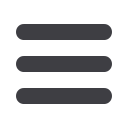
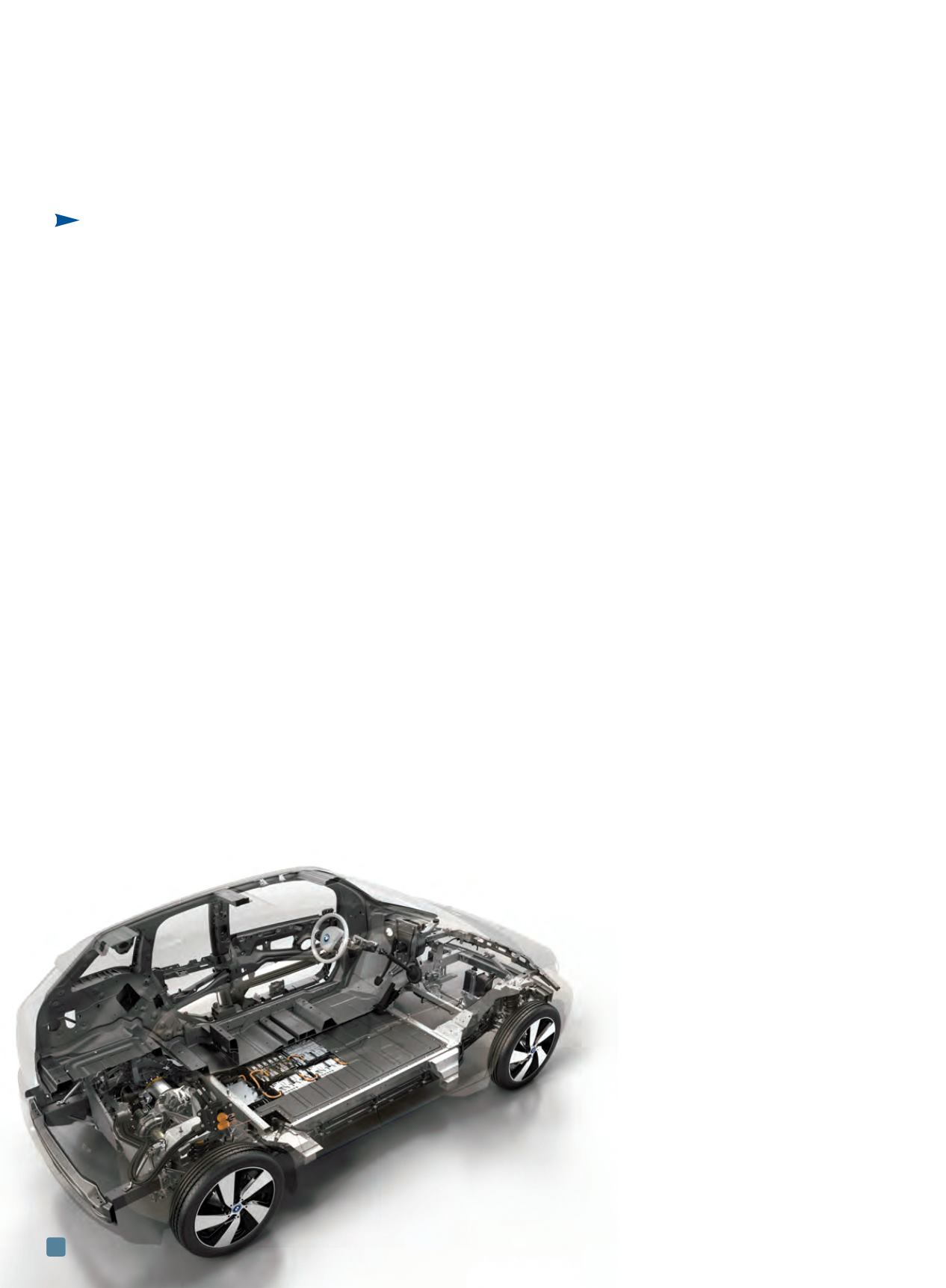
The Role of Materials Testing in
Vehicle Lightweighting
Alex Koprivc
Zwick/Roell
Ulm, Germany
A mixed
materials
strategy calls
for efficiency
and flexibility,
especially
when it comes
to testing
requirements.
ADVANCED MATERIALS & PROCESSES •
JUNE 2014
22
C
onsumer demand for greater fuel effi-
ciency and a changing regulatory en-
vironment have stimulated substantial
interest in alternative materials for passenger
vehicles. Over the past decade, automotive
manufacturers launched a series of initiatives
aimed at reducing weight, improving fuel econ-
omy, and enhancing performance. Materials se-
lection is a key factor in successfully meeting
such challenges. Automotive manufacturers
now have a wide variety of choices available,
ranging from various grades of steel and alu-
minum to the most advanced lightweight com-
posite materials (Fig. 1).
The Center for Automotive Research
(CAR) created the Coalition for Automotive
Lightweighting (CALM) to support collabora-
tive efforts of auto manufacturers and suppli-
ers to integrate mixed materials for mass
reduction. Key issues addressed by CALM in-
clude identifying lightweighting technology im-
plementation constraints, supply chain and
economic issues, engineering decision analysis,
and cost/benefit methodologies.
A mixed materials environment requires
understanding the limitations and advantages
of specific materials and the methods available
to join them, according to Jay Baron, president
of CAR.
Metals remain material of choice
Automotive steels, aluminum, and magne-
sium alloys provide high strength and have a
well developed supply chain supporting quality
and manufacturability. For the past century,
steel and, more recently, alloys have been the
automotive materials of choice. Steels are typi-
cally bonded with welds that can cost about
5 cents each. With roughly 4000 required per
automobile, welds add hundreds of dollars in
cost to the manufacturing process, says Baron,
although they are very lightweight.
Earlier this year, Alcoa announced comple-
tion of a $300 million expansion at its Daven-
port, Iowa, facility dedicated to supplying
aluminum sheet products to the automotive in-
dustry. As an example of aluminum’s growing
share of the automotive market, Ford Motor
Co. announced that the body of the 2015 F-150
pickup truck will be comprised entirely of alu-
minum (Fig. 2). Ford expects to produce about
650,000 of the trucks next year. In the UK,
Jaguar Land Rover’s lightweight strategy for the
Range Rover L405 involves an all-aluminum
monocoque body.
According to automakers, demand for alu-
minum—already the material of choice behind
steel for passenger vehicle manufacturing—is
expected to nearly double by 2025. More specif-
ically, the amount of aluminum body sheet con-
tent in North American vehicles is expected to
quadruple by 2015 and increase tenfold by 2025
compared to 2012 levels. Aluminum is attractive
for its lighter weight as well as enabling complex
geometries in cases where the formability of
steel has been prohibitive. Aluminum has also
played an integral role in enabling part integra-
tion for cost reduction initiatives.
Despite its advantages, Al is not an ideal
material for welding, says Baron, and automak-
ers prefer redundancy in fastening solutions.
Aluminum use requires new joining techniques
including self-piercing rivets and adhesives. For
example, each Range Rover body uses 187 yards
of adhesive. Alcoa’s pretreatment bonding tech-
nology, known as Alcoa 951, enables more
durable bonding of aluminum components in
vehicles, can reduce spot weld points, and also
reduces manufacturing costs.
CFRPs for the future
Composites are following the classic adop-
tion curve within the automotive industry.
BMW’s i3 electric vehicle is the first of its kind, featuring a passenger cell
comprised entirely of carbon fiber-based composites. The drive module is
aluminum and must be joined to the passenger cell using specialized adhesives.
Courtesy of BMW AG.