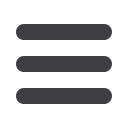
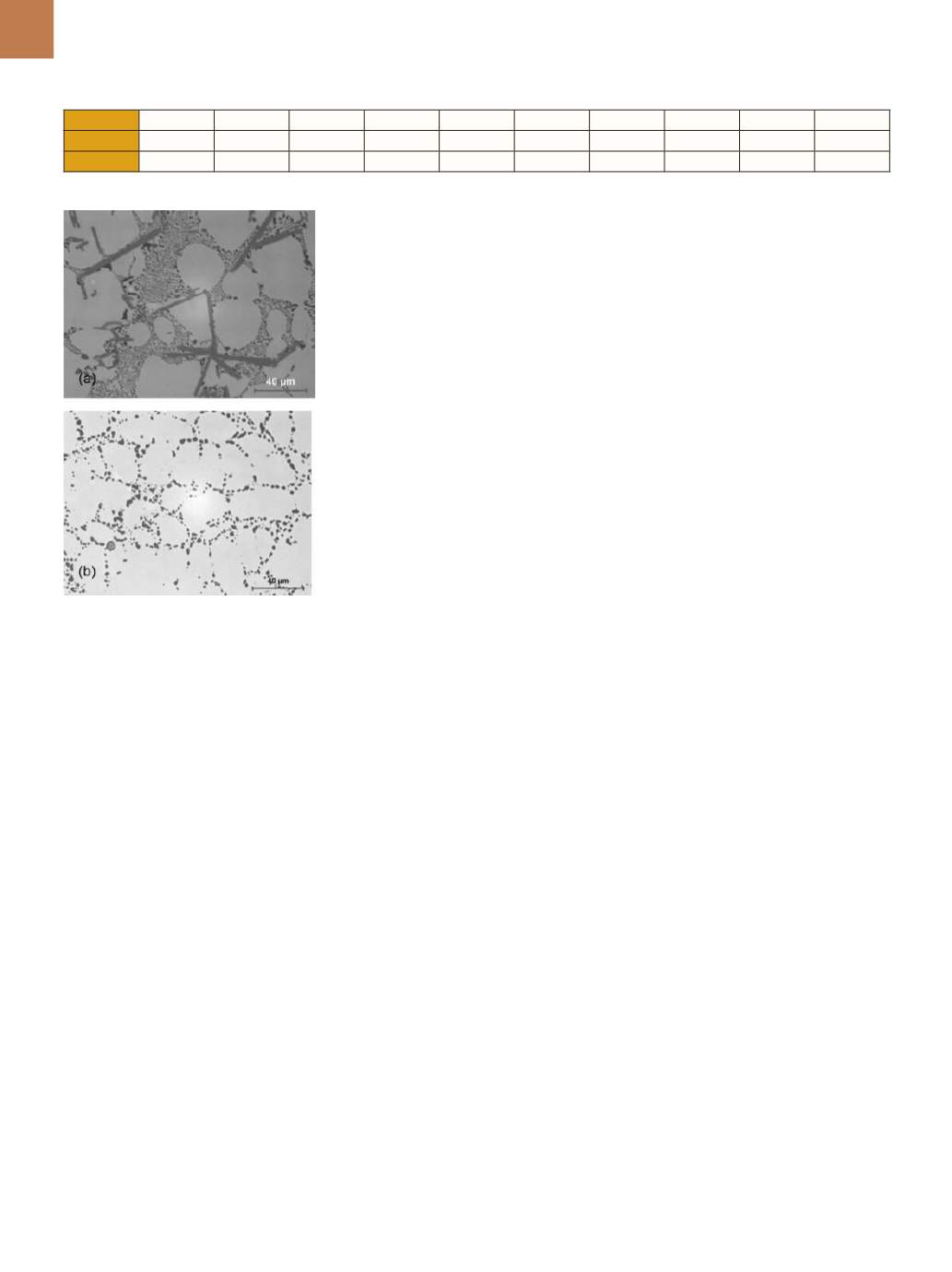
A D V A N C E D M A T E R I A L S & P R O C E S S E S | M A R C H 2 0 1 6
1 8
TABLE 1
—
CHEMICAL COMPOSTIONS OF COMMERCIAL A380 AND RESEARCH AL ALLOYS, WT%
Alloy
Si
Cu
Mg
Fe
Sr
Mn
Zr
Ti
V
Al
New
7.02
0.95
0.48
0.09
0.012
0.005
0.47
0.21
0.30
Bal
A380
9.5
3.4
0.07
0.90
<0.001
0.18
0.0073 <0.001 0.0087
Bal
Fig. 2 —
(a) As-cast microstructure of re-
search alloy; (b) microstructure after T6 heat
treatment. Chemical composition listed in
Table 1.
different lattice parameters. They in-
clude Al
6.7
Si
1.2
TiZr
1.8
, Al
21.4
Si
4.1
Ti
3.5
VZr
3.9
,
and Al
2.8
Si
3.8
V
1.6
Zr, which are desig-
nated in the literature as (AlSi)
3
(TiZr),
(AlSi)
3
(TiVZr),
and
(AlSi)
2
(VZr),
respectively.
Another positive modification of
the alloy microstructure occurs in the
Fe-containing
β
-Al
5
FeSi phase, which is
generally needlelike in shape and detri-
mental for alloy strength and ductility.
As a result of alloying with Zr-Ti-V, the
Fe-containing
β
-Al
5
FeSi phase converts
into the Al
5.1
Si
35.4
Ti
1.6
Zr
5.7
Fe phase with
a general formula of (AlSi)
2
(TiZr)Fe.
Zr always forms complex intermetallics.
The intermetallic phases are distribut-
ed most often in interdendritic regions.
TESTING HIGH-TEMPERATURE
PERFORMANCE
To test high-temperature perfor-
mance, alloys were subjected to var-
ious heating cycles. Test results were
compared with properties of commer-
cial A380 alloy, currently the industry
choice for targeted automotive appli-
cations. As-cast hardness of A380 al-
loy (83 HRF) was over 10 units higher
than that of the research alloy. Results
of isochronal aging at temperatures
up to 500
°
C show that the research al-
loy achieved peak aging hardness at
approximately 200
°
C, and a hardness
difference existed at the peak between
the research alloy and A380 grade
[9]
. For
temperatures up to 150
°
C, A380 experi-
enced a hardness reduction compared
with an increase for the research alloy.
Temperatures of phase stability
were identified using electron micros-
copy, electron backscatter diffraction,
and high-temperature x-ray diffraction.
During the solutionizing step of the T6
heat treatment at 510
°
C followed by
525
°
C, the research alloy primarily ex-
perienced dissolution of Cu-containing
phases (Fig. 2b). Some other phases
including eutectic silicon experienced
only partial dissolution. Some phases
were not affected by the solutionizing
temperature, indicating their high sta-
bility. In-situ x-ray diffraction of bulk
material at room and elevated tem-
peratures is useful to directly test alloy
phase stability. For the research alloy,
increasing the temperature from 200
°
to 400
°
C led to dissolution of the Si eu-
tectics in the Al matrix. Also, Al
2
Cu and Q
phases dissolved with increasing tem-
perature from 300
°
to 500
°
C, and were
not detected by x-ray above 500
°
C. In
contrast, phases containing transition
metals V, Ti, and Zr remained present
up to temperatures between 695
°
and
705
°
C, i.e., after reaching liquid state,
indicating their high stability.
STATIC MECHANICAL
PROPERTIES
Microstructural
modifications
through alloying additions affect work
hardening and texture, tensile and
compressive deformation behavior, hot
deformation, and movement of disloca-
tions during deformation at increasing
temperatures. In automotive engine ap-
plications, Al alloysare subjected tocom-
plex stress scenarios. The component
typically undergoes compression during
heating and is under tension during sub-
sequent cooling. Therefore, hot tensile
and compressive behavior are relevant
for good material performance.
The as-cast research alloy had a
yield strength (YS) of 162 MPa, an ulti-
mate tensile strength (UTS) of 252 MPa,
and an elongation of 3.9% inmonotonic
loading at room temperature. Proper-
ties improved substantially after the T6
heat treatment, resulting in 287 MPa YS,
343 MPa UTS, but lower elongation of
2.6% (Fig. 3a). Compression properties
were 312 MPa YS, compressive strength
of 418 MPa, and a compressibility value
of 52.2% (Fig. 3b). It was established
during compression experiments that
decreasing deformation temperature
in the range of 200
°
to 400
°
C, and to a
lesser extent increasing the strain rate
in the range of 10
-3
– 1 s
-1
, led to higher
flow stress.
During hot compression deforma-
tion, fracturing and reorientation of the
second phase particles occur, and both
phenomena are influenced by tem-
perature and strain rate. For both the
research and A380 alloys, intermetallic
precipitates experience substantially
more frequent cracking than the eu-
tectic silicon. Although second phase
particles in both alloys have a similar
morphology, there is a difference in their
performance during hot compression. In
the research alloy, eutectic silicon and
intermetallics were more resistant and
experienced less frequent fracturing.
Also, both the eutectic silicon and inter-
metallic particles of complex chemistry
are more resistant to rotation within the
matrix during hot deformation.
CREEP PROPERTIES
Creep-rupture tests provide rel-
evant information when considering