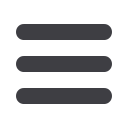
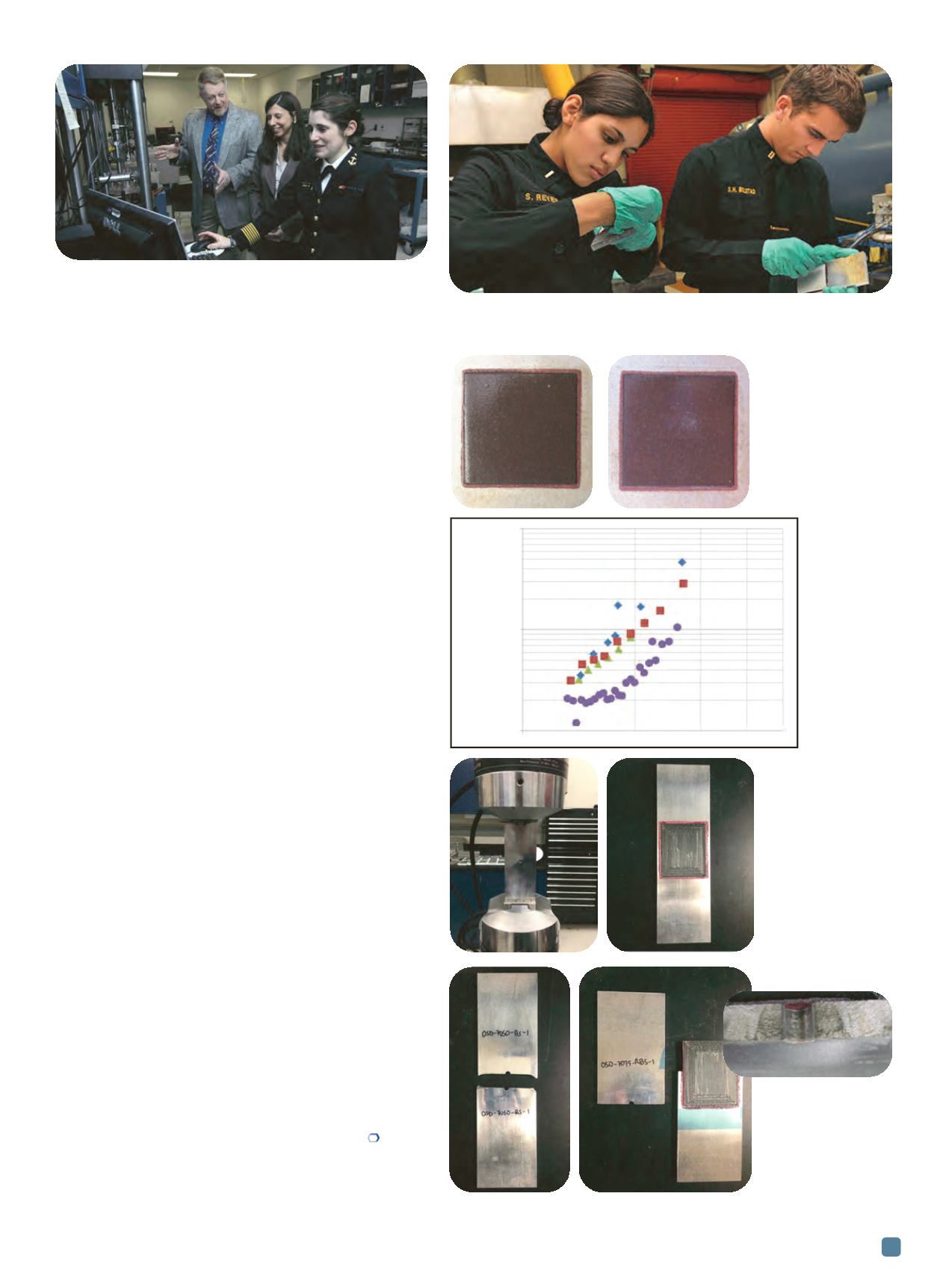
DoDNews
(Fig. 3) displaying their ongoing corrosion fatigue
research on composite repairs of aluminum alloys for aero-
space and naval ship applications. These experiments con-
tinue Schubbe’s work with boron-epoxy repairs and expand
the research into four different alloy systems and two com-
posite repair applications. Preliminary experiments in 2013
showed a significant increase in fatigue rates of cracks in
corrosion-resistant aluminum alloys when simulated seawa-
ter was applied to the repair area. In addition, durability test-
ing was done through the Naval Research Laboratory’s Key
West facility, coordinated by Robert Bayles and Sean Olig, to
examine repair bonds over time and when subjected to sea-
water immersion. Only minor bonding degradation was ob-
served due to some biofouling of the repair systems.
Seawater exposure to these repair systems was tested on
cracked and repaired specimens of 7050, 7075, 6061, and
5083 aluminums; data is now being reviewed.
Standard flat aluminum specimens with an electro-dis-
charge machined (EDM) pre-notched center hole were
tested. Specimens were pre-cracked to a specified length
then repaired using one of two composite combinations.
Boron-epoxy with AF-163-2 adhesive or graphite-epoxy
with an electrically insulative fiberglass layer was applied
and cured at elevated temperature and vacuum bagged to
simulate a field repair scenario. Specimens were then sub-
jected to tension-compression sinusoidal fatigue loading
at R = -0.3 to grow the crack in either ambient lab air or
subjected to a saltwater solution simulating seawater in the
crack damage. Results were promising, showing the
patches extend life. However, some indications still show a
negative effect from a potential galvanic couple between
the graphite patch and the aluminums.
Preliminary results were presented at the USNA Stu-
dent Research Fair on May 1 and final results will be pre-
sented at the TCC (Technical Corrosion Collaboration –
OSD) Program Review meeting in August at The Univer-
sity of Akron. One of the goals of the TCC is to enhance the
education of potential DoD employees in the area of cor-
rosion and expand the workforce involved in repairing
aging systems for the nation’s naval forces.
The USNA program continues to grow and attract inter-
ested students with the help of the TCC and other naval or-
ganizations. The ultimate goal is to expand awareness relative
to corrosion and corrosion-related material degradation, its
effects on force readiness, and efforts to manage it.
For more information:
Joel J. Schubbe is an associate profes-
sor at the U.S. Naval Academy, 590 Holloway Rd., Annapolis,
MD 21402, 410.293.6426,
schubbe@usna.edu,
usna.edu.
ADVANCED MATERIALS & PROCESSES •
JUNE 2014
27
Fig. 2
—
Trident Scholar and former Brigade Commander
Jennifer Jones demonstrates strain rate testing to her mentors.
Fig. 3
—
MIDN Sabrina Reyes and Scott Bolstad conduct corrosion fatigue
research on composite repairs of aluminum alloys for aerospace and naval
ship applications. Courtesy of CorrDefense DoD News.
Fig. 4
—
Corrosion
test samples from
the Key West NRL
facility.
1.0E-0.5
1.0E-0.6
1.0E-0.7
Crack growth rate, m/cycle
Fig. 5
—
Research
results.
Fig. 6
—
U.S. Naval
Academy testing of
composite repair for
corrosion fatigue.
Fig. 7
—
Exposed failed test specimens.