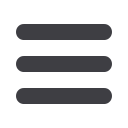
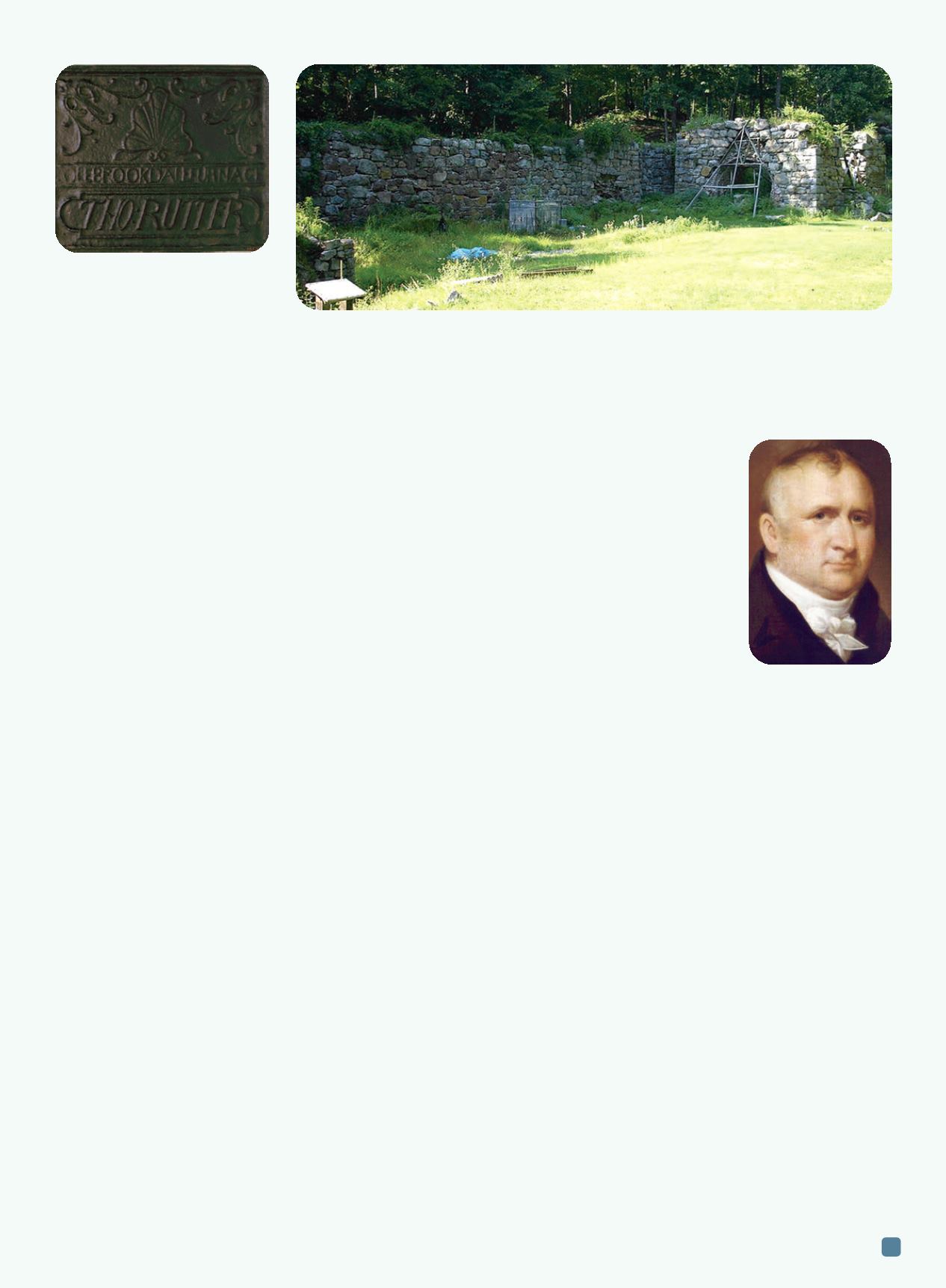
ADVANCED MATERIALS & PROCESSES •
JANUARY 2014
29
Iron production in the new United States in-
creased from these 30,000 tons at the beginning
of the American Revolution to 54,000 tons from
153 furnaces by the 1810 census. The slow growth
was largely due to a general lack of industrializa-
tion in America: Per capita iron consumption
hardly changed in this 35-year span. Another fac-
tor keeping growth in check was the relatively in-
expensive iron imported from England. It was
cheaper to make iron from coke in Britain and
ship it to major East Coast port cities than to con-
tinue using charcoal in the inland U.S. plantations
and then transporting finished iron to growing
population centers.
Philadelphia and the canal systems
The beginnings of a solution to the English im-
port problem came about because the city of
Philadelphia was desperately seeking a way to pre-
vent the influx of farm products and manufactured
goods from areas north and west of the city using
the Susquehanna River to ship from Baltimore.
Philadelphia was the largest port in the newU.S. and
its politicians were battling to maintain this position
against New York City and nearby Baltimore. Top
priority was to capture the local trade leaking out to
Baltimore and to transport energy resources from
the new anthracite coal mines from the region in
Pennsylvania’s northeastern corner to metropolitan
areas along the coast. The only solution to bulk
transportation at this point was by water. While
there were many natural streams in this corner of
Pennsylvania, they contained numerous obstacles to
navigation. This meant building canals.
Canals were not new to America, as they had
been dug in New England with some effective-
ness. With the successful attempt to build one
across upstate New York all the way to Lake Erie,
a project just coming to completion in the mid-
1820s, many attempts were undertaken to build
them throughout the country. One of the most
profitable was the Delaware and Hudson Canal,
built with private capital.
This canal system was masterminded by three
brothers by the name of Wurts, who had tied their
future to that of the anthracite coalfields behind
Moosic Mountain in the Scranton, Pa., area. Yet
two major problems existed—finding a way to get
the coal out of the wilderness of Northeast Pa. and
down to the cities on the coast, especially New
York, and convincing people that anthracite coal
(known as stone coal) was an acceptable fuel. The
Wurts brothers believed if they could get the coal
to New York at a reasonable cost, its value would
soon sell itself, a belief shared by their ally Philip
Hone, then mayor of New York City.
Technical expertise for the project came from
Benjamin Wright, chief engineer of the Erie Canal.
The logical route for the new canal was across the
Delaware River into New York, northeast up the
valleys west of the Shawangunk Mountains, down
Rondout Creek to Kingston, New York, and then
through the Hudson River. It was a natural water-
way, even though it meant the canal went north-
east when New York City was southeast.
Other canals were built on the Susquehanna,
Schuylkill, Lehigh, and Delaware Rivers. The Union
Canal system linked the Susquehanna and the
Schuylkill with the coal fields above Reading, Pa.
With the sudden availability of anthracite coal in
Southeastern Pa., the ironmasters soon learned to
adapt it to their blast furnaces. The hard coal did
not have to be processed to coke and was usable di-
rectly from the mine. Just as coke had revived the
British iron industry a century earlier, anthracite
coal accomplished the same result for the iron in-
dustry in Southeastern Pa. The industry had been
in a long period of decline because it was running
out of wood. This strategy of improved water trans-
portation with the fortuitous application of an-
thracite coal in ironmaking worked sufficiently well
to allow this region to become the first major iron
producer in America.
The passage of a half-century and a Civil War
would occur before Pittsburgh would replace
Philadelphia as the leader in ironmaking. During
this time, Philadelphia would begin manufacturing
the mill machinery and building the factories for
products made of iron, thereby serving as a major
incubator for the American Industrial Revolution.
For more information:
Charles R. Simcoe can be
reached at
crsimcoe@yahoo.com. For more metallur-
gical history, visit
www.metals-history.blogspot.com.
Peter Hasenclever’s
Long Pond Ironworks,
N.J., a furnace from the
Civil War era. Courtesy of
KForce at en.wikipedia.
When the Erie Canal
was funded in 1817,
Benjamin Wright
became the chief
engineer who directed
the successful
completion of the
greatest artificial
waterway in the world.
Courtesy of Francis
Delafield Wright III;
www.marblecemetery.org.
A cast iron stove plate made at
Colebrookdale Furnace, Pa., circa
1765. Courtesy of the State Museum
of Pennsylvania.