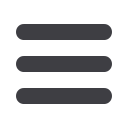
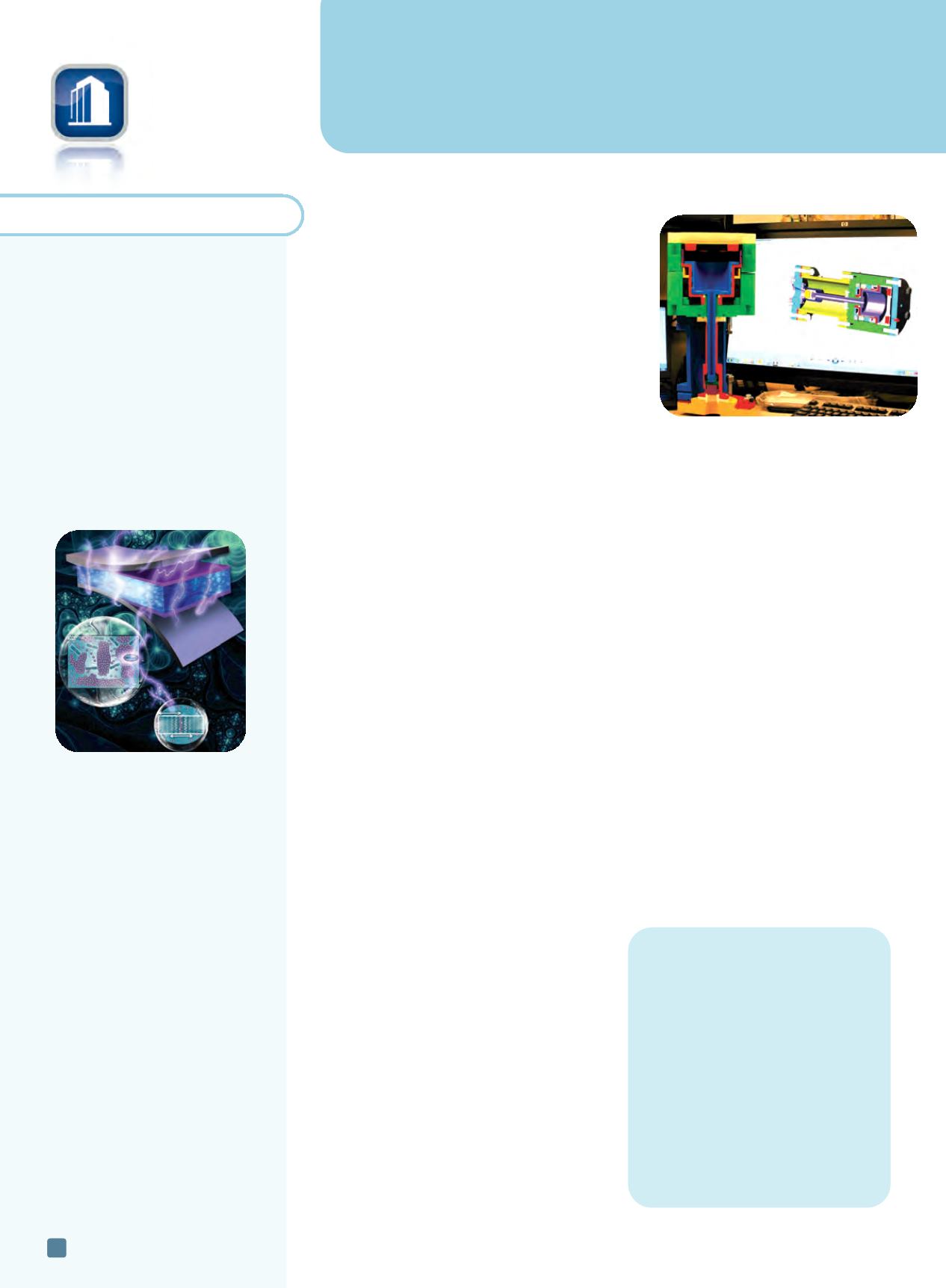
news
industry
3D printing enhances fusion research
ITER, the international fusion research facility,
is now under construction in St. Paul-lez-Du-
rance, France. US ITER staff at DOE’s Oak Ridge
National Laboratory, Tenn., are using desktop 3D
printing to help colleagues design and configure
components more efficiently and affordably. Al-
though full-scale models cast or machined from
metal and other materials continue to have value
and will still be a part of the US ITER development
process (as will 3D computer modeling), the af-
fordability and accessibility of desktop 3D print-
ing offers a number of advantages. “It’s a lot more
time consuming and expensive when you find a
mistake in a metal prototype than in a 3D printed component. 3D printing is very low cost.
With metal, you may have to start over if you can’t re-machine it, ” says Mark Lyttle, an en-
gineer working on the pellet injection and plasma disruption mitigation systems.
ornl.gov.
World-record current in a superconductor
In the framework of the High-Luminosity LHC project, experts from the CERN
(European Organization for Nuclear Research) superconductors team recently obtained a
world-record current of 20 kA at 24K in an electrical transmission line consisting of two
20-m-long cables made of magnesium diboride (MgB
2
) superconductor. This result makes
the technology a viable solution for long-distance power transmission. The result was
achieved at a temperature of 24K (-249˚C) and is kept homogeneous over the 20 m length
of the line by a forced flow of helium gas. Following development, the full 2 × 20 m MgB
2
superconducting line was successfully powered to the world-record current of 20 kA, show-
ing that this technology has great potential for the transmission of electrical power.
http://home.web.cern.ch.
Nanocrystalline copper turns CO into fuel
Matthew Kanan and colleagues at Stanford University and Lawrence Berkeley National
Laboratory, both in Calif., developed a new type of nanocrystalline copper electrode that
catalyzes the electrochemical conversion of carbon monoxide to alcohols. Results from a
standard copper foil electrode were compared with those using nanocrystalline copper
electrodes. Both commercial nanoparticle electrodes were produced by rapidly vaporiz-
ing bulk copper before cooling to form isolated nanoparticles, while researchers produced
electrodes by oxidizing the copper foil and reducing oxide. Like the standard foil electrode,
only 5% of the hydrogen produced by the
commercial nanoparticle electrodes reduced
carbon monoxide. The oxide-derived elec-
trodes were very effective at reducing carbon
monoxide, with about 50% of the product a
mixture of ethanol, acetate, ethylene, and
propanol. Researchers suspect the explana-
tion lies in the grain boundaries between
nanoparticles in their electrode. “The grain
boundary terminates at the surface, and at
that surface termination you can have a dif-
ferent structure that wouldn’t be stable on
the normal surface of a particle,” explains
Kanan.
For more information: Matthew
Kanan, 650.725.3451,
mkanan@stanford.edu,
stanford.edu.
ADVANCED MATERIALS & PROCESSES •
JUNE 2014
14
E
NERGY
T
RENDS
briefs
Research from
North Carolina
State University,
Raleigh, reveals
that solar cell efficiency is based
on a delicate balance between the
size and purity of the interior
layers, or domains. Polymer-based
solar cells are intended to have
two domains, consisting of an
electron acceptor and an electron
donor material. However, these
domains are not separate and
pure, and many more than two can
exist. Current processing methods
create a complex, multi-domain
structure, which impacts all of the
factors involved in the solar cell’s
efficiency.
ncsu.edu.
Interior of a solar cell.
A breakthrough by researchers at
Oregon State University,
Corvallis, could reduce the cost of
solar energy, speed production
processes, use environmentally
benign materials, and make the
sun almost a “one-stop shop” that
produces both the materials for
solar devices and the energy to
power them. The work is based on
use of a “continuous flow”
microreactor to produce
nanoparticle inks that make solar
cells by printing. Simulated
sunlight is focused on the solar
microreactor to rapidly heat it, and
allows precise temperature control
to aid the quality of finished
products. The light used in
experiments was artificial, but the
process could use direct
sunlight—at a fraction of the cost
of current approaches.
oregonstate.edu.
A 3D-printed version of a fast gas valve
for the disruption mitigation system.
Engineers at
University of California San
Diego
created ceramic materials that store
hydrogen safely and efficiently. The com-
pounds are made from mixtures of calcium
hexaboride, strontium, and barium hexa-
boride and manufactured using combustion
synthesis. The ceramics are essentially crys-
talline structures in a cage of boron. To store
hydrogen, calcium, strontium, and boron are
swapped with hydrogen atoms within the
cage. Boron is mixed with metal nitrates and
organic fuels, such as urea, in a box furnace
at temperatures below 400°C (~750°F). The
nitrates and organic fuels ignite, generating
heat and driving the reaction without an ex-
ternal power source.
ucsd.edu.