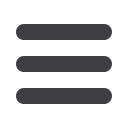
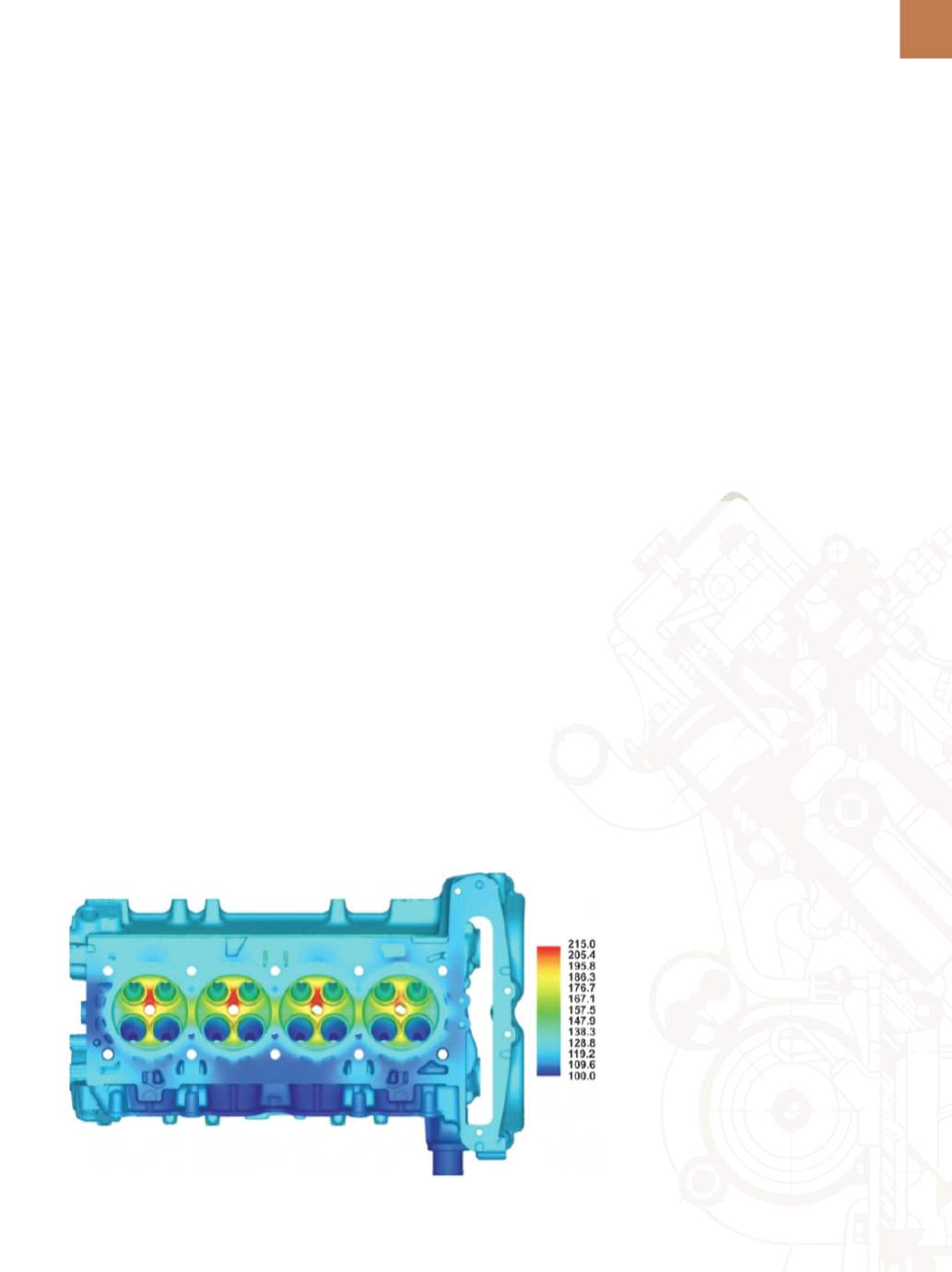
A D V A N C E D
M A T E R I A L S
&
P R O C E S S E S |
M A R C H
2 0 1 6
1 7
Fig. 1 —
Modeled temperature distribution within a combustion engine
[2]
.
T
he use of aluminum alloys in au-
tomotive applications continues
to grow because they offer an
economically viable way to improve
vehicle performance and efficiency, en-
suring safety and durability, enhancing
fuel consumption, and reducing harm-
ful emissions. The U.S. Environmental
Protection Agency and U.S. Depart-
ment of Transportation issued 2017-
2025 corporate average fuel economy
(CAFE) targets for both passenger cars
and light trucks calling for more than
50% improvement compared with cur-
rent targets. Substantial improvements
in fuel economy can be achieved by
increasing engine performance and by
replacing large engines with smaller
ones in the same vehicle class. Smaller
engines require lighter support, which
means additional weight reduction.
Computer simulations of a diesel en-
gine show that a 60% increase in power
and torque requires an increase in max-
imum cylinder-head pressure of 180 to
300 bar, an increase in peak tempera-
ture on the head combustion face of
215
°
to 275
°
C, and of 150
°
to 190
°
C on
the water-jacket face
[1]
. These goals re-
quire significant technological changes
in engine materials.
Cast aluminum alloys are attrac-
tive structural materials for a number
of automotive applications including
strategic
powertrain
components,
such as engine blocks and cylinder
heads, where permanent-mold cast-
ing and high-pressure die casting are
cost-effective mass production meth-
ods (Fig. 1). The most versatile casting
aluminum alloys are Al-Si alloys, ac-
counting for the majority of automotive
cast parts. The maximum operating
temperature of 180
°
C for existing Al-Si
casting grades (Al-Si-Cu and Al-Si-Mg) is
too low for new combustion-engine de-
signs, where an improvement in perfor-
mance requires both increasing service
temperature and internal pressure. This
article describes research aimed at de-
veloping cast aluminum alloys with the
necessary high-temperature tensile and
fatigue strengths to withstand the mod-
ern automotive engine environment.
INCREASING THERMAL
STABILITY
The strengthening mechanism
of current Al alloy grades becomes in-
effective at the service temperature
of new engine designs due to rapid
coarsening and dissolution of their mi-
crostructure controlling phases. This
requires modifying the base composi-
tion of aluminum alloys. Elements in-
vestigated for this purpose include Ni,
Fe, Cr, Mn, Co, Zr, Gd, Hf, Y, Sc, Nb, and
V. When alloyed with Al, some elements
form incoherent dispersoids, such as in
the Al-Fe-Ce, Al-Fe-V-Si, Al-Fe-Ce-W, and
Al-Cr-Zr-Mn systems. Alloying Al with Sc
forms coherent dispersoids, where their
low fraction is effective in preserving
high-temperature properties. Strength-
ening is also induced through incoher-
ent oxide particles such as in Al-Mg and
Al-Ti systems, but resulting alloys have
low ductility and fracture toughness.
For effective improvement of the high
temperature performance of Al, alloy-
ing elements should
[3]
:
•
Be capable of forming thermally
stable strengthening phases
•
Have low solid solubility in the Al
matrix
•
Have low diffusivity in the Al matrix
•
Retain the ability for the alloy to be
conventionally solidified
Transition metals, which form
thermally stable and coarsening-
resistant precipitates, arepromising can-
didates to achieve this. Phase diagrams
and crystallographic data indicate that
some transitionmetals crystallizewith Al
to form stable Al
3
M-trialuminides. Trialu-
minide intermetallic compounds (Al
3
X)
are good candidates for dispersoids
and precipitates in high-temperature
aluminum alloys. High symmetry cubic
L1
2
and related tetragonal D0
22
and D0
23
structures are prevalent among some
transition metals. This work focuses on
Zr, V, and Ti combined with the Al-Si-Mg-
Cu cast matrix
[4-7]
.
The best results were generat-
ed for simultaneous micro-additions
(0.1-0.5 wt%) of Zr, V, and Ti to the hy-
poeutectic Al-7Si-1Cu-0.5Mg (wt%)
base. The alloy’s chemical composition
is listed in Table 1.
ALLOYING IMPACT ON
MICROSTRUCTURE
Al-Si-Cu-Mg base alloys have a
complex microstructure consisting of
a number of phases including den-
dritic
α
-Al, modified eutectic silicon,
blocky-type copper base
θ
-Al
2
Cu phase,
ternary eutectic Al-Al
2
Cu-Si phase,
Mg-rich Chinese script-like Q-phase
Al
5
Cu
2
Mg
8
Si
6
, and Fe-rich needlelike
π-phase Al
8
FeMg
3
Si
6
[8]
. Additions of tran-
sition metals make this microstructure
muchmore complex (Fig. 2a). For exam-
ple, the presence of Ti leads to an addi-
tional needlelike phase (AlSi)
3
Ti, while
additions of Ti and Zr form needlelike
phase (AlSi)
3
(TiZr). The simultane-
ous presence of Zr-Ti-V leads to new
unique (AlSi)
x
(TiVZr)-type phases with
D0
22
/D0
23
tetragonal crystal structure and