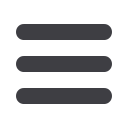
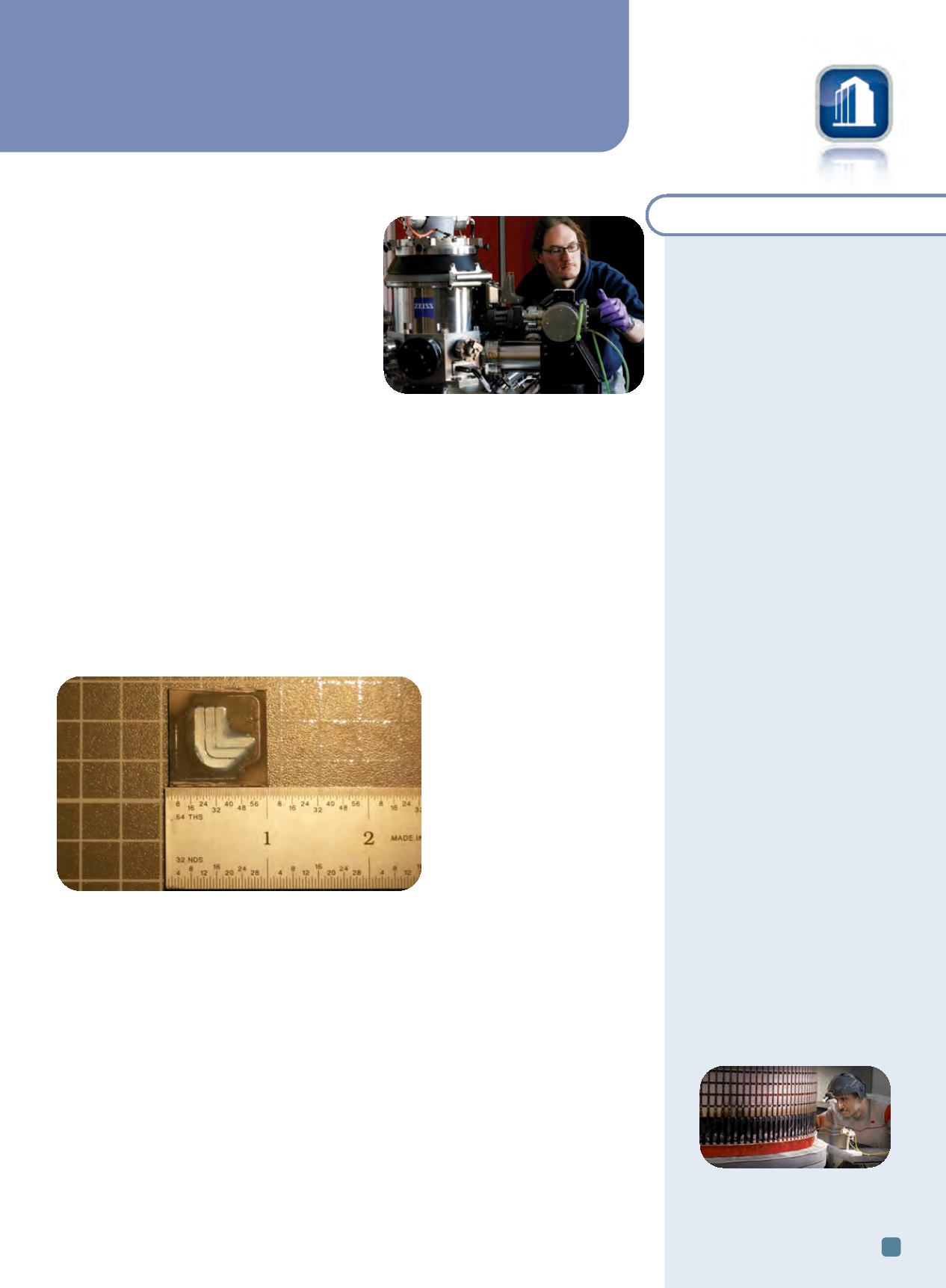
ADVANCED MATERIALS & PROCESSES •
JUNE 2014
13
news
industry
briefs
Proto Labs Inc.,
Maple Plain,
Minn., acquired
FineLine
Prototyping Inc.,
Raleigh, N.C.
Proto Labs uses CNC machining
and injection molding to
manufacture custom parts.
FineLine provides high-quality
stereolithography, selective laser
sintering, and direct metal laser
sintering services to a variety of
industries, such as medical,
aerospace, computer/electronics,
consumer products, and industrial
machinery.
protolabs.com.
SQuAD Forging
installed a
10,000-ton-capacity aerospace
hydraulic forging press at its
manufacturing facility in Aequs
SEZ (special economic zone),
Belgaum, India. The closed die,
hydraulically operated hot forging
press is reportedly the largest of
its kind in India and will be used to
forge large airplane components
and parts such as landing gears
and various actuation and
structural parts. The new press,
expected to begin production by
September, can forge aluminum,
steel, and titanium parts up to
400 kg.
squadforge.com.
Power generation and distribution
firm
ABB Ltd.,
Zurich, recently
installed the largest single-shot
short-circuit ring brazing system
developed by
EFD Induction Inc.,
Madison Heights, Mich. The
system, installed at the Italian ABB
plant outside Milan can braze rings
with diameters to 1500 mm. The
system is comprised of
customized coils, an EFD Induction
Sinac 250/320 power source, and
mounting table. The first project
involved brazing a 1500-mm-
diameter short-circuit ring for a
wind tunnel motor.
efd-induction.com.
An ABB technician uses the new
EFD system to heat a
short-circuit ring.
P
ROCESS
T
ECHNOLOGY
Newmethod makes ample amounts of high quality graphene
Researchers at AMBER (Advanced Materi-
als and BioEngineering Research), the materials
science center headquartered at Trinity College
Dublin, developed a new method of producing
industrial quantities of high-quality graphene,
which was previously impossible.
The subject of ongoing international re-
search, the AMBER discovery is said to be the
first to perfect large-scale production of pristine
graphene materials. Jonathan Coleman, profes-
sor of chemical physics at Trinity College and
AMBER, and his team used a simple method to
transform flakes of graphite into defect-free
graphene using commercially available tools, such as high-shear mixers. They demon-
strated that not only could graphene-containing liquids be produced in standard lab-scale
quantities of a few hundred ml, but also that the process could be scaled up to produce
hundreds of liters and more.
www.ambercentre.ie.
Additive manufacturing approach uses light to form composites
For almost 100 years, electrophoretic deposition (EPD) has been used as a method to
coat materials by depositing particles of various substances onto the surfaces of manufac-
tured items. EPD is most commonly used to apply primer to new car bodies on assembly
lines. The car’s body is positively charged while the liquid primer in the dunk tank is neg-
atively charged, forcing the primer to attract to the metal surface. In its traditional use,
EPD can only deposit mate-
rial across the entire surface
and not in specific, predeter-
mined locations, until now.
Researchers at Lawrence
Livermore National Labora-
tory (LLNL), Calif., created
a technique called light-
directed electrophoretic
deposition, which uses pho-
toconductive electrodes and
dc electrical fields to dynam-
ically pattern the surface
material. This allows the
material to build up in
targeted areas where the light contacts the photoconductor’s surface, enabling
arbitrarily patterned, 3D multimaterial composites to be created over large areas with
fine resolution.
Light-directed EPD was used to produce an alumina ceramic-tungsten nanoparticle
composite. Initially, the tungsten nanoparticles were deposited across the photoconductive
surface then illuminated through a laser-cut aluminum mask. A differently shaped mask
was substituted along with the new material to deposit the ceramic material. In the future,
aluminum masks will be replaced by digitally projected ones for a completely automated
deposition system.
Light-directed electrophoretic deposition has the potential to elevate traditional EPD
from a single layer, single material coating process to a true additive manufacturing tech-
nique that allows unique composites to be formed. For example, void areas can be pre-
cisely created in a part to control polymer material behaviors for energy absorption or
within cellular material to create veins or blood vessels for manufactured organs.
llnl.gov.A team led by Jonathan Coleman
discovered a new method to produce
large volumes of high-quality graphene.
Proof-of-concept logo 3D printed using a new additive
manufacturing process, light-directed electrophoretic
deposition (EPD). Courtesy of LLNL.