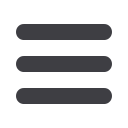
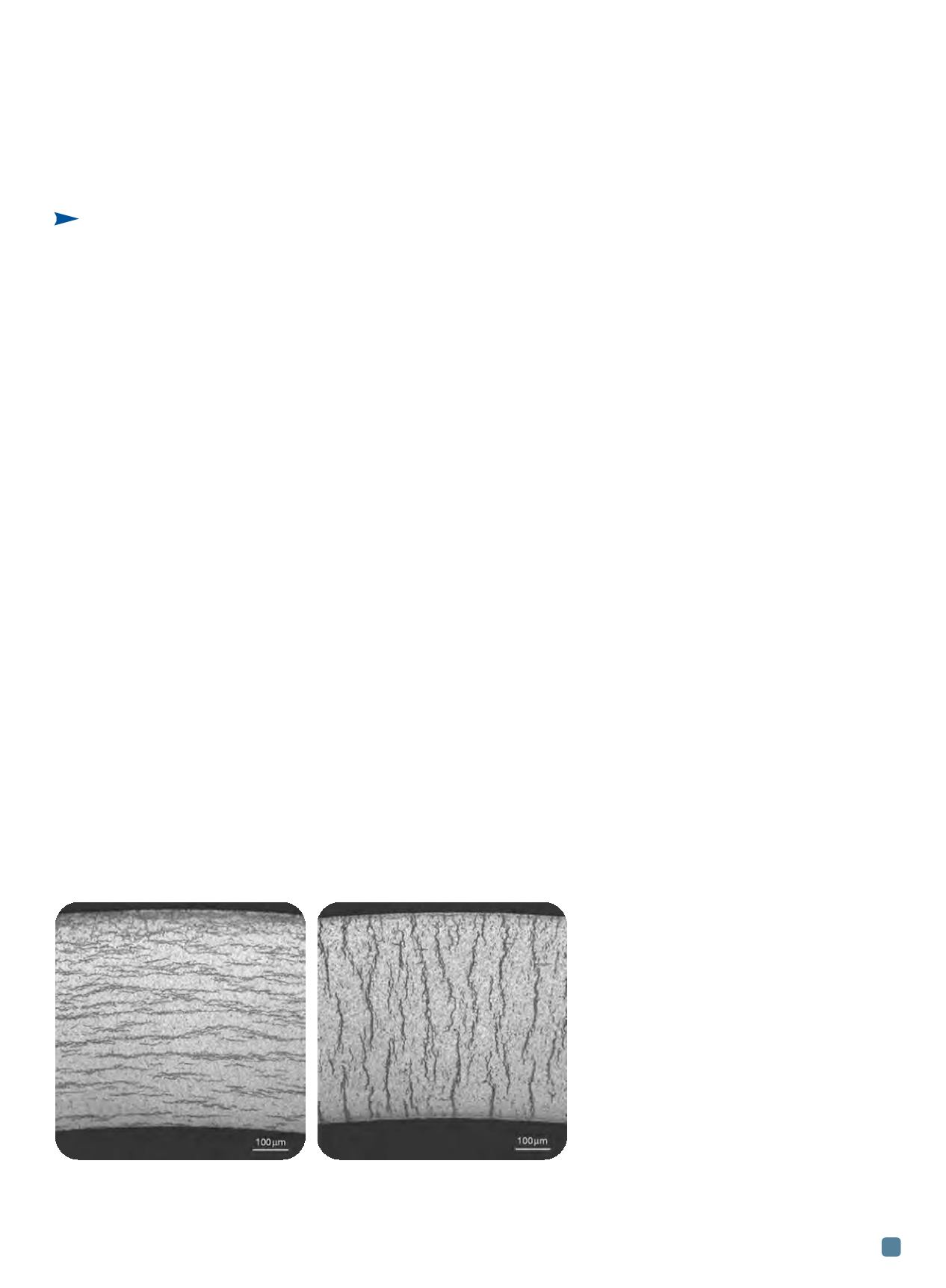
ADVANCED MATERIALS & PROCESSES •
JANUARY 2014
17
Understanding How Materials Corrode
in Nuclear Reactors
C
orrosion of structural materials is an im-
portant consideration for both today’s
nuclear reactors and the development of
future advanced reactor concepts. Corrosion can
decrease the effective wall thickness of compo-
nents and can generate activated oxide or corro-
sion product debris particulates in reactor
systems. In conjunction with improper mi-
crostructure and tensile stress in the material it
can also lead to stress corrosion cracking (SCC).
Radiation-induced segregation (RIS) of elements
to grain boundaries can also promote SCC.
While light water reactors (LWR) use pres-
surized high-temperature water as a coolant,
other coolants such as molten metal, helium,
and molten salt are being considered for higher
temperature advanced reactor technologies
with enhanced capabilities and improved effi-
ciencies. Materials development and selection
for corrosion resistance is critical in all reactor
designs. In addition, control of coolant chem-
istry is a viable option for mitigating corrosion.
In this article, corrosion issues in four reactor
concepts that use vastly different coolant types
are reviewed.
Light water reactors
Most power reactors worldwide are LWR,
using water as the coolant and operating in the
250-350°C temperature range. Boiling water re-
actors (BWR) operate at pressures of ~7MPa,
while pressurized water reactors (PWR) oper-
ate at higher pressures (~15MPa) and temper-
atures than BWR. Zirconium alloys are used in
LWR for fuel cladding due to their high neutron
transparency. These alloys are predominantly
zirconium (~98%) with small amounts of other
constituents such as tin, niobium, iron,
chromium, and nickel
[1]
. Historically, Zircaloy-
2 and Zircaloy-4 have been used as cladding
materials. More recently, zirconium alloys such
as ZIRLO and M5 were developed for superior
corrosion resistance. In LWR environments, Zr
alloys react with high-temperature water to
form Zr-oxide and hydrogen or directly with
dissolved oxygen in water to form Zr-oxide:
Zr + H
2
O = ZrO
2
+ H
2
Zr +O
2
= ZrO
2
Oxidation of Zr cladding is a limiting factor in
achieving higher fuel burn-ups to reduce costs.
Radiation can potentially enhance oxidation
rate, an effect attributed to the creation of dif-
fusion-enhancing point defects in the oxide
layer and the radiolysis of water, which can re-
lease free oxygen
[2]
. In most cases, Zr alloys ex-
hibit uniform corrosion. Early stages are
marked by the formation of a dense oxide film
with tetragonal crystal structure, which follows
a cubic growth law and is therefore very pro-
tective. Next, a regime of columnar oxide
growth is accompanied by transformation of
the oxide to a monoclinic crystal structure.
Oxide thickness measurements of Zr alloys
from autoclave tests demonstrate a series of
cyclic patterns, each following cubic oxide
growth law during initial exposure with an
eventual transition to linear growth law behav-
ior. Micro-cracking of the oxide due to com-
pressive stresses or stresses from crystallo-
graphic transformation is attributed to this pe-
culiar growth behavior. It is evident that water
coolant chemistry plays an important role in
corrosion
[3]
.
In PWR, boron (in the form of boric acid) is
added to water to reduce core reactivity, while
LiOH is added to counteract the boric acid’s
acidic effect. Infusing lithium into oxide me-
chanically destabilizes the oxide layer and ad-
versely affects its protective qualities. Another
form of Zr alloy corrosion in BWR is nodular
corrosion, which manifests as circular nodules
in the early stages of oxidation. Thicker oxide
layers are observed on Zr alloys in the vicinity
of stainless steel and Inconel components. This
is known as shadow corrosion and is thought
to occur due to galvanic effects.
Hydrogen diffusion produced from corro-
Kumar Sridharan,
FASM*
University of
Wisconsin-Madison
The corrosion of
structural
materials and
control of
coolant
chemistry are
key factors that
impact the
lifetime of
nuclear reactors
and the
development of
future reactors.
Fig. 1 —
(a) Circumferential and (b) radial hydrides formed in Zr alloy claddings as a
result of corrosion
[3]
.
(a) (b)
*Member of ASM International and ASM Thermal Spray Society