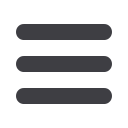
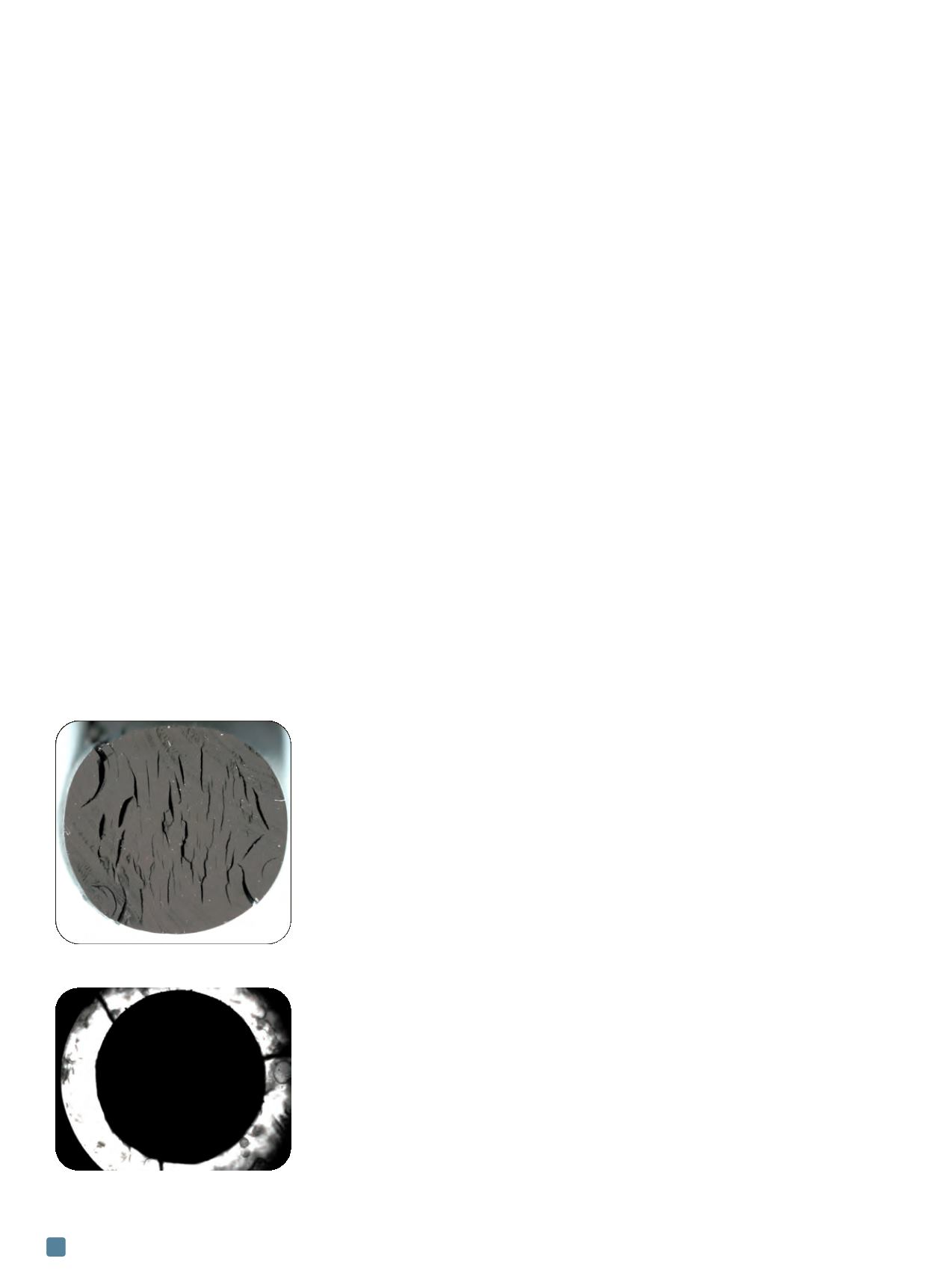
T
he oil and gas industry is focusing on
deepwater exploration for developing
reserves of natural oil and gas, as “easy”
reserves are becoming scarcer. The trend to-
wards deeper, colder, and more extreme envi-
ronments within recent years is demonstrated
by discoveries of mega-fields such as that off
the shores of Brazil. According to a report by
Douglas-Westwood in 2013, more than $232
billion will be spent on deepwater projects be-
tween now and 2020. Such a substantial invest-
ment hints at the anticipated challenges that
companies involved in exploration and produc-
tion expect when accessing oil at depths of any-
where up to 2 miles below sea level.
While the projection highlights the most
obvious challenges as financial in nature—such
enterprises are more costly than onshore or
fixed offshore operations—few alternatives
exist. With rapidly emerging economies such as
China and India, global energy demand shows
no sign of stopping, with oil as the dominant
source of power for the near future. The single
greatest challenge oil producers face when ex-
tracting deepwater oil is not an economic one,
but rather a technical hurdle.
The environment of fields found at
depths of 1.25 miles and deeper make
deploying standard equipment unfeasi-
ble. For example, these fields have un-
usually high levels of CO
2
that can occur
in the production stream, which comes
out of the reservoir in a super-critical
state, at a temperature exceeding 88°F
(31°C) and pressure of 74 bar. In this
state, the CO
2
exists as a dense phase
fluid, displaying characteristics of both
liquid and a gas, and poses difficulties
for equipment used to transport oil
from the well to the surface. Valves and
blowout preventers are attacked by
super-critical CO
2
, but also damagingly
high levels of corrosive H
2
S found in
deepwater environments.
This CO
2
can be useful if injected
back into the reservoir to reduce oil vis-
cosity and assist its flow back to the well.
Using such full-field subsea separation
and boosting and injection systems, the
Statoil Hydro-operated Tordis field in the
North Sea increased recovery by an extra
35 MMbo (millions of barrels of oil) and
extended the life of the field by 15 to 17
years in 2007. At higher temperatures and pres-
sures in deeper water, longstanding issues of cor-
rosion, pressure, and temperature all pose greater
problems for compressors and other components.
Elastomer selection and qualification
Element Material Technology, St. Paul,
Minn., is currently involved in the research, de-
velopment, and qualification of next-generation
materials designed to offset problems posed by
deepwater extraction. Elastomers are being
considered due to their flexible and pliant na-
ture, which makes them well suited as sealing
components. The team was recently ap-
proached by a client seeking to operate in a field
discovered off the coast of Brazil at a depth of
1.25 miles in order to characterize a range of
advanced elastomers.
At this depth, elastomers are more suscep-
tible to chemicals and can become structurally
altered. The valves and components are in con-
tact with oil and gas at temperatures of 248°F
(120°C) and must contend with high pressures
and rapid gas decompression events, so qualifi-
cation and selection of the best materials for
this environment is critical.
Seven well characterized primary products
were selected for qualification to deliver opti-
mum performance and to represent the full
range of three core varieties of elastomers—hy-
drogenated nitrile butadiene rubber (HNBR),
fluoroelastomer (FKM), and perfluoroelas-
tomer (FFKM). Each elastomer type has partic-
ular strengths—FFKM is particularly suited to
high temperatures and chemically aggressive
environments, while HNBR performs well at
lower temperatures. FKM has good resistance
to thermal and chemical environments and gas
decompression events.
Rapid gas decompression and pressure resist-
ance are primary concerns when selecting a par-
ticular elastomer for these components. However
advanced the material may be, under pressure
and over time, damaging chemical elements such
as super-critical CO
2
andH
2
S will diffuse into the
polymer and permeate through it. If rapidly de-
compressed, the change in pressure means gases
are forced out of the material, potentially causing
blistering or cracks as they escape, as seen in
Fig. 1. Under constant pressure, fluid diffused
into the material can cause swelling and weaken-
ing, potentially causing leakage.
To overcome this issue, elastomers are
Advanced Elastomers
for Deepwater Oil Exploration
Through
rigorous
testing and
qualification,
advanced
materials
enable major
oil companies
to operate in
ever more
extreme
environments.
ADVANCED MATERIALS & PROCESSES •
JANUARY 2014
26
TECHNICAL SPOTLIGHT
Fig. 2 —
Super-compressed CO
2
at
pressure and temperature surrounding
the elastomer during decompression.
Fig. 1 —
Typical decompression failure
of FKM material.