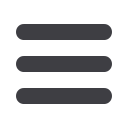
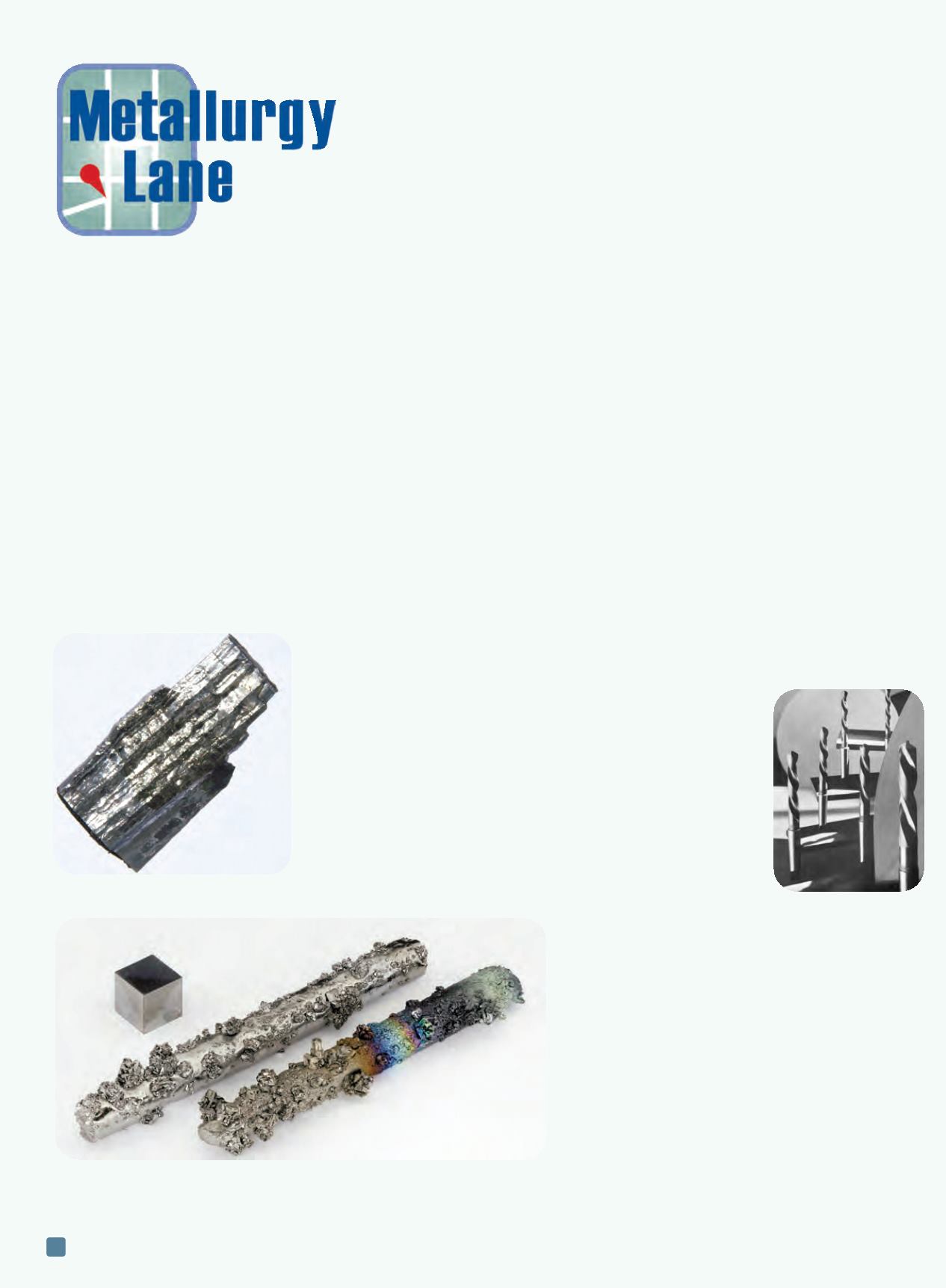
ADVANCED MATERIALS & PROCESSES •
JUNE 2014
32
A
shortage of tungsten during World War I
forced many high-speed steel users to fall
back to carbon steel, a 50-year technology
regression. After the war, a major research effort in
high-speed steels at Watertown Arsenal, Mass.,
looked at substituting molybdenum—tungsten’s
sister metal—in J.A. Mathews’ successful T-1
alloy. This work was done during the late 1920s
and early 1930s, and substituted approximately
9.5% Mo for the 18% W in the T-1 alloy—a
roughly 1:1 atomic replacement. Major accom-
plishments included using a borax coating during
heat treating to protect the surface and incorpo-
rating molten salt baths to heat the steel during
hardening. A significant drawback of all previous
high-molybdenum tool steels was the excessive
loss of surface carbon during heating.
It was widely known that large
deposits of Mo were present in the
Colorado Rocky Mountains. Within
a few years, consumption rapidly in-
creased partially due to the growing
adoption of Mo in engineering alloy
steels. With increased supply from
the Climax Molybdenum Co., the
price finally became competitive
with tungsten for use in high-speed
steel. Price alone, however, was not
the main driver for replacing W
with Mo: Technical acceptance in
the industrial marketplace among
tens of thousands of tool makers,
tool room foremen, and machinists was the final
hurdle. The Watertown Arsenal work was interest-
ing, and many applications were discovered for the
new tungsten-free, molybdenum high-speed steel
within various arsenals around the country. How-
ever, it never gained acceptance in industry as a
T-1 competitor.
Major breakthrough
The first significant breakthrough regarding
commercial development of Mo high-speed steels
was discovered by Joseph V. Emmons at the Cleve-
land Twist Drill Co. In 1933, he received his patent
and published a technical paper in which he briefly
reported that all-molybdenum steels (tungsten-free)
were inferior to T-1. Emmons also pointed out that
substituting small amounts of Mo for some of theW
was not worthwhile. His major discovery was that a
Mo-W ratio of roughly 4:1, for a total of 10% of the
steel, offered a critical composition that could com-
pete against T-1’s 18% tung-
sten recipe. His paper,
“Some Molybdenum High
Speed Steels,” won the cov-
eted Henry Marion Howe
Medal in 1933, an annual
award still presented by
ASM International.
Cleveland Twist Drill
significantly boosted the
manufacture of Mo high-
speed steel by ordering
more than $1,000,000
worth, based solely on con-
fidence in Emmons and his
15-year quest for the best
T-1 replacement. Many modern high-speed steel
compositions still fall under various patents issued
to Emmons.
Industrial practices, however, die hard and at
the time of America’s entry into World War II,
more than 80% of high-speed steels were still of the
tungsten type. The War Production Board pro-
vided encouragement for the massive technological
shift to molybdenum by denying the tool steel in-
dustry the tungsten it required to maintain produc-
tion. Thus, Mo high-speed steels became the
dominant type during World War II and beyond.
Metallurgy Lane,
authored by
ASM life member
Charles R. Simcoe
,
is a yearlong series
dedicated to the early
history of the U.S. metals
and materials industries
along with key
milestones and
developments.
The Toolmakers: Part II
Modern society has evolved and progressed in no small part
due to the availability of cutting tools made of high-speed steel.
99.99% pure molybdenum crystal.
Courtesy of Jurii/Wikimedia Commons.
99.98% pure tungsten rods with evaporated crystals, partially oxidized with colorful
tarnish; high-purity tungsten cube for comparison. Courtesy of Alchemy-hp/
Wikimedia Commons.
Beautiful bits from
Cleveland Twist Drill
Co., circa 1933, the
first company to
commit to Mo
high-speed steel.