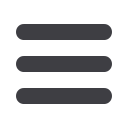
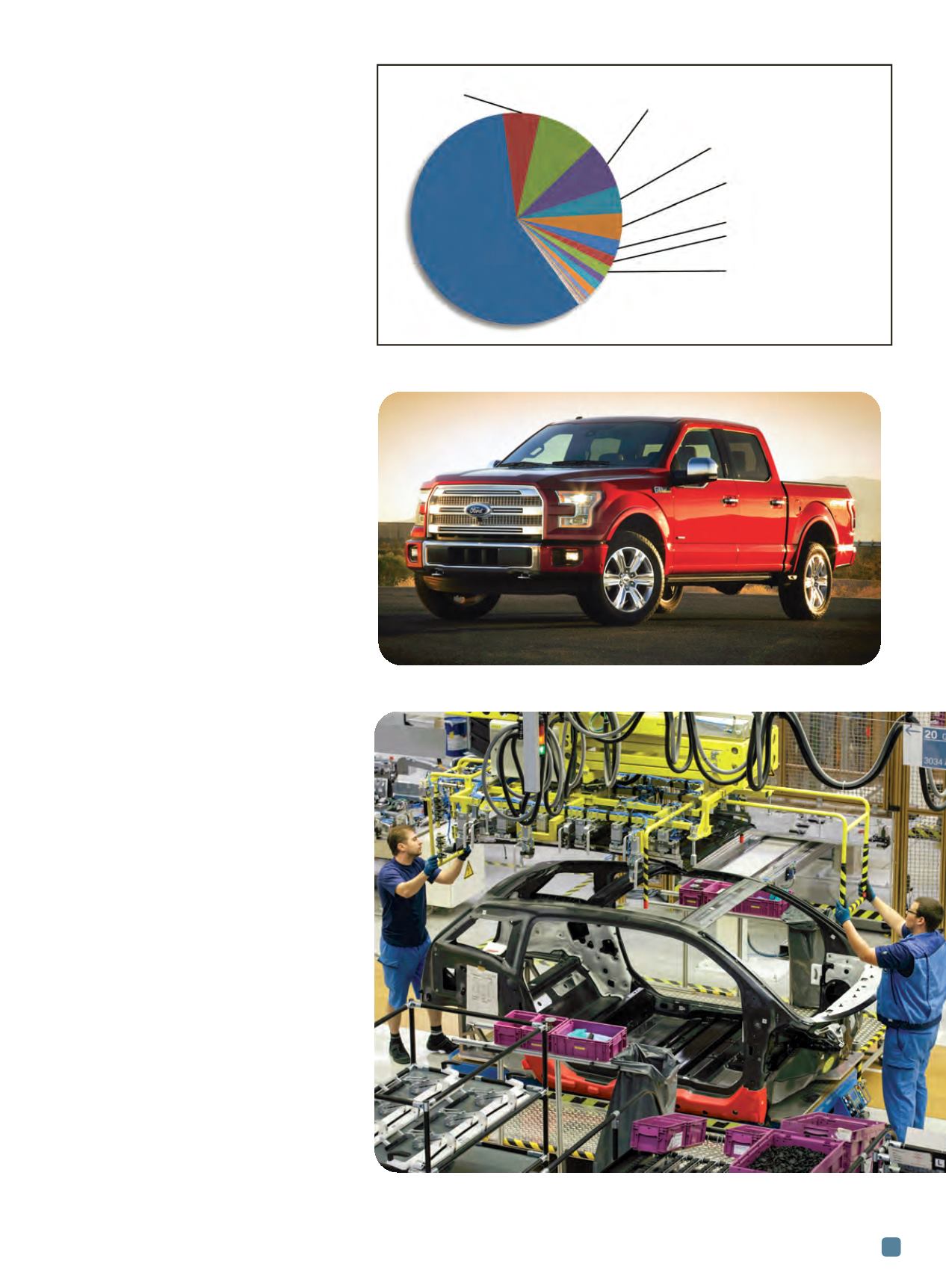
ADVANCED MATERIALS & PROCESSES •
JUNE 2014
23
Entry occurred first in the racing and perform-
ance classes, with mainstream market applica-
tions emerging more recently. Composites also
played an important role in production of mid-
20th century models of General Motors’
Corvette. While steel was actually lighter than
fiberglass at the time, the connection between
lightweight composites and high performance
was cemented in the mind of the consumer.
Carbon fiber-reinforced plastics (CFRPs)
deliver the benefits of high strength with ultra-
low weight, but require costly technology in-
vestments. Low volume production makes it
difficult to exercise economies of scale using
CFRPs in select applications. Supply chain op-
timization, refinement of manufacturing tech-
niques, and installation of quality assurance
infrastructure are key to volume applications of
CFRPs in the automotive industry (Fig. 4).
BMW has invested substantially in each of
these areas. Last year, the automaker an-
nounced its i3 and i8 all-electric vehicles, which
both have a body consisting solely of CFRPs
(Fig. 3). Vehicles are constructed of two major
units—a CFRP-based passenger portion and an
aluminum-based drive module.
Recognizing the challenges involved in a
pure composites-based approach to light-
weighting, many manufacturers are employing
mixed material strategies. Applying aluminum
and aluminum alloys where strength is required
yet complex shapes are desirable, designers
achieve weight reduction goals without sacri-
ficing performance or form.
Joining steel, aluminum, and alloy-based
components poses one set of challenges, while
joining metals to composites creates new ones.
Structural adhesives must be thoroughly char-
acterized to assess their capacity to cohesively
join dissimilar surfaces, manage the varying ex-
pansion rates of the materials to which they are
bonded, and enable the properties profile re-
quired by the application. Adhesives create spe-
cific quality control challenges, not the least of
which is environmental. Temperature control
is necessary to ensure correct bonding and cur-
ing of adhesives on a tight time schedule, says
Baron. Maintaining uniform adhesive thickness
is also critical. However, he notes that even ad-
hesives can be problematic with regard to light-
weighting initiatives, because bonding
compounds typically weigh more than rivets or
spot welds.
Fig. 1 —
Advanced composites drive down weight requirements, by identified
component manufacturer, 2013. Courtesy of Composites Forecasts and Consulting LLC.
Fig. 2
—
The 2015 Ford F150 boasts a body comprised of aluminum alloys, reducing
truck weight by 700 lb.
Fig. 3
—
Final assembly of the BMW i3 electric vehicle at the manufacturer’s Leipzig,
Germany, site. Courtesy of BMW AG.
Advanced Composites by Component Manufacturer, 2013
SGL Brembo Carbo Tech
6% Industries GmbH ITCA Colonnella 7%
9%
Automobili Lamborghini 4%
Voestalpine Plastics
Solutions 4%
Sortira 3%
Brakes
(data not available) 2%
Morrison Molded Glass Co.
2%
BMW – Germany
58%