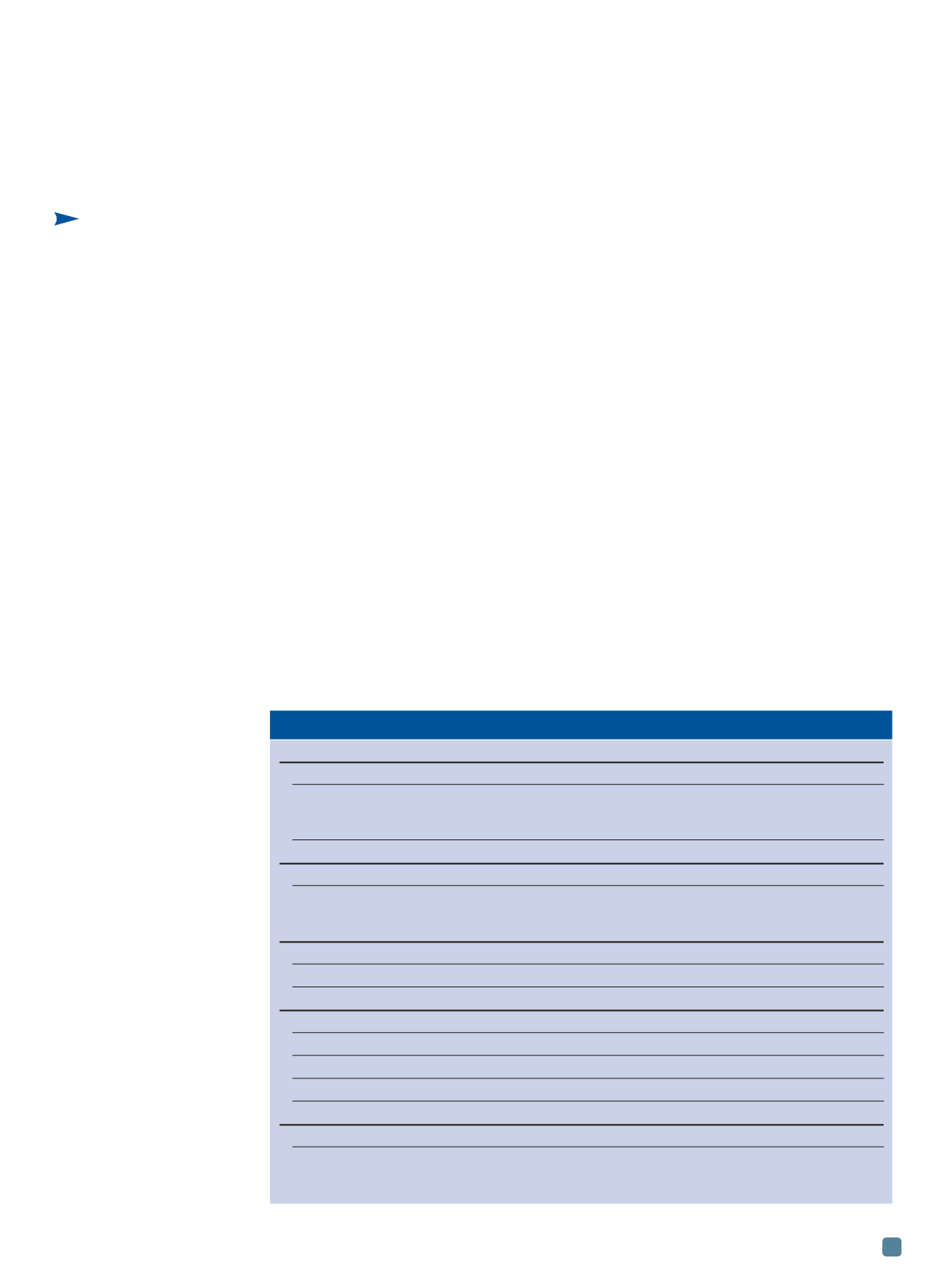
ADVANCED MATERIALS & PROCESSES •
MARCH 2014
15
Finding and Removing Inclusions in
Magnesium Alloys
M
agnesium and its alloys are among
the most promising lightweight ma-
terials. With a density of 1.74 g/cm
3[1]
(35% lighter than aluminum), Mg alloys are at-
tractive to both the aerospace and automotive
industries due to their high strength-to-weight
ratio, good castability, high impact resistance,
and high recyclability.
However, its high oxidation potential usu-
ally results in inclusion contents much greater
than that found in Al. Unlike Al alloys, which
form a stable nonporous oxide surface, molten
Mg produces a porous magnesium oxide
(MgO) surface that does not protect the molten
metal from further oxidation unless special pre-
cautions are taken. Inclusions in Mg alloys re-
duce strength and ductility, are detrimental to
surface finish, increase porosity, and exhibit a
tendency to increase corrosion
[2]
. Improving
the melt quality by controlling trace elements,
reducing the amount of dissolved gases, and re-
moving inclusions could enhance the proper-
ties of Mg and its alloys.
This article provides an overview of typical
inclusions found in Mg and its alloys, various
techniques used to determine inclusion con-
tent, and methods employed to reduce inclu-
sions and their influence on properties. This
discussion is based on a recent review article
on inclusions in Mg alloys
[3]
.
Inclusions in Mg alloys
Typical inclusions found in Mg alloys can
be categorized into either nonmetallic (oxides,
carbides, nitrides, chlorides, and salts) or inter-
metallic (iron-based) types. A summary of typ-
ical inclusions is shown in Table 1.
Each stage of the casting process is a poten-
tial source of inclusions in Mg alloys. Melting,
melt holding/transfer, and casting each exhibit
conditions in which the molten Mg surface may
be exposed to the atmosphere where inclusions
could form:
Melting —
Molten Mg reacts with oxygen to
formMgOwhen the melt is exposed to oxygen in
the atmosphere
[7, 8]
. In addition, all tools must be
dry or preheated before immersion to remove
moisture and to prevent MgO and hydrogen for-
mation (potential fire or explosion source).
Melt holding/transfer —
Actions such as
stirring, charging, ladling, poor venting, re-
moval of dross and sludge, and excessive move-
Abdallah Elsayed*
Sophie Lun Sin
Comondore (Ravi)
Ravindran, FASM*
Centre for
Near-net-shape
Processing of
Materials,
Ryerson University
Toronto
Understanding
both the origin
and procedures
for removing
inclusions in
magnesium
alloys results
in castings
with enhanced
mechanical
and corrosion
properties.
*Member of
ASM International
TABLE 1 — INCLUSIONS IN Mg ALLOYS
[4-6]
Type
Morphology Dimensions (
m
m) Density (g/cm
3
)
Oxides
MgO
Particles, films
10-300
3.58
0.5-1 (thickness)
50-400 (length)
MgO-Al
2
O
3
(spinel)
Particles
3.58
Nitrides
Mg
3
N
2
Particles, films
10-300
2.71
0.5-1 (thickness)
50-400 (length)
Carbides
Al
4
C
3
Particles
0.1-10
2.36
CaC
2
Particles
2-20
2.22
Chlorides and salts
MgCl
2
Particles
10-50
2.32
NaCl
Particles
10-50
2.17
CaCl
2
Particles
10-50
2.15
KCl
Particles
10-50
1.98
Iron-rich intermetallic compounds
Al
8
(Mn,Fe)
5
,
a
-AlMnFe,
Particles,
<20
4-7
(Mn,Fe)
5
Si
3
, Al
8
(Mn,Fe)
4
RE,
a
-Fe,
needles
Fe
2
(Si,B), Fe
3
(Al,Si), (Fe, Mn)
3
Si