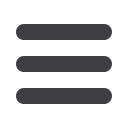

A D V A N C E D
M A T E R I A L S
&
P R O C E S S E S |
M A R C H
2 0 1 6
1 9
durability of materials for use in power-
train applications. Creep deformation is
slow, continuous, and time dependent.
In contrast to elastic/plastic deforma-
tion where strain is mainly a function of
stress and temperature, creep strain is a
function of time as well. In-situ neutron
diffraction was used for an in-depth
analysis of creep evolution in the alloys
under elevated temperatures of 200
°
and 250
°
C
[10]
. The focus of this exper-
imental research includes elastic and
plastic tensile creep properties near the
yield strength of the material, typical in
automotive powertrain applications.
associated with power law-governed
creep. The creep mode shifted to the
power-law breakdown as the applied
load was incrementally increased; this
was dominant for most testing condi-
tions. Crystallographic planes (111) and
(311) were typically the main planes
that supported most of the applied
load during testing of both alloys. Acti-
vation of the additional crystallograph-
ic planes, such as (200) and (220) in
the research alloy to support the load
at the higher load settings and at the
higher temperature of 250
°
C was due to
accumulation of dislocations through
the loading stages and by thermal
activation.
FATIGUE BEHAVIOR
The failure mechanism in automo-
tive powertrain components subjected
to high pressure, changing high loads,
and thermal gradient is often fatigue
related. Load cycling between low and
high stress leads to a shorter lifetime
than a static load at high stress. Fatigue
is of special importance for cast alloys
due to a variety of casting defects,
which serve as sources of crack initia-
tion. Combined analysis of creep and
fatigue provides valuable input into
the alloy performance. The response of
cyclic stress amplitude as a function of
the number of cycles at different strain
amplitudes was measured for the re-
search alloy. Fatigue life decreased
and stress amplitude increased with
increasing strain amplitude for the T6
temper condition. At lower total strain
amplitudes in the range of 0.1-0.2%, cy-
clic stress amplitude remained essen-
tially constant throughout the entire
fatigue life. At higher total strain am-
plitudes in the range of 0.4-0.6%, cyclic
hardening occurred from the beginning
and continued to failure for the T6 tem-
pered samples as cyclic deformation
progressed
[11]
.
Fatigue lifetime S-N curves for
both alloys in the T6 tempered condi-
tion are shown in Fig. 4
[6]
. Fatigue life in-
creasedwith decreasing total strain am-
plitudes for all alloys, and fatigue life of
the research alloy is significantly longer
at all levels of total strain amplitudes.
According to the testing regime, if alloy
Test data enabled defining creep mech-
anisms characteristic for each stage of
incremental loading. The research alloy
exhibited considerable improvement in
creep resistance over that of A380 grade
at 200
°
and 250
°
C in terms of ultimate
strength and total (plastic and elastic)
creep. The improvement was explained
by profiles of elasticmicrostrains, which
indicate that additional crystallograph-
ic planes were activated in supporting
the applied load.
Test results showed that the
main mechanism is dislocation creep,
which initiates at the lower load setting
Fig. 3 —
(a) Ultimate tensile strength and (b) compressive strength of research and A380 alloys
after T6 heat treatment tested at room and elevated temperatures.
(a)
(b)