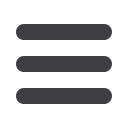
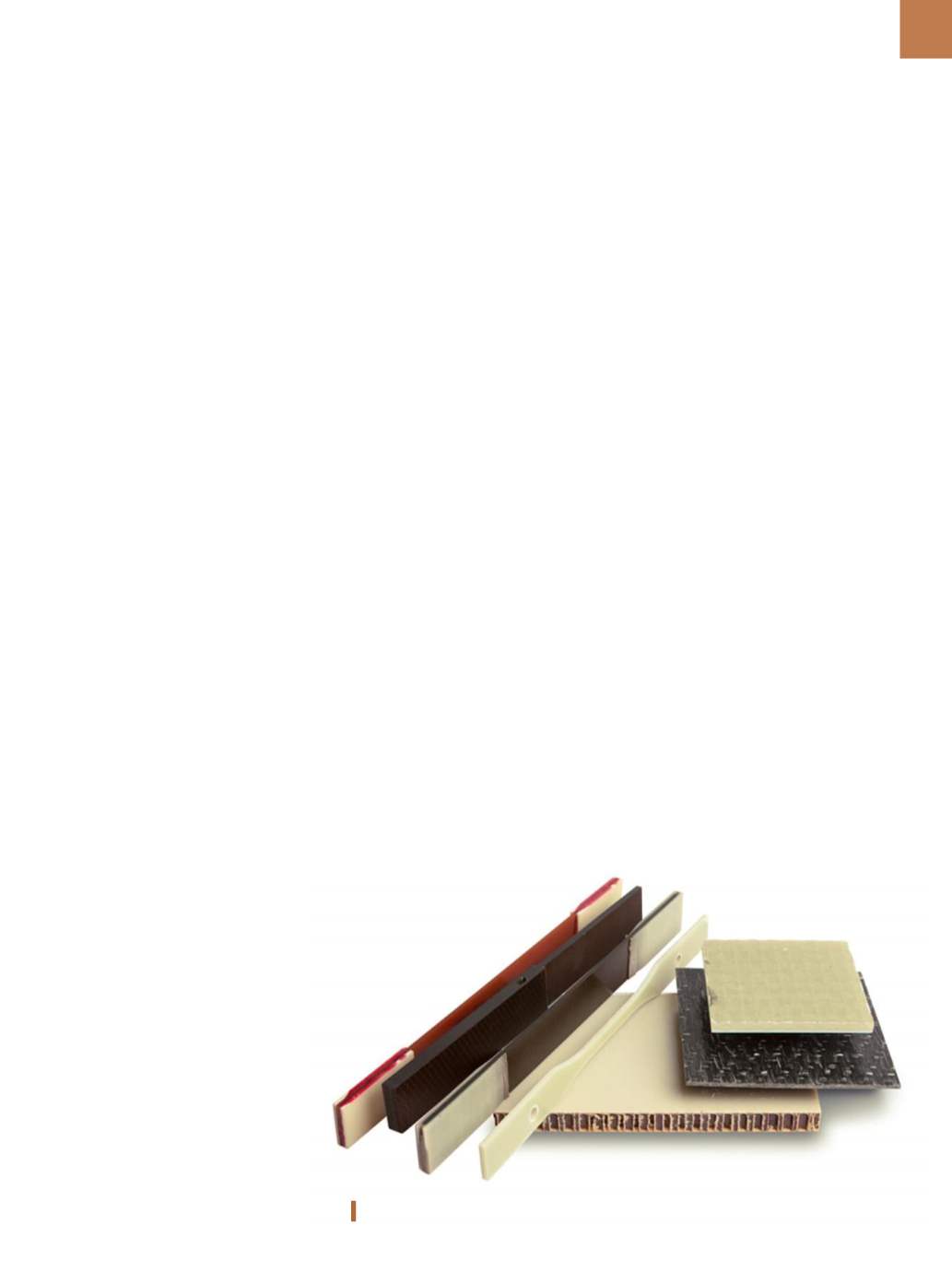
A D V A N C E D
M A T E R I A L S
&
P R O C E S S E S |
M A R C H
2 0 1 6
2 1
MECHANICAL TESTINGOF
AUTOMOTIVE COMPOSITES
Successful use of composite materials requires a thorough understanding
of their mechanical properties.
Typical composite test specimens.
A
utomotive manufacturers are
employing a wide range of new
materials to decrease the weight
of their vehicles and reduce emissions.
These materials include new, high-
strength steel and aluminum alloys,
and a huge range of plastics and com-
posites. Of these materials, continuous
carbon fiber polymer composites offer
the greatest potential for lightweight
structures, yet many barriers inhibit
their widespread adoption. Currently,
the cost and process times of composite
parts are significantly higher than tradi-
tional metals. This is being addressed
by the development of new matrix ma-
terials and manufacturing processes.
Recycling of composite materials is be-
ing investigated and progress is being
made with new thermoplastic matrix
composite materials, which are easier
to recycle than thermoset matrix mate-
rials. Finally, the unique nature of com-
positematerials presents designers and
engineers with new challenges, and the
successful use of composite materials
requires a thorough understanding of
their mechanical properties.
MECHANICAL PROPERTIES
AND TESTING
The properties of most metals and
plastics are more or less isotropic (i.e.,
independent of direction) and homog-
enous (i.e., they consist of a single uni-
form phase). Consequently, their me-
chanical properties can be described by
a small number of material constants
obtained from a simple tensile test. In
contrast, describing the properties of
anisotropic and inhomogeneous com-
posite materials requires many more
material constants obtained from a
range of mechanical tests. For example,
determining the static bulk properties of
composite materials requires tension,
compression, and shear tests. Other
tests are used to characterize proper-
ties related to inhomogeneity, such as
interlaminar fracture toughness, which
measures resistance to delamination.
Creep and fatigue testing is needed to
predict the long-term durability of a ma-
terial in service. It is often necessary to
understand how the material behaves
under high rates of strain—conditions
that would be encountered in a crash.
Further, tests generally need to be con-
ducted over a range of temperatures and
other environmental conditions.
TEST TYPES
Determining the static bulk prop-
erties of a composite laminate requires
tension, compression, shear, and flex
tests. In most cases, the properties of
interest are
in-plane
properties (in the
direction of the plane), but in some cas-
es the
through-thickness
properties (in
a direction normal to the plane of the
laminate) are also required.
In-plane tension testing of com-
posite laminates is similar, in principle,
to a traditional metals or plastics ten-
sion test. The test specimen is usually a
rectangular coupon cut from a laminate
panel in a specific direction relative to
the fiber direction, such as specimens
cut from a unidirectional laminate
panel at 0° and 90° orientations to the
fiber direction. Specimens are usually
provided with bonded tabs to prevent
the grip jaws from damaging the com-
posite and causing premature failures.
Through-thickness tension testing on
thin laminates can be performed, indi-
rectly, by subjecting a curved laminate
beam to a four-point bending test. This
TECHNICAL SPOTLIGHT