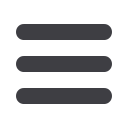
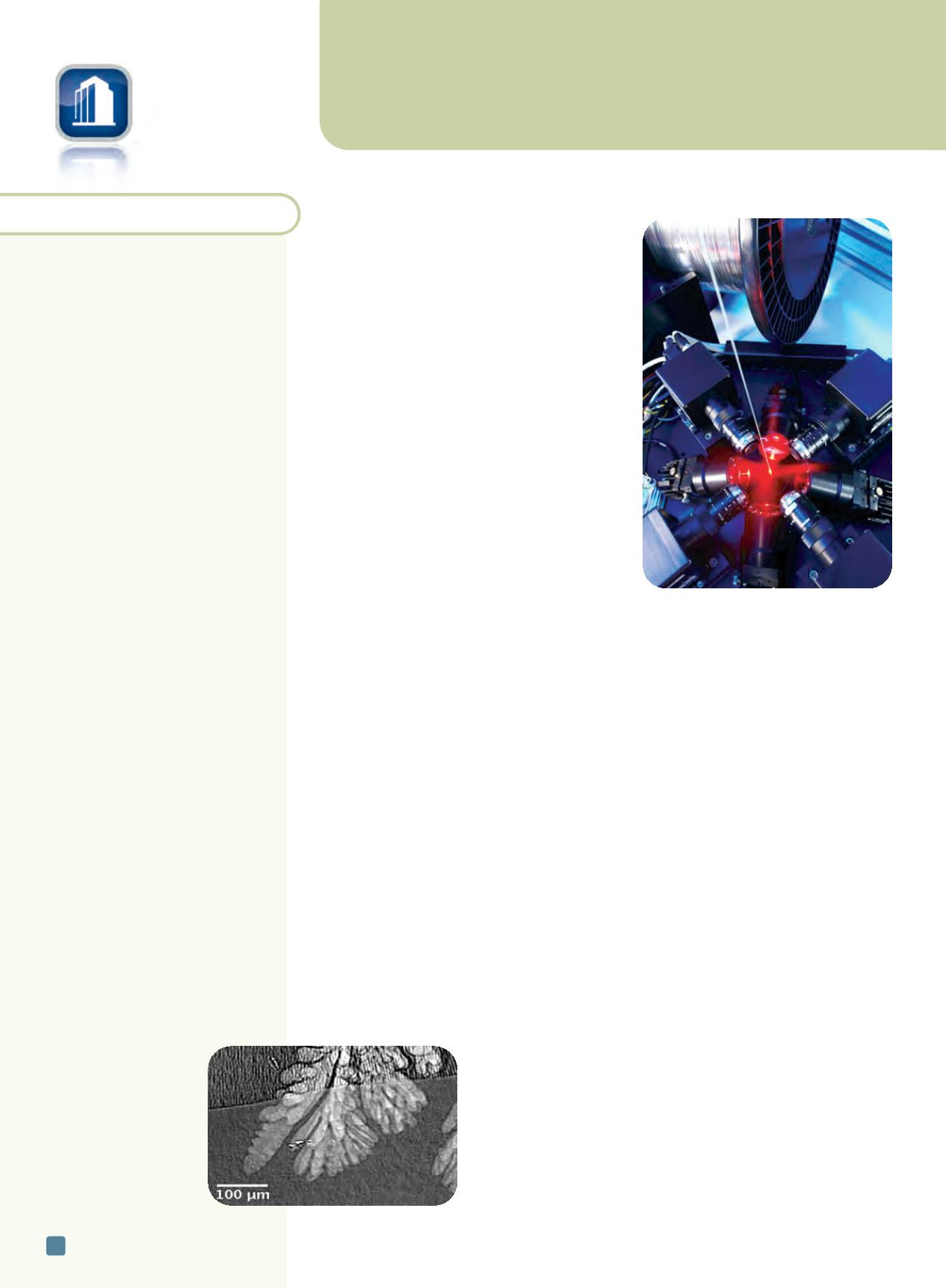
Optical inspection system enables rapid in-line inspection
Researchers at Fraunhofer Institute for Phys-
ical Measurement Techniques IPM, Freiburg,
Germany, achieved in-line inspection at ex-
tremely high production speeds. Their optical in-
spection system, WIRE-AOI, can detect defects
in strip products such as pipes, rails, wires, and
boards in real-time. The inspection system de-
tects micro-defects that zoom past at 10 m/s and
are no thicker than a human hair. Workers see
the processed defects depicted on a monitor and
can remove corresponding pieces.
The defect location is marked and the asso-
ciated camera image is stored in a database, en-
abling strip product manufacturers to identify,
classify, and document defects during produc-
tion. If a workpiece exceeds predefined param-
eters, a visible and audible alarm is activated.
Four high-speed cameras deliver images of de-
fects, with each camera capable of shooting
10,000 images per second and processing them
in real-time.
“Only a handful of models for industrial cam-
era inspection are able to record this number of
images in the first place, much less analyze them
in real-time,” says Daniel Carl, group manager for Inline Measurement Techniques at IPM.
Prerequisite for this peak performance are cellular neuronal networks. “That means each
pixel is itself a computer in its own right. In order to program these, you need specialized
knowledge about parallel architectures that the team at IPM has at its disposal.”
Corresponding software must first enable the system to analyze the images shot by the
camera. An LED light developed by the teammakes the images super-sharp. Its light shines
at 5 millionths of a second, as bright as 100 suns, and flashes 10,000 times per second. An-
other feature is sturdy housing, as the process can get rough when making strip products.
For example, in wire production, blanks are either rolled or drawn through dies, which can
get messy or experience extreme vibration. The inspection system—with its sensitive elec-
tronic and optical components—is in the middle of the production line and workpieces
travel directly through it.
For more information: Daniel Carl, 49.761.885.7549,
daniel.carl@ipm.fraunhofer.de,
www.ipm.fraunhofer.de.
Nondestructive imaging sheds light on metal solidification
Los Alamos researchers and collaborators are using nondestructive imaging techniques
to study solidification of metal alloy samples. The team used complementary methods of
proton radiography at the Los Alamos Neutron Science Center (LANSCE), N.M., and syn-
chrotron x-ray radiography at Argonne National Laboratory (ANL), Lemont, Ill., to make
the measurements. This is the first time high-energy protons were used to nondestruc-
tively image a large metal sample during melting and solidifica-
tion. Such real-time imaging could provide the insight needed to
control metal microstructure and lead to advanced manufactur-
ing processes to produce materials with desired properties.
Scientists can peer into a metal during processing without
destroying it using high energy proton radiography (pRad) and
synchrotron x-ray radiography. Amy Clarke of Metallurgy (MST-
6) led a team that demonstrated the ability to use pRad imaging
to examine large volumes (greater than 10,000 mm
3
) of metallic
briefs
Element Materials Technology,
St. Paul, Minn., opened a new
state-of-the-art laboratory in
Plymouth, Mich. The company’s
42nd location worldwide, the
facility will serve the automotive
industry, providing materials and
component testing, and product
qualification testing to the
transportation and industrial
markets, including automotive
manufacturers and their suppliers.
Services include environmental,
vibration, and interior testing,
including component durability and
airbag deployment.
element.com.
MTI Instruments Inc.,
Albany,
N.Y., received ISO 9001:2008
quality management certification,
authorized by
TÜV Rheinland,
a
global provider of independent
testing and certification services.
MTI manufactures noncontact
measurement systems and
sensors including computerized
general gauging instruments for
position, displacement, thickness,
and vibration applications using
laser, fiber optic, and capacitive
sensor measurement technologies.
mtiinstruments.com.
Renishaw plc,
UK, received a
Queen’s Award for Enterprise
2014
in the “Innovations” category
for its inVia Raman microscope.
The award was granted for
continuous development of the
inVia with ultra-fast Raman
imaging, which enables rapid
generation of high-definition 2D
and 3D chemical images for
material analysis. The microscopes
use Raman scattering to analyze
the chemical structure and
composition of materials.
renishaw.com.
ADVANCED MATERIALS & PROCESSES •
JUNE 2014
10
T
ESTING
C
HARACTERIZATION
news
industry
With the WIRE-AOI wire inspection
system, four cameras collectively deliver
40,000 analyzed images per second.
Courtesy of Fraunhofer IPM.
X-ray image of a 200-
micron thick Al-14 at.%
Cu alloy during
directional solidification,
highlighting growth of
an aluminum-rich
branched structure
(dendrite) and
advancing solid-liquid
(planar) interface.