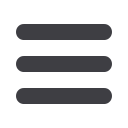
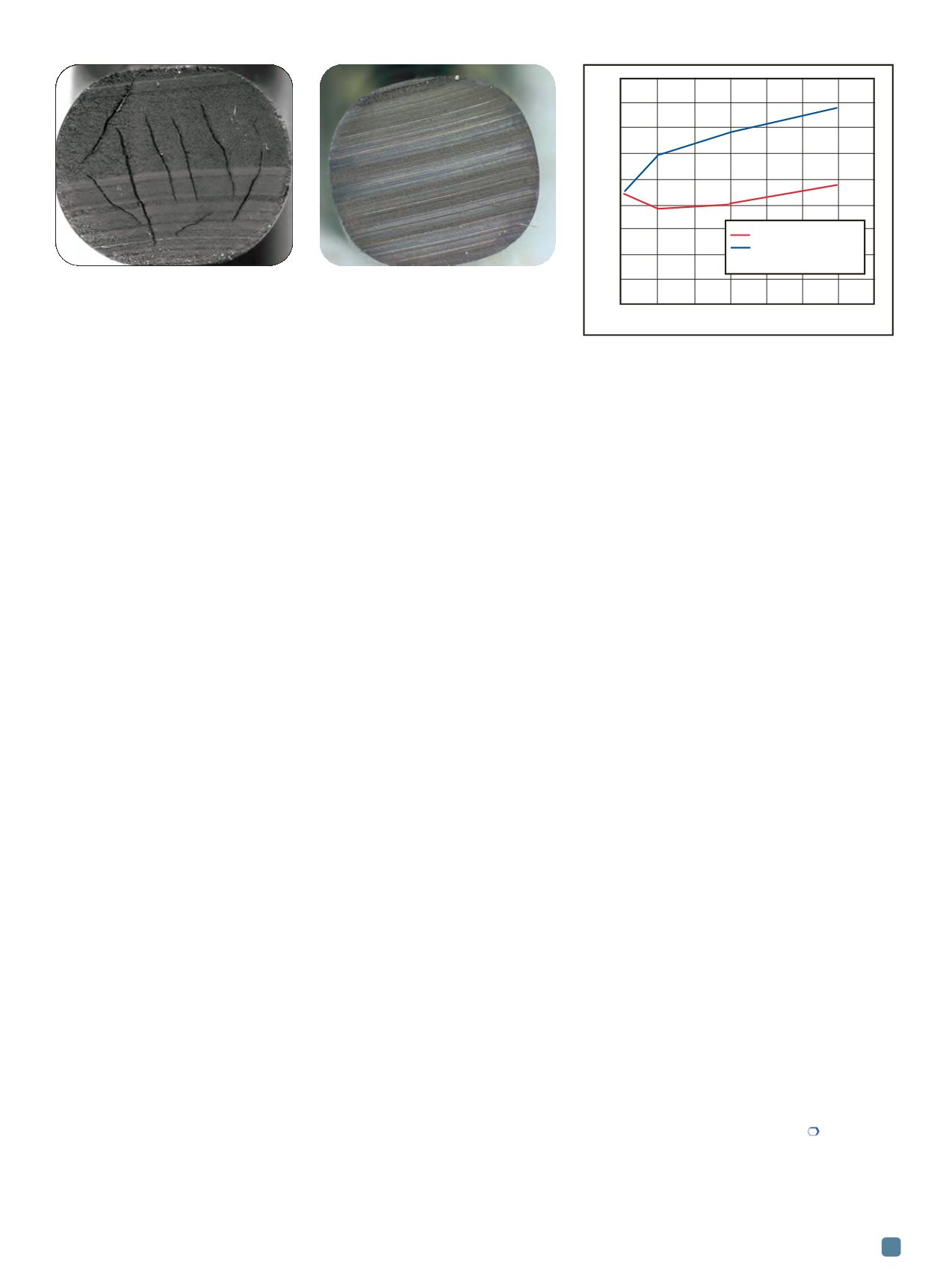
ADVANCED MATERIALS & PROCESSES •
JANUARY 2014
27
being produced in grades that are molecularly more robust
and reliable. The selected elastomers are relatively new, as
the most recent was developed 18 months ago. One partic-
ular FFKM was specifically engineered to resist gas decom-
pression, historically a major weakness of this elastomer. The
limits of HBNR also have been expanded, with one variety
exhibiting unprecedented resistance to high pressure in tests.
Pressure testing elastomers
To qualify and provide accurate, statistical data on these
seven elastomers, each was subjected to a variety of tests at
specific temperature ranges, pressures, and fluid ratios to
simulate existing environmental conditions at the well and
to meet the component’s required lifetime. Tests covered
three areas of interest: Long-term aging, mechanical per-
formance, and rapid gas decompression performance.
An extensive test matrix was conducted during a one-
year span. Much effort was dedicated to performance test-
ing, to ensure that each material was capable of
withstanding long-term exposure to various fluid chemical
elements. Seven high-pressure exposure tests up to 626 bar
and 212°F (100°C) were conducted, with multiple combina-
tions of oil, water, CO
2
, H
2
S, and methane. To perform
these high-pressure exposures, bespoke stainless steel
pressure vessels designed in-house were used. These have
a capacity of approximately 3 liters at 5 cm wall thickness,
and enabled testing of each elastomer at the required pres-
sures of nearly 10,000 lb/in
2
. Exposure tests monitored
swelling, changes in hardness, change in compression set,
and tensile properties after 1-, 3-, and 6-month durations.
To qualify the effects of decompression and material
performance, each elastomer was also subjected to three,
separate rapid decompression test scenarios at 626 bar
and 212°F (100°C), which simulates operational deepwa-
ter environments. To complement these tests, an innova-
tive pressure system with a custom sapphire-based
viewing window was designed. To create a pressurized
environment, the ends of a standard pressure vessel are
sealed with sapphire windows. The environments can be
observed and recorded; various fluids can be pumped
into the vessel where a material sample is mounted, to
view the seal performance under a wide range of simu-
lated conditions to the point of failure or physical dam-
age. Different swell rates under gas decompression for
elastomers being exposed to super-critical CO
2
were
recorded (Fig. 2). In addition, the exact point at which
material changes occur was charted, delivering previ-
ously unobtainable data.
Results and conclusions
The overall outcome was a definitive list that ranked
the seven elastomers and identified those best suited for
the specific simulated deepwater environment. Two show
significantly superior performance results across the test-
ing range and were thus recommended for operational de-
ployment. One HBNR displayed particularly impressive
resistance to damage under rapid decompression. When
taken as a benchmark, a comparable product tested sev-
eral years prior suffered noticeable cracks in a cross sec-
tion of the testing sample (Fig. 3). Under identical
conditions and viewed in situ through the sapphire-based
window, the best performing modern HBNR is character-
ized by uniform resistance (Fig. 4).
The operational integrity of this HBNR also remained
unaffected by super-critical CO
2
. After benchmark perform-
ance levels under conditions with heavy levels of both super-
critical CO
2
and H
2
S, tests were repeated without hydrogen
sulphide to determine if the CO
2
produced a negative reac-
tion. While H
2
S with super-critical CO
2
has a highly damag-
ing effect over six months as expected, super-critical CO
2
alone caused negligible performance fluctuations (Fig. 5).
Advanced materials, such as these elastomers, give
component designers an option over metal-to-metal seals,
which do not perform as well and present various chal-
lenges. The elastomer performance exhibited during test-
ing positions it as a versatile material, while its inherent
flexibility makes it well suited for other offshore technolo-
gies, such as bonded hoses that transport oil from ship to
ship. Capable of operating at a wide range of temperatures
and pressures, the more robust varieties can be formed
into larger diameter products that are less likely to fracture
when deployed in heavily rolling seas.
At these largely unexplored depths, even a single valve
is a critical component that needs to be fully functioning
and maintain its integrity for up to 30 years. Advanced ma-
terials are enabling the major oil companies to operate at
deepwater levels and it is only through rigorous testing and
qualification that confidence can be gained in their use.
For more information:
Glyn Morgan is sector manager,
oil and gas, Element Materials Technology, 662 Cromwell
Ave., St. Paul, MN 55114, 888/786-7555,
www.element. com.Fig. 3 —
Typical decompression damage
to traditional HNBR material.
Fig. 4 —
Best modern HNBR after de-
compression test at identical conditions.
Fig. 5 —
HBNR performance in a gas environment
at 167°F (75°C) in 90% CO
2
at 600 bar pressure.
l
l
l
l
l
l
l
0 1 2 3 4 5 6 7
Exposure time, months
18
16
14
12
10
8
6
4
2
0
Modulus, MPa
Super critical CO
2
Super critical CO
2
with trace H
2
S