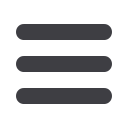
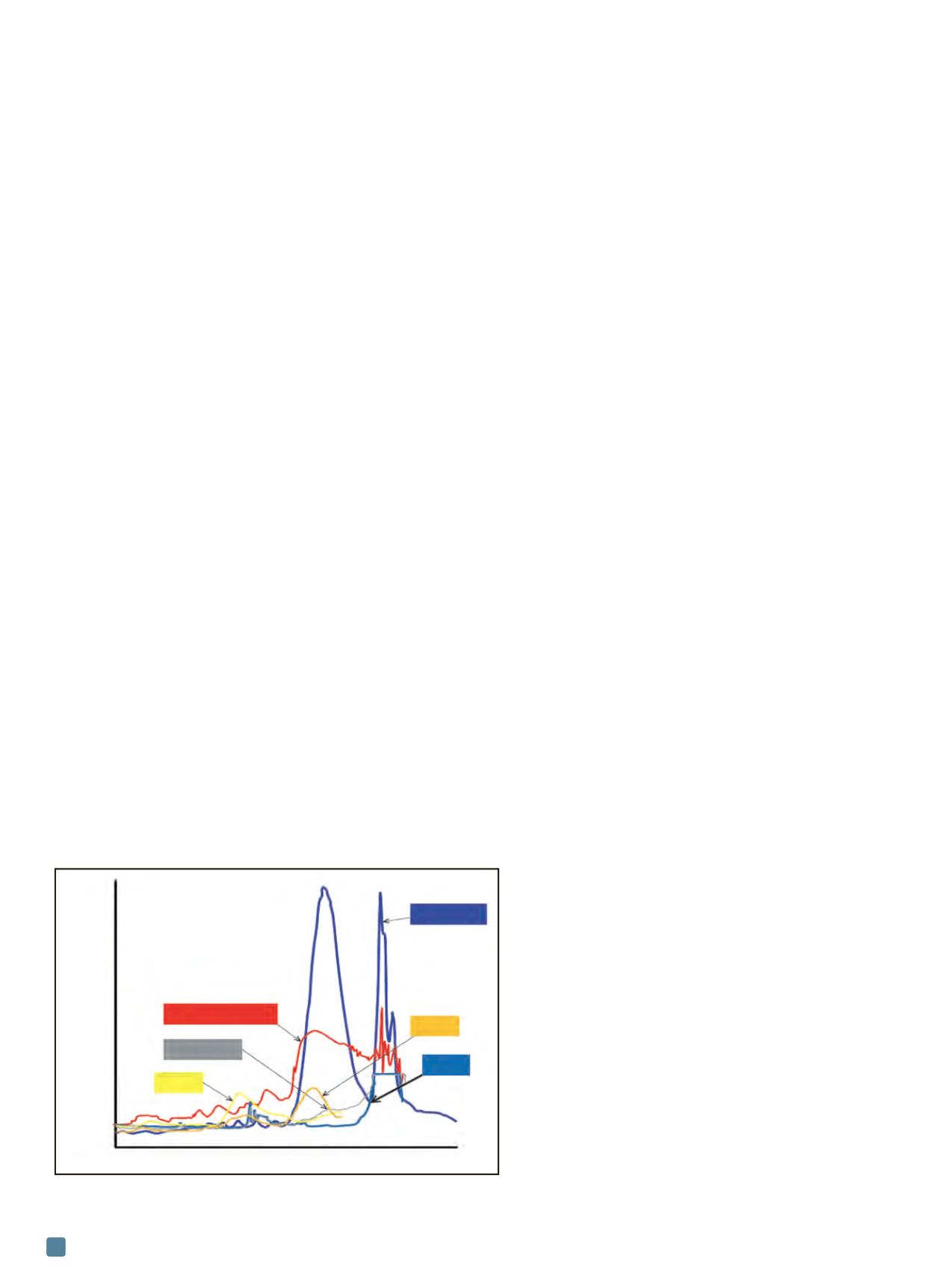
A
ccurate multi-component thickness and moisture
data is critical to the productivity and efficiency of
producers of plastic films, extrusion coatings,
blown films, and nonwoven fabrics. Collecting this data on
production lines in real-time ensures that raw materials
are not wasted and that all products meet relevant specifi-
cations. This becomes even more important as polymer
material costs rise. Several different noncontact online
analysis techniques exist, which primarily measure thick-
ness by passing either nuclear or electromagnetic radiation
through the web and measuring its absorption patterns via
a detector on the other side of the material.
Nuclear web gauging instruments are some of the ear-
liest online measurement technologies. Using sources like
Krypton 85 and Promethium 147 to emit a directed beam
of particles at test materials, these instruments can pro-
vide valuable and accurate thickness data but are limited in
measurement capabilities and cost. In addition to obtain-
ing a regulatory license to operate and incurring mainte-
nance costs associated with replacing the source, users of
nuclear web gauging instruments often need to hire a ra-
diation safety officer and submit to annual inspections. De-
pending on the country where the instrument is operated,
users may be subject to additional regulatory and licens-
ing requirements.
Infrared (IR) instruments avoid these burdens by using
infrared light to measure layer thickness. Because every
component in a multilayer web has a specific pattern of in-
frared absorption unique to its chemical structure, web
composition, multilayer thickness data, moisture, and
other parameters can be found by measuring the absorp-
tion and reflection of a light source through a multilayer
web. Two primary types of IR web gauging sensors exist:
Spinning filter wheel and solid-state full spectrum.
Spinning filter wheel sensors
The spinning filter wheel offers the simplest design,
which determines moving web thickness using a ratiomet-
ric measurement technique that compares two IR absorp-
tion readings. These readings are taken through two
different light filters, attached to a spinning wheel posi-
tioned near the web. The first filter is called the reference
filter (R) and it selects a wavelength with very low absorp-
tion for the analyzed material. The second filter is known
as the measurement filter (A) and uses a high absorption
wavelength. After readings are taken, the A/R ratio pro-
vides a result proportional to web thickness.
Spinning filter wheel sensors present several challenges.
Because each material in a multilayer web has its own ab-
sorption pattern, these sensors cannot measure multiple
materials simultaneously without additional A and R filters.
These filters increase upfront instrument costs, require
more maintenance, and compound the risk of failure. Addi-
tionally, any changes to the composition of the web being
measured require new filters. Spinning filter wheels require
a finite amount of time to rotate, so measurements suffer
from spatial displacements between readings. Further, each
filter measures a slightly different spot on the web, making
precise measurements difficult. While design improvements
have incrementally increased filter wheel speed over time,
they are unable to overcome this limitation.
Spatial displacement and the limited number of wave-
lengths measured by filter wheel sensors also make them
prone to error in certain circumstances. Moving webs that
include printed substrates, pigmentation, or nonuniform
base substrates have different absorption patterns than
those that do not, especially when variations are not uni-
form across the entire web (i.e., printed text and paper
board). Sheet flutter can also cause errors, as it can alter
absorption for one or both of the A and R readings. The
same is true for varying light conditions in the area sur-
rounding the instrument.
Solid state full spectrum sensors
Full spectrum IR web gauging instruments were devel-
oped to overcome the regulatory and technical issues of
nuclear and spinning filter wheel IR sensors. Unlike spin-
ning filter wheel sensors, which use only one wavelength of
IR light per filter at a time to take measurements, full spec-
trum IR instruments emit the entire spectrum of near in-
frared (NIR) light and take absorption measurements for
all wavelengths simultaneously. These instruments are able
to continuously measure the complete absorption pattern
of a given material rather than just a single wavelength.
Full Spectrum IR sampling eliminates many of the
problems that come with filter wheel IR web gauging sen-
sors. Because the entire NIR spectrum is sampled simulta-
neously, inaccuracies caused by spatial displacement are
Full Spectrum Infrared Light Analysis
Enhances Web Gauging Applications
ADVANCED MATERIALS & PROCESSES •
JUNE 2014
28
TECHNICAL SPOTLIGHT
Fig. 1
—
Full spectrum absorption patterns for common web materials,
taken using the Thermo Scientific PROSIS sensor.
2.5
2.0
1.5
1.0
0.5
0.0
IR Absorbance
EVOH
Cellulose
PET
Surlyn
PE
PP
Wavelength