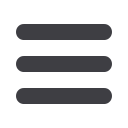
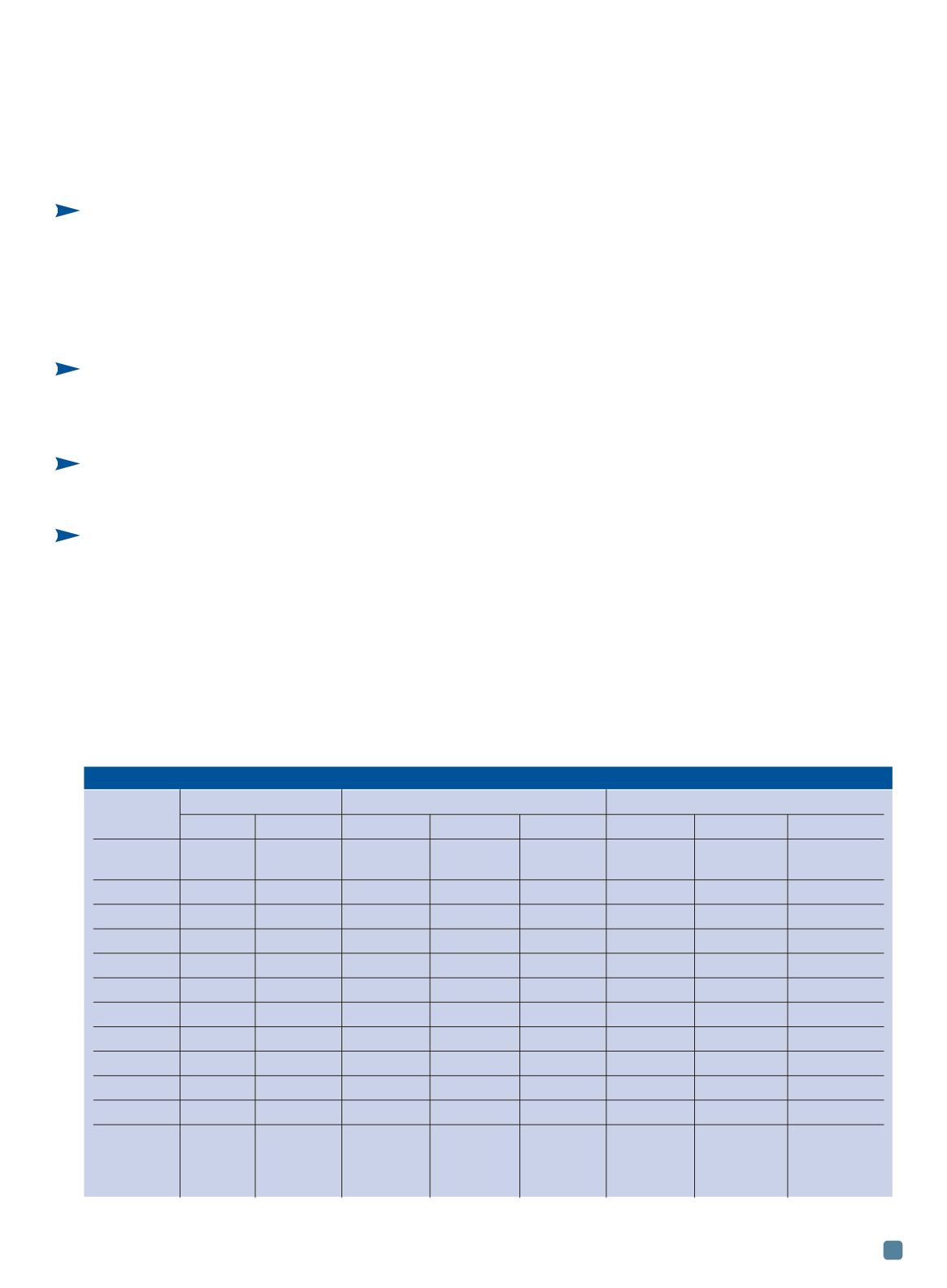
ADVANCED MATERIALS & PROCESSES •
JANUARY 2014
21
Development of Hardfacing Alloys
for Power Generation Applications
M
any issues exist concerning the spec-
ification, manufacturing, and use of
high-performance valves in the fossil
and nuclear power generation industries. In-
creased unit flexibility (cyclic operation),
higher-temperature operation (for higher effi-
ciency), and radiation exposure (nuclear power)
are key drivers for new opportunities in the de-
velopment of materials and manufacturing
processes for valve components. A recent arti-
cle in
AM&P
discussed the promise of powder
metallurgy and hot isostatic pressing (PM/HIP)
technology for ferritic and stainless steel com-
ponents production. This technology addresses
a wide range of issues regarding cast valve com-
ponents, including inspection, performance,
and supply chain pinch points such as procure-
ment, machining, and rework or refurbish-
ment, including weld repair
[1]
.
Ongoing research and development at the
Electric Power Research Institute (EPRI), de-
tailed in this article, examines the application
of wear-resistant hardfacing materials using the
PM/HIP process. The hope is to eliminate
weldability and residual stress challenges asso-
ciated with some of the hardfacing alloys, as
well as provide a wider range of potential alloy
solutions for two key concerns, detailed here.
Table 1 provides chemical compositions of the
materials discussed in this article.
A drive to eliminate cobalt from hardfaced
components such as valve seats, discs, and
stems remains in the nuclear power industry.
Hardfaced component wear during operation
may result in transporting Co to the reactor
where it is transformed into highly radioactive
Co
60
. This isotope has a half-life of more than
five years and is a major culprit in occupational
radiation exposure to plant personnel working
on valve components or near potential crud
trap sites during outages.
Delamination (also referred to as liberation
or disbonding) of hardfacing material from fer-
ritic valve seat and disc substrates results in col-
lateral damage to the steam turbine and valve
operational function(s) (i.e., failure). An exam-
ple of delamination hardfacing in a Grade 22
valve disc is shown in Fig. 1. This problem has
John Siefert*
David Gandy, FASM
Dan Purdy
John Shingledecker*
Electric Power
Research Institute,
Charlotte, N.C.
Ryan Smith
Tapasvi Lolla
The Ohio State
University, Columbus
Suresh Babu, FASM*
The University of
Tennessee, Knoxville
Lou Lherbier, FASM*
David Novotnak*
Carpenter Technology
Corp.
Reading, Pa.
Development of wear-resistant hardfacing materials using powder
metallurgy/hot isostatic pressing technology offers an alternative to today’s
cobalt-based materials and those that suffer delamination damage.
*Member of ASM International
TABLE 1 — MATERIAL CHEMICAL COMPOSITION
Hardfacing
Potential Butter Layers
Substrate Materials
Element
Alloy 6
Alloy 21 FM625
ER309
316L Grade 22 Grade 91
Industry
Nuclear
Nuclear
Fossil
Fossil
Fossil
Nuclear
Fossil
Fossil
and Fossil Candidate
C
0.9-1.4
2.5
0.20-0.35 0.10 max 0.04-0.12 0.030 max 0.05-0.15 0.07-0.14
Ni
— — 2.0-3.0 58.0 min
12-14
10-14
— 0.40 max
Cr
27-32
25
26-29
20-23
23-24
16-18
1.9-2.6
8.0-9.5
Fe
— Bal.
— 1.0 max
Bal.
Bal.
Bal.
Bal.
Mo
— 3.2
4.5-6.0 8.0-10.0 0.3 max
2-3
0.87-1.13 0.85-1.05
Mn
— ≤1.0
— 0.50 max
1.0-2.5
2 max
0.30-0.60
0.30-0.60
Si
— ≤0.5
— 0.50 max
0.30-0.65
1 max
0.5 max
0.20-0.50
P
— — — 0.02 max
0.030 max 0.045 max 0.025 max
0.020 max
S
— — — 0.015 max 0.020 max 0.030 max 0.025 max
0.010 max
Co
Bal.
— Bal.
Bal.*
— — —
—
Others
W: 4.0-6.0 V: 0.5
— Nb: 3.15-4.15 — N: 0.10 max
— Nb: 0.06-0.10
Al: 0.40 max
V: 0.18-0.25
Ti: 0.40 max
Al: 0.020 max
Ti: 0.010 max
*Ni+Co