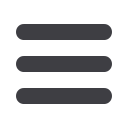
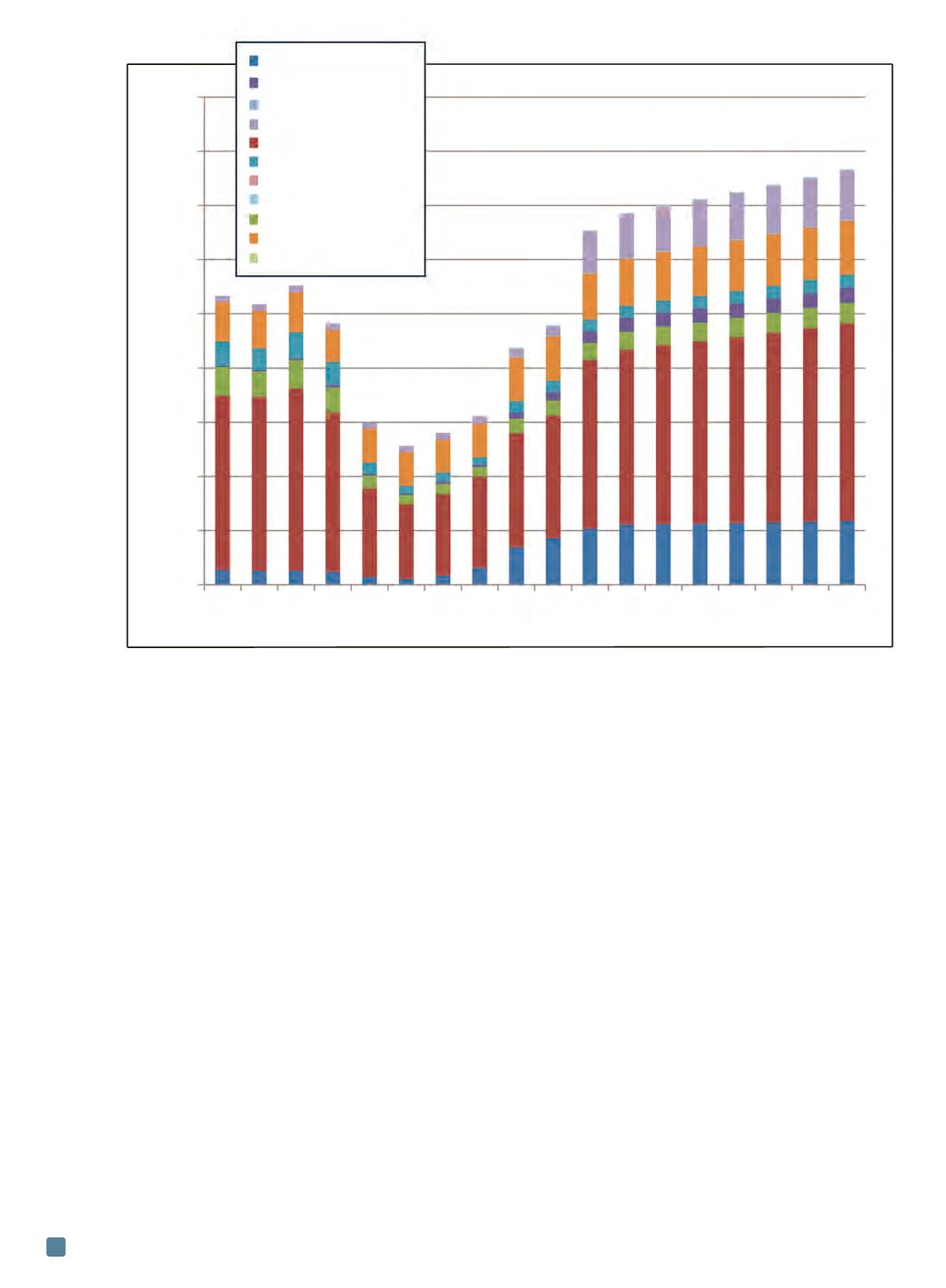
ADVANCED MATERIALS & PROCESSES •
JUNE 2014
24
Adhesive quality control begins with the supply
chain, emphasizes Baron. Adhesive properties need to
be standardized to ensure consistency and integrity in
the bonding process. Testing of joints between materi-
als usually requires destructive testing and knowledge
of mechanical engineering. As new adhesives are devel-
oped, quality control will require greater knowledge of
chemical engineering.
Assessing the properties of materials on an individ-
ual basis—as well as collective performance within a joined
system—supports the realization of design goals. With ma-
terials selection processes complete, manufacturers must
then assess the quality of inbound products from suppliers
as well as performance of components in joined systems.
The capability to accurately determine crucial properties,
such as percent elongation at failure, modulus, shear
strength, and flexure in a manner that supports high
throughput is paramount. Materials testing equipment has
traditionally been used to evaluate small samples. As qual-
ity assurance moves from the lab to the manufacturing
floor, capacity to handle high volume is the key to large
scale implementation of quality testing.
Solutions for mixed materials strategies
One company making headway in mixed materials
qualification is Zwick/Roell, a testing equipment supplier
based in Germany. The company has developed solutions
that support both R&D (materials selection and design val-
idation) and quality control testing applications for
aluminum/aluminum alloys and composites. Its new-
generation Allround-Line testing system is well suited to
the high throughput test environment mandated by both
materials selection routines and quality management
processes for lightweighting initiatives (Fig. 5). Rapid test
and positioning speeds, coupled with fast return, reduce
cycle times for testing. Intelligent features such as inte-
grated adaptive control with automatic setting of all con-
trol parameters, sophisticated strain-rate control, and
online compensation for changes in specimen properties
enable lab managers to spend more time focusing on re-
sults analysis than test setup. For example, applications
such as buckling tests on lightweight vehicle door compo-
nents demonstrate the flexibility of the new system.
“The Allround-Line systems contain dual testing areas
that minimize changeover time between tests and deliver
the flexibility that R&D labs require, as well as the through-
put that quality control environments demand,” says Hel-
mut Fahrenholz, composites industry manager for Zwick.
Composite testing challenges
Composites are anisotropic and therefore present chal-
lenges. In addition, the properties of fiber-reinforced com-
posites greatly depend on fiber and matrix materials,
alignment of fibers, and the fiber-matrix interface. Materi-
Fig. 4
—
Advanced composite component unit production forecast by application category. Courtesy of Composites Forecasts and
Consulting LLC.
Chassis
Interior – cosmetic
Engine bay – cosmetic
Brakes
Body
Suspension
Emissions/exhaust
Other
Interior – structural
Engine/drive train
Fuel system
Advanced Composite Component Unit Production
Forecast by Application Category
4,500,000
4,000,000
3,500,000
3,000,000
2,500,000
2,000,000
1,500,000
1,000,000
500,000
0
2005
2006
2007
2008
2009
2010
2011
2012
2013
2014
2015
2016
2017
2018
2019
2020
2021
2022