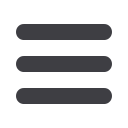
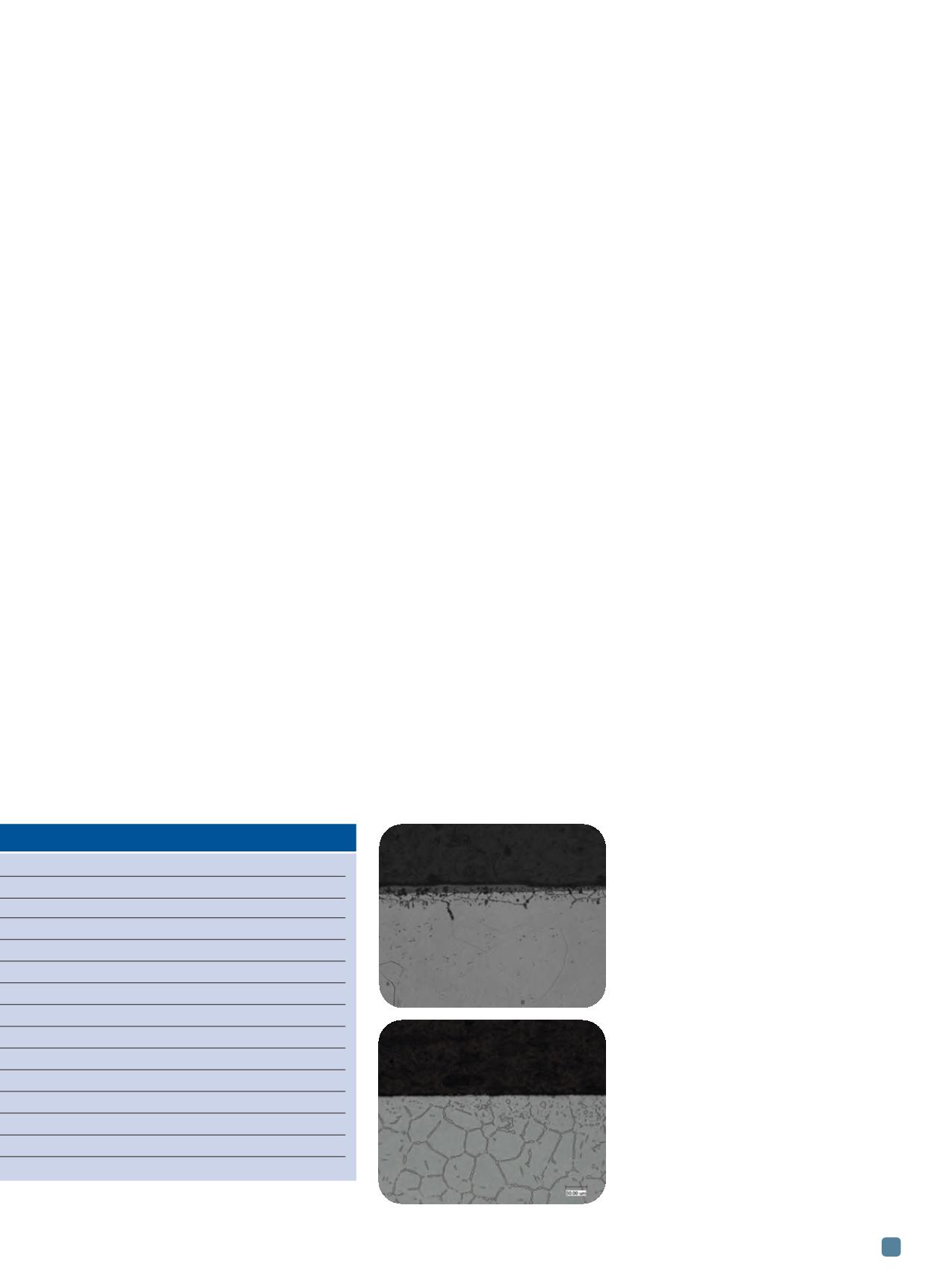
for corrosion control in liquid lead and LBE environments
Ferritic-martensitic (FM) steels such as HT9, which
have an extensive database of radiation damage, and T91,
which allows for higher operating temperatures, are being
considered for LFR cladding applications
[5]
. Typical oxide
layer structures developed on these steels in LBE comprise
an outer Fe
3
O
4
(magnetite) layer and inner spinel com-
pound ([Fe, Cr]
3
O
4
) layer. A notable advancement in FM
steels for LBE applications is EP-823, developed by Russian
programs. This steel contains Si (1-1.3%) resulting in an
SiO
2
surface layer that provides improved protection in
LBE environments. Ferritic oxide dispersion strengthened
(ODS) steels such as MA956 and PM2000 containing alu-
minum also perform well in LBE environments due to the
formation of a protective alumina film on the surface. Re-
fractory metals such as W, Mo, and Ta were tested with
promising results. Flow-assisted erosion and corrosion is
an important concern in LBE and can become quite dom-
inant at flow rates above roughly 2 m/s, depending on the
steel and the temperature
[4-6]
.
High temperature gas-cooled reactors
High temperature gas-cooled reactors (HTGR) are
being considered for electricity production and as a source
of by-product process heat for powering chemical plants.
Helium was chosen as the coolant gas due to its excellent
heat transfer characteristics. The reactor gas outlet tem-
peratures have not been fully established, but temperatures
of 850°C or higher are being targeted. While helium is
inert, long-term corrosion due to its impurities such as
methane, carbon monoxide, hydrogen, carbon dioxide, and
water is an important consideration. The most critical
metallic component in HTGR is the heat exchanger.
Two alloys being considered for this application are
Alloy 617 and Haynes 230. The environmental degrada-
tion of these alloys in a helium environment was investi-
gated in Japan and Germany in the 1980s and more
recently at CEA in France and Idaho National Laboratory
in the U.S.
[7-9]
Studies show that depending on the partial
pressure of these impurities and temperature, a variety of
surface reactions can occur including oxidation, carbur-
ization, and decarburization. Ideally, a protective oxide is
desirable, but this layer should not be destroyed by carbur-
ization or decarburization
[8]
. Examples of potential surface
reactions with alloys’ metallic constituents (M, reactions
listed below) include oxidation of metal by water or car-
bon monoxide, decarburization of surface by water, and re-
duction of protective surface oxide by methane
[9]
.
xH
2
O + M = MO
x
+ x/2H
2
xCO + M = MO
2x
+ C
H
2
O + C = CO
2
+ H
2
xCH
4
+ MO x = xCO
2
+ 2xH
2
+ M
Based on thermodynamic equilibrium considerations,
regimes of environmental interaction mechanisms were
mapped as a function of carbon activity and oxygen partial
pressure. The map (Fig. 3 for Alloy 617) provides a basis
for coolant chemistry control for mitigating corrosion
[7, 8]
.
The regimes include: I: strongly reducing, II: highly oxidiz-
ing, III: stable outer oxide and stable internal carbides, IV:
strongly carburizing internally and externally, IVa: strong
external carburization with stable oxide layer. Regime III
represents the highest environmental stability where a sta-
ble surface oxide protects the alloy surface and the me-
chanical integrity is maintained by stable carbides. Figure
4a and b show cross-sectional images of corrosion layers
in IN 617 after exposure at 1000°C under oxidizing and
carburizing conditions, respectively
[8]
.
Fluoride salt-cooled high temperature reactor
The high volumetric heat capacity of molten salts in gen-
eral has garnered considerable
interest for their use as a
coolant, heat transfer, and ther-
mal storage media in many en-
ergy-related applications. The
fluoride salt-cooled high tem-
perature reactors (FHR) use
molten fluoride salts as coolant.
These salts have a high boiling
point (alleviating concerns
about loss-of-coolant acci-
dents) and a high solubility for
ADVANCED MATERIALS & PROCESSES •
JANUARY 2014
19
Nb
Ti
Y
2
O
3
Co
— — — —
0.075
— — —
— — — —
— — 0.5
—
— — 0.5
—
— — — —
— — — —
— — — —
4.75-5.5 0.65-1.15 — <1.0
— — — —
0.8*
— — —
— 0.15-0.6
— —
— — — —
Fig. 4 —
Cross-sectional
images showing corrosion layers
in IN 617 after exposure at
1000°C for 500 hours (a) under
oxidizing conditions showing an
oxide layer and slight surface
decarburization, and (b) under
carburizing conditions showing
carbide phase formation at
grains and grain boundaries
[8]
.
(a)
(b)