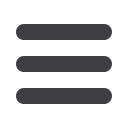
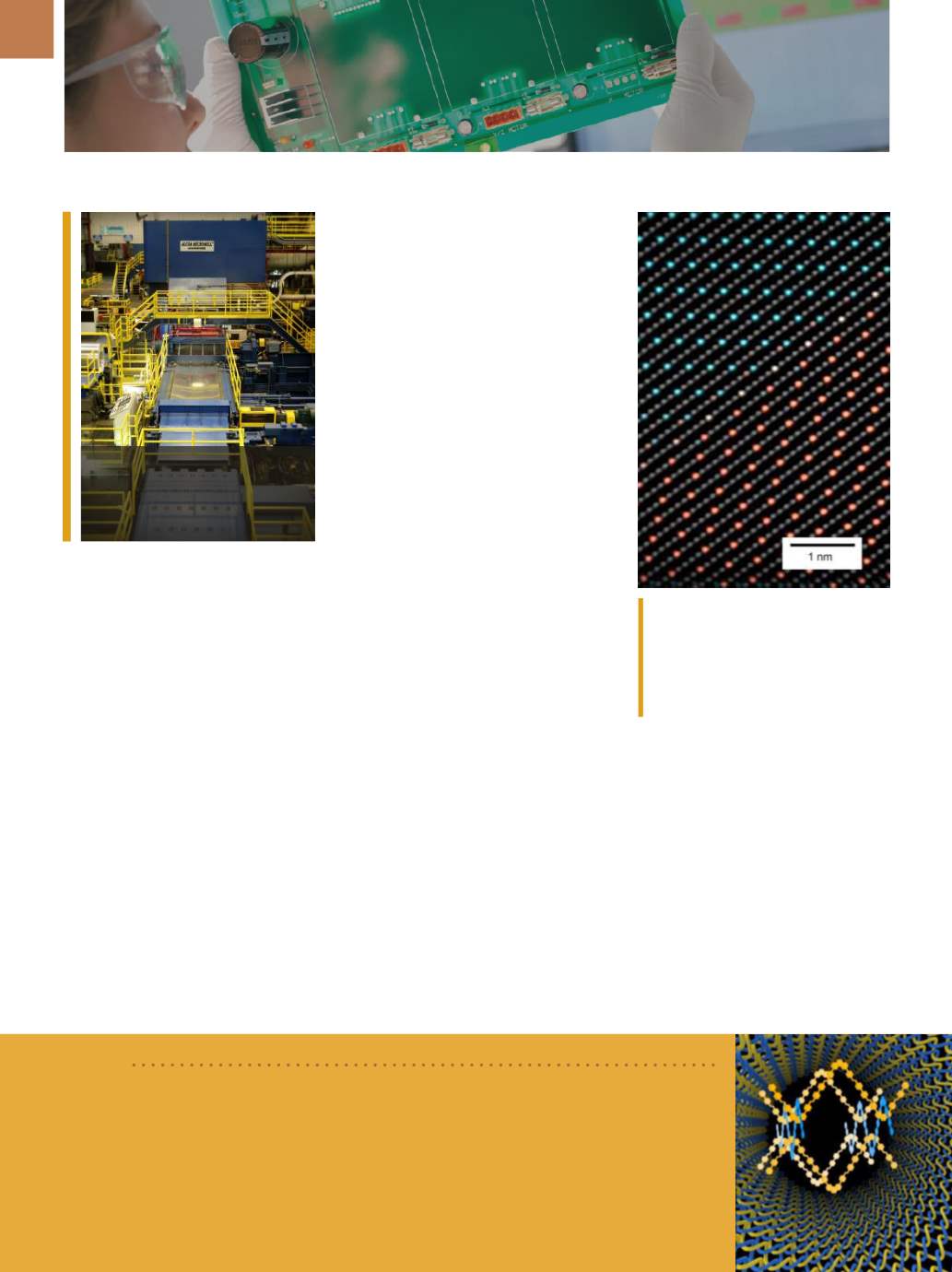
FORD AND ALCOA DEVELOP
NEXT-GEN ALUMINUM
Ford Motor Co., Dearborn, Mich.,
and Alcoa Inc., New York, are collabo-
rating to produce next-generation auto-
motive aluminum alloys that are more
formable and design-friendly than
previous versions. Ford will use Alcoa’s
Micromill material in multiple compo-
nents on the 2016 F-150, becoming the
first automaker to commercially use
the advanced aluminum. Alcoa’s Micro-
mill technology produces an aluminum
alloy that is 40% more formable than
today’s automotive aluminum. The in-
creased formability makes it easier to
shape into intricate forms, such as the
inside panels of automobile doors and
external fenders. Increased strength
enables use of thinner aluminum sheet
without compromising dent resistance.
Micromill is reportedly the fastest, most
productive aluminum casting and roll-
ing system in the world combining mul-
tiple technologies into a streamlined
production system. While a traditional
rolling mill takes around 20 days to turn
molten metal into coil, Micromill does it
in 20 minutes.
Ford began using Micromill ma-
terial in 2016 F-150 production in late
2015, and plans to increase its use over
the next several years on a range of
vehicle components and future plat-
forms. By using the highly formable
material, parts constructed of multiple
pieces can be manufactured as a single
part, reducing complexity and assem-
bly time. Target applications include
critical strength structural parts as
well as exterior panels that must meet
strict surface quality requirements.
corporate.ford.com,
alcoa.com.
KECK FOUNDATION AWARDS
$1 MILLION TO STUDY
ANTI-THERMAL BEHAVIOR
The W.M. Keck Foundation, Los
Angeles, awarded a $1 million grant
to Lehigh University, Bethlehem, Pa.,
to study the mechanisms that govern
anti-thermal processes that appear to
reverse nature. The work has potential
to revolutionize the basic understand-
ing of thermal processes and inform
development of new materials that
could withstand higher temperatures. A
Alcoa’s Micromill technology reduc-
es the time to transformmolten
metal into aluminum coil from
20 days to 20 minutes.
High magnification image shows how
atoms are arranged on both sides of the
twin boundary, represented by yellow
atoms in the center. Courtesy of Martin
Harmer and Christopher Marvel, Lehigh
University.
BRIEF
An international team led by scientists at the DOE’s
Lawrence Berkeley National Laborato-
ry
and the
University of California, Berkeley
reports weaving the first 3D covalent organic
frameworks (COFs) from helical organic threads. The woven COFs display advantages in
flexibility, resiliency, and reversibility over previous COFs—materials prized for their potential
to capture and store CO
2
then convert it into valuable chemical products
. lbl.gov.breakthrough in this area could lead to
significant increases in engine efficien-
cy, for example, saving billions of dol-
lars in fuel costs, say researchers. The
grant was awarded to principal investi-
gator Martin Harmer, Alcoa Foundation
Professor of Materials Science and En-
gineering. Harmer’s collaborators are
Elizabeth Holm and Gregory Rohrer,
both professors of materials science
and engineering at Carnegie Mellon
University, Pittsburgh.
lehigh.edu.
EMERGING TECHNOLOGY
A D V A N C E D M A T E R I A L S & P R O C E S S E S | M A R C H 2 0 1 6
1 2
COF-505 is the first 3D covalent organic framework to
be made by weaving together helical organic threads.