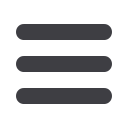
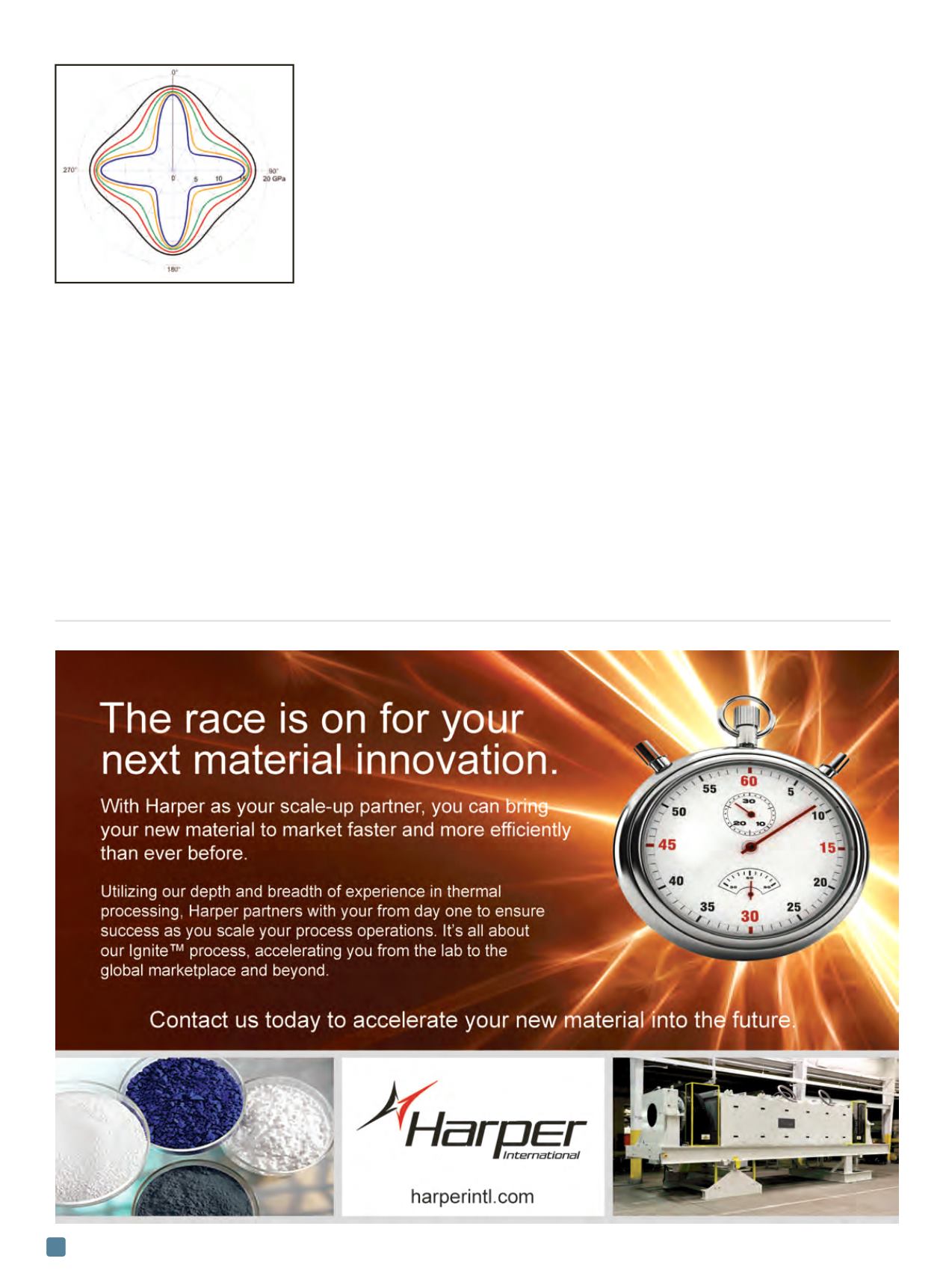
from 26° to 38°C. When an
automatic system of adaptive
frequency control was used,
surface temperatures were
controlled within ±0.5°C on
all specimens and machine
time was reduced by more
than 27%.
Fatigue testing of compos-
ites is still evolving in terms of
scientific understanding of
the phenomena, but meets an
urgent industrial need. A va-
riety of failure mechanisms at
a range of length scales are interacting, and are so different
from those in metals that using the term
composites fatigue
might be misleading. The effects of processing (e.g., layup
sequence) can be more severe than in metals, as are the re-
sults of different temperatures or strain rates. The challenges
of producing representative samples are also considerable.
An ongoing debate continues on how best to define speci-
men failure. It is agreed that specimen rupture is not a good
metric, yet it remains the accepted measure because no sin-
gle construction (for example, xyz% reduction in modulus)
that can be used comparably across the entire, diverse fam-
ily of polymer matrix composites has been identified.
Considering that metals fatigue came into being 150
years ago, it is apparent that despite numerous unsolved
problems, composites fatigue is progressing rapidly after
only 30 years. It is expected that industrial adoption will
result in pragmatic improvements.
High-speed testing
More recently, the demand for lightweighting in the au-
tomotive sector has prompted manufacturers to investi-
gate high-performance composites use in more critical and
structural parts, as a way to reduce mass even further than
what is possible with modern metals technologies.
Approximately 10 to 15 years ago, strain-rate testing of
metals caused a minor revolution in automotive materials
evaluation because it offered much more informative data
on differences in crash scenarios. An initial phase of realiza-
tion and assessment resulted in many automotive compa-
nies adopting polymer matrix composites as a worthwhile
investment. Processing and designing with structural com-
posites has significantly different challenges, but as with fa-
tigue testing, initial work has largely employed similar
models as those for metals as a starting point, so experimen-
tal data is essential. For this area of development, existing
equipment and methodologies seem to have helped—a
number of specialized materials test systems found further
use, while many new systems are being built.
ADVANCED MATERIALS & PROCESSES •
JUNE 2014
18
Fig. 3 —
Polar plot of tensile modulus
vs. angle for a simple woven cross-ply
laminate at increasing strain rate.
1) 0.00044 s
-1
, 2) 0.044 s
-1
, 3) 0.44 s
-1
,
4) 4.4 s
-1
, 5) 44 s
-1
. Courtesy of Gude et
al., Mech. Comp. Mat., Vol 45, No. 5.