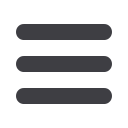
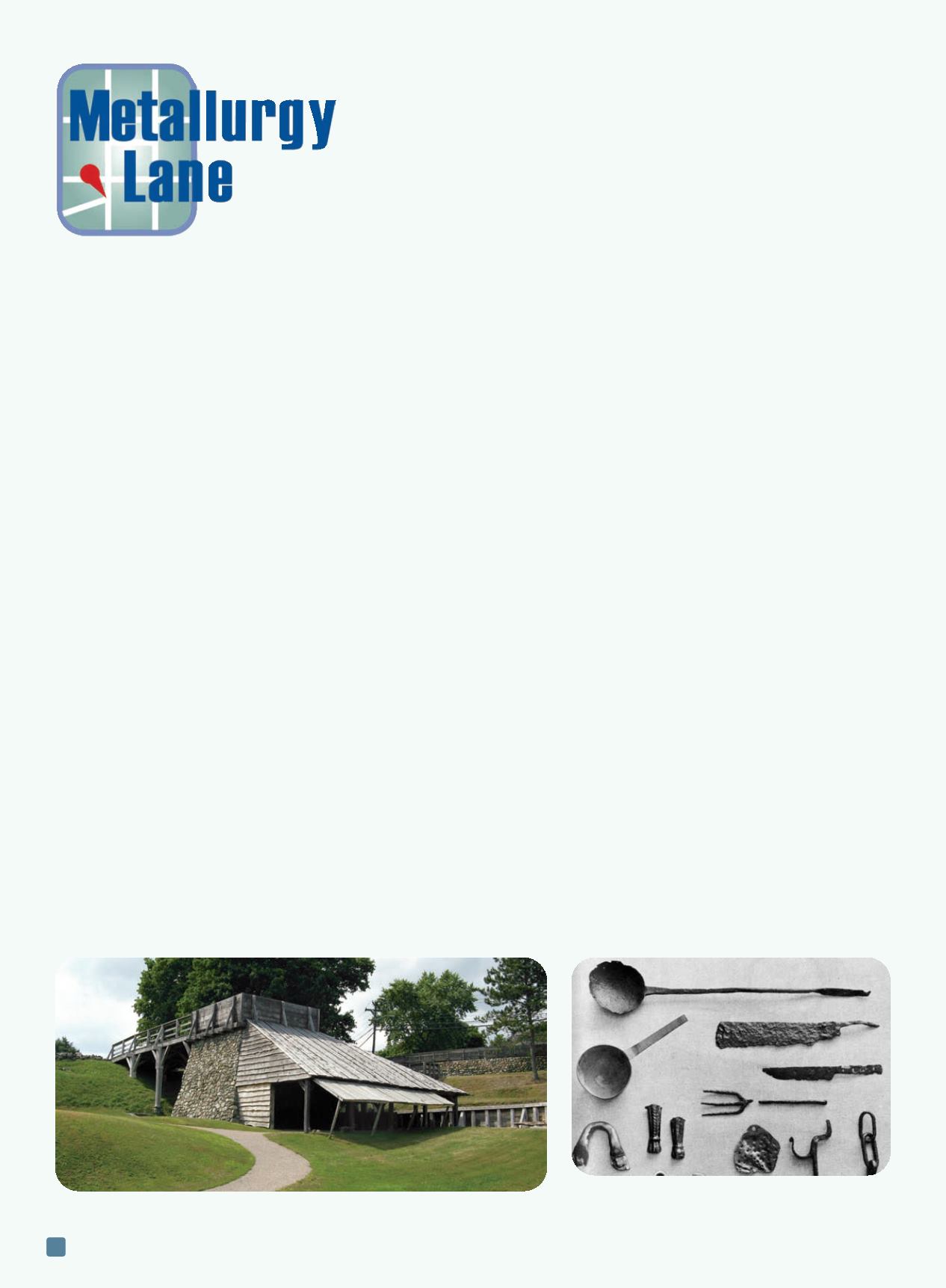
ADVANCED MATERIALS & PROCESSES •
JANUARY 2014
28
Metallurgy Lane is a
new series authored by
ASM life member
Charles R. Simcoe,
developed to share the
early history of the U.S.
metals and materials
industries along with key
milestones and
developments. Simcoe,
a World War II veteran,
holds a degree in
metallurgical engineering
from Purdue University
and spent his career in
physical metallurgy R&D
at Westinghouse Atomic
Power Division, Battelle
Memorial Institute,
Armour Research
Foundation,
and Simonds Steel Co.
Iron in America: 1645 to 1850
The steel industry of the U.S. rose out of the iron plants of our colonial past.
Here we take a brief historical look at the early days of ironmaking.
The furnace at Saugus Iron Works, Mass., circa 1645. Courtesy of John Phelan.
Early cooking implements from colonial New
Hampshire. Courtesy of
www.cowhampshireblog.com.
I
ronmaking commenced in the British Colonies as
early as 1645 at the Saugus Iron Works in Massa-
chusetts, although the effort was never financially
successful and closed in 1676. The site is now com-
pletely restored in tribute to America’s industrial
heritage. A more successful metals operation was
the Raynham Forge Plant near Taunton, Mass.,
which opened in 1656 and operated until 1880.
Other early furnaces were built at Braintree,
Mass., in 1648 and at New Haven, Conn., in 1658.
In 1716, Thomas Rutter built a bloomery forge to
make wrought iron in Berks County, Pa., and in
1720, constructed the Colebrookdale Blast Fur-
nace. Anthony Morris later built the famous
Durham Furnace and Ironworks near Easton, Pa.,
on the Delaware River.
Early pioneers make headway
Another early iron pioneer was Peter Grubb,
who discovered the iron ore deposit where he lo-
cated the famous Cornwall Iron Mine in 1736. This
open-pit mine became the largest source of iron
ore in America until the debut of the great ore de-
posits of Michigan and Minnesota more than a
century later. Grubb built the Cornwall Iron Fur-
nace and the town of Cornwall itself for housing his
Welsh workers in 1742, naming the town in honor
of his father’s English birthplace. Between these
very early iron plants and the time of the Revolu-
tionary War, ironmaking spread to many of the
New England Colonies.
Wherever bog iron ore or other iron-bearing
minerals were found in conjunction with plentiful
supplies of wood for charcoal, iron could be made,
provided either a local population or water trans-
portation to a ready market was also available.
Ironmaking spread to New Jersey by 1710, with
later operations at Oxford Furnace (1741-1882)
and at the Pine Barrens in southern New Jersey
where the 20,000-acre Martha Furnace operated as
one of the biggest facilities ever constructed. Prior
to the war, Peter Hasenclever’s Long Pond Iron-
works was one of the largest such investments at
approximately $250,000.
The Principio plant in Maryland was another
substantial operation. At the time of its 1751 debut,
it boasted four blast furnaces and two forges, with
timber covering 30,000 acres. Principio was de-
stroyed by the British Army in 1777, rebuilt for the
war of 1812, and then destroyed by the British a
second time. In 1836, the Whitaker brothers ac-
quired it and restored it once again. The Principio
Co. was absorbed into Wheeling Steel Co. in 1920.
Ironmaking expands
into Pennsylvania and beyond
Pennsylvania had become the major iron-pro-
ducing region by the time of the Revolutionary
War. The availability of ore, wood for charcoal,
limestone for flux, and the major waterways of the
Susquehanna, Schuylkill, and the Lehigh-Delaware
Rivers and their tributaries kept this region pro-
ductive until—as happened earlier in England—
wood for charcoal became scarce. These iron
plantations produced from a few hundred tons to
as much as 1000 tons, resulting in the ironmakers
of colonial America turning out approximately
30,000 tons of iron in 1775 alone.