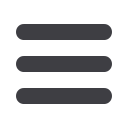
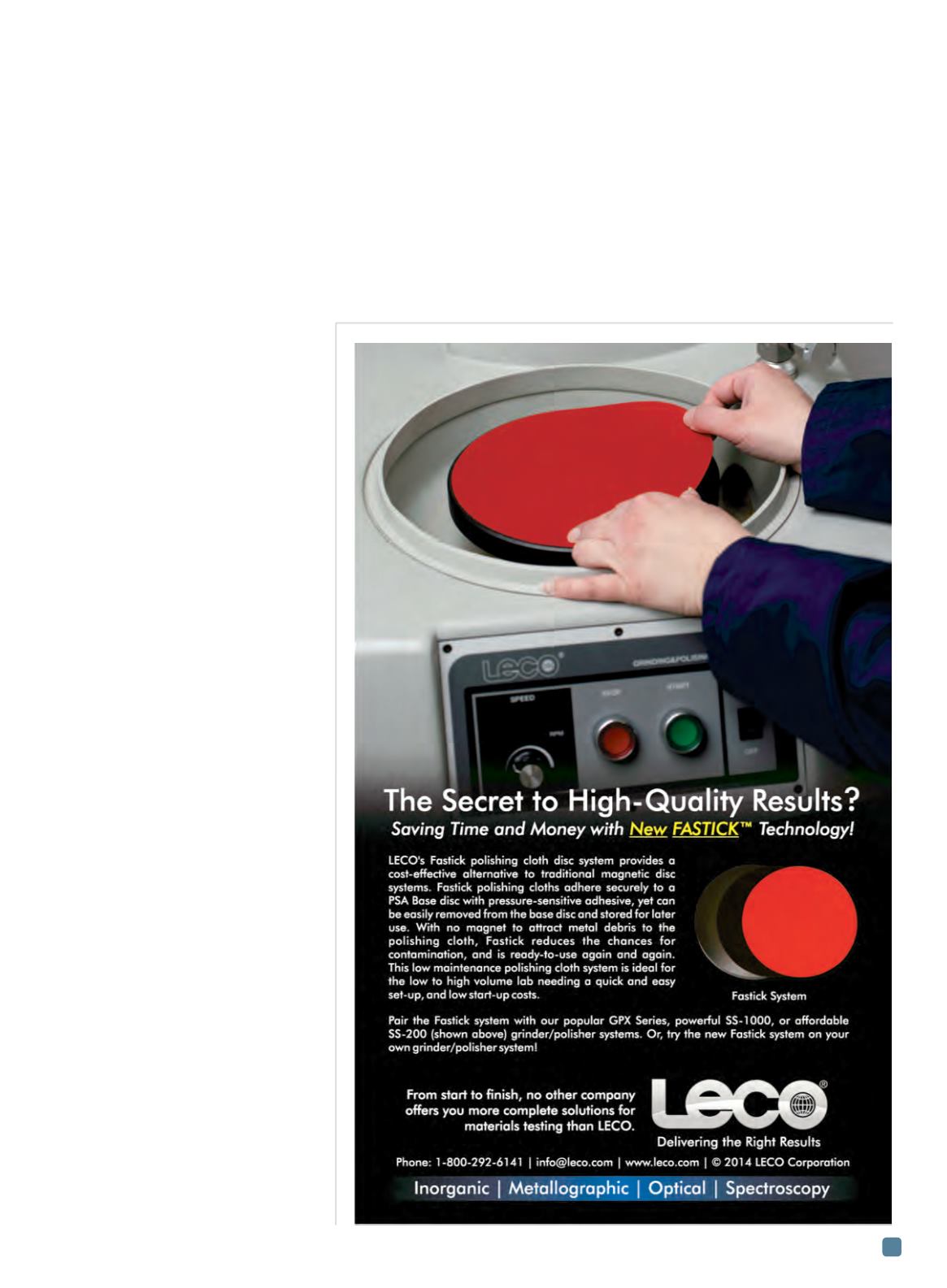
ADVANCED MATERIALS & PROCESSES •
JUNE 2014
19
For example, Fig. 3 shows a startling picture of just how
sensitive composites can be to the very high strain rates
experienced by crash structures. The material modulus at
high strain rate on the axes of reinforcement fibers shows
a noticeable increase of around 15% compared with static
loading, but in the 45° orientation this increase jumps to
more than 250%.
High strain rate testing of composites (and high strength
metals) is by no means trivial. All the problems that might be
encountered with gripping for static tests tend to be exacer-
bated—such as failure at grip, effective tab
bonding, or slippage of untabbed speci-
mens. Also, the test itself is very short—
often less than 2 ms. This is due to test
speeds up to 25 m/s, combined with very
high stiffness and low elongation at break,
typical of structural composites. This re-
quires highly specialized methods of load
and strain measurement, which result in
considerable data analysis.
Load is typically measured using a
piezoelectric transducer within the load-
string, which converts applied stress di-
rectly to potential difference (voltage).
These devices provide extremely high
stiffness and nearly instant response, ideal
for the necessary data acquisition rate.
However, those features have a drawback
in that this type of load cell offers almost
no damping. Therefore, shock loading
with sudden failure and recoil results in
strong, but repeatable, resonances that
must be filtered to accurately determine
applied specimen load. Strain gauge-
based load measurement is sometimes
used, but it must inherently have greater
mechanical compliance, ultimately raising
questions about load trace reliability and
signal conditioning bandwidth.
Similarly, strain cannot be measured by
conventional contact methods used in low-
speed tests. Applying strain gauges to the
specimen and connecting them to high
bandwidth amplifiers is possible, but this
can lead to questions about whether the lo-
cation and area are representative of speci-
men bulk, and if the gauges remain adhered
to the specimen throughout the test. A
more successful method for general strain
measurement is to use a high-speed optical
extensometer, which tracks a simple line of
strong contrast at either end of the gauge
length. The most effective method is to
apply a speckle pattern directly to the whole
area of interest, and then trigger a very
high-speed digital camera to collect a series
of images, which are post-processed using
digital image correlation (DIC). Although
considerably more expensive, DIC systems have great advan-
tages in terms of understanding strain distribution during
failure and the influence of edge effects.
This is also a technically demanding test, as collected
data requires considerable care in interpretation, but these
issues are outweighed by the importance of providing cru-
cial insight into material behavior.
New analytical techniques
Thermography is now making a noticeable impact on