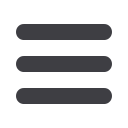
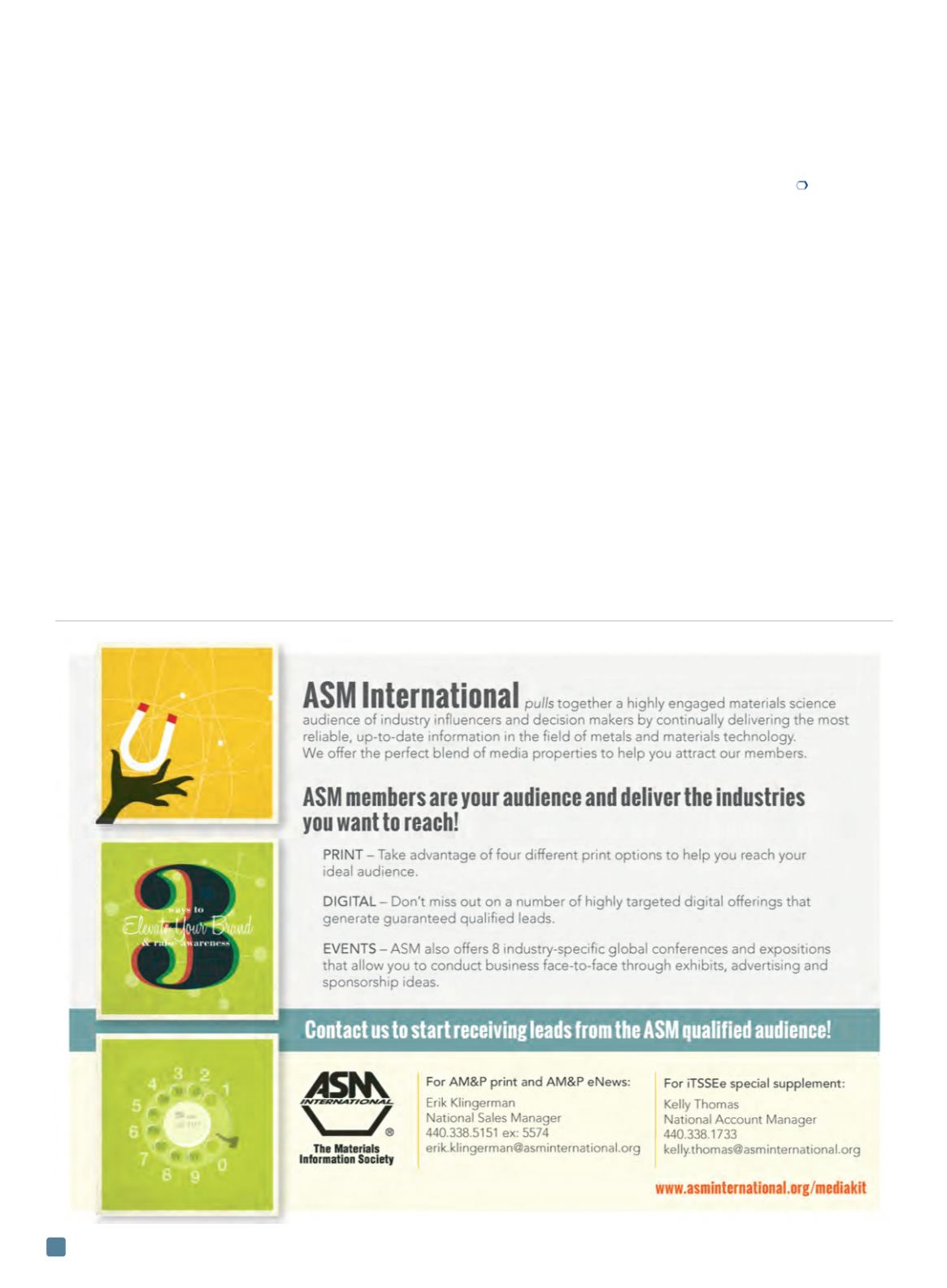
• Standard methods for examination of tested
specimens to ASTM G98 and ASTM G133 to
provide quantifiable results. A database of roughly
20 different materials including both commercially
available and developmental hardfacing alloys has
been assembled.
• Identification of multiple failure modes in cycling,
fossil-fired valve applications due to different material
combinations.
• Potential solutions to the selection of appropriate
butter layer(s) for use in cycling fossil applications
were identified using thermodynamic simulations.
Ongoing research provides intriguing results, which
may lead to identification of material(s) that will solve is-
sues across the nuclear and fossil industries. The promise
of PM/HIP has sparked intrigue in solving material incom-
patibility issues using a function graded composition con-
trolled (FGCC) methodology to layer or grade between two
materials. Further, the ability to deposit materials using this
manufacturing process allows optimization of wear behav-
ior as opposed to weldability, for example.
PM/HIP also provides an attractive alternative in the nu-
clear industry, where difficulties in welding previously devel-
oped replacement hardfacing materials (such as NOREM)
often result in continued use of the Co-based Alloy 6. In re-
sponse to the power industry’s critical need for improved
component life, EPRI research projects—from the funda-
mental science of wear and galling to practical issues of inves-
tigating failed service components—are being conducted to
provide both near- and long-term solutions.
For more information:
John Siefert is project manager, Elec-
tric Power Research Institute, 1300 West WT Harris Blvd.,
Charlotte, NC 28262, 704/595-2886,
jsiefert@epri.com,
www.epri.com.
References
1. D.W. Gandy, J.P. Shingledecker, and J.A. Siefert, Overcoming
Barriers for Using PM/HIP Technology to Manufacture Large
Power Generation Components,
Advanced Materials &
Processes,
Vol 170, No. 1, p 19-23.
2. ASTM Standard G98-02, 2009. Standard Test Method for
Galling Resistance of Materials, ASTM International, West Con-
shohocken, PA. DOI: 10.1520/G0098-02R09.
3. ASTM Standard G133-05, 2010. Standard Test Method for
Linearly Reciprocating Ball-on-Flat Sliding Wear, ASTM Inter-
national, West Conshohocken, PA. DOI: 10.1520/G0133-05R10.
4. Programon Technology Innovation: Galling and SlidingWear
Test Results for Candidate Hardfacing Alloys Manufactured by
PM/HIP. EPRI, Palo Alto, CA. 3002001737. 2013.
5. 3D Laser Scanning Microscope VK-X100/X200 Series: AMi-
croscope, SEM and Roughness Gauge in a Single Unit, Keyence
Corp. of America, p 27, 2011.
6. Programon Technology Innovation: Microstructural Charac-
terization of Cobalt-Free Hardfacing Alloys Subjected to Galling
Tests. EPRI, Palo Alto, CA. 3002001738. 2013.
ADVANCED MATERIALS & PROCESSES •
JANUARY 2014
24