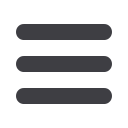
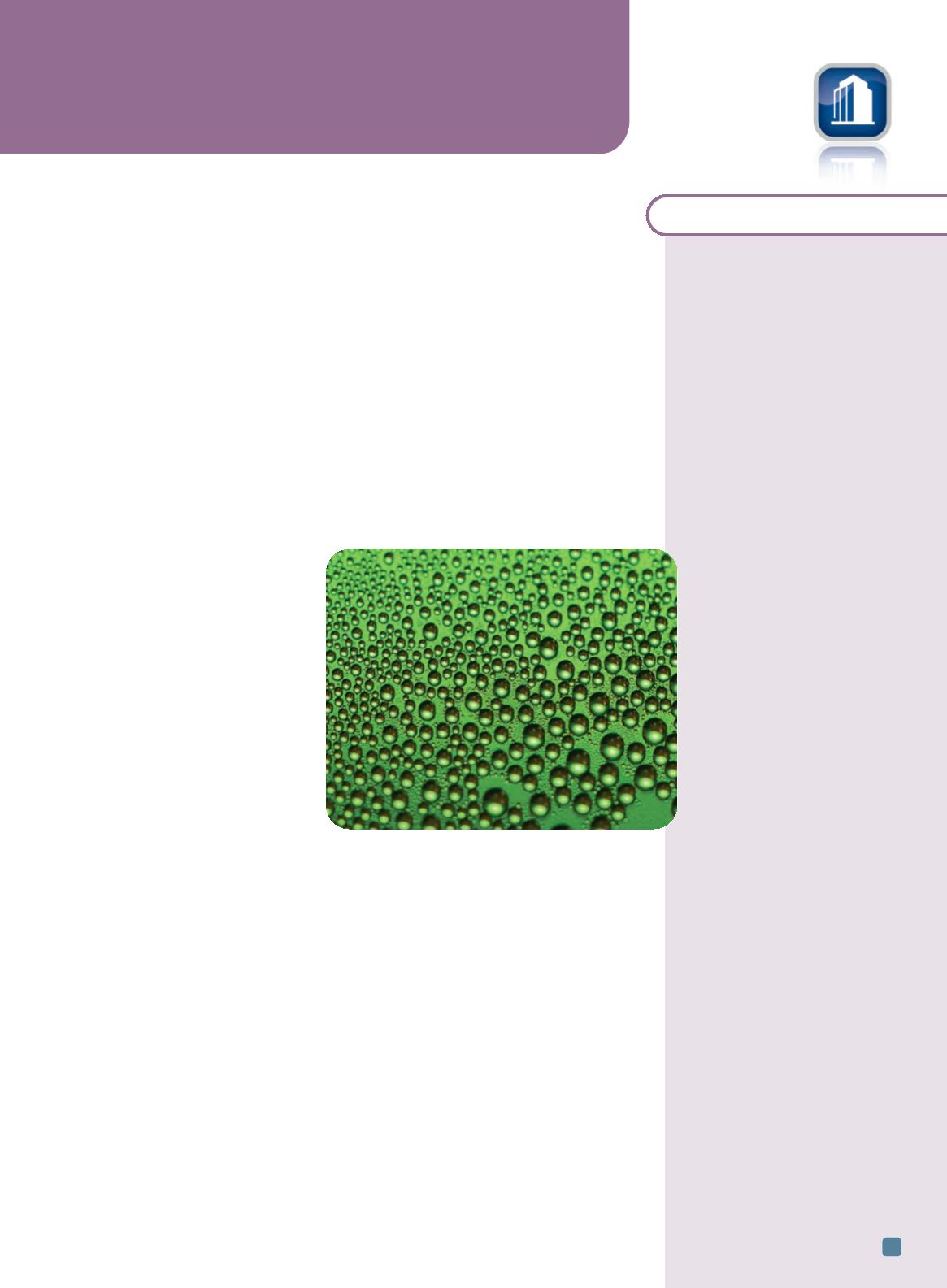
ADVANCED MATERIALS & PROCESSES •
JANUARY 2014
13
S
URFACE
E
NGINEERING
news
industry
briefs
Advenira Enterprises Inc.,
Sunnyvale, Calif., was issued U.S.
Patent No. 8,507,035. It covers the
company’s Hybrid 3D coater that
allows nanocomposite material to
be applied to virtually any
substrate shape or material
including polycarbonate, ceramic,
quartz, aluminum, and others. This
is an alternative to the commonly
used vacuum and non-vacuum
deposition techniques. Key
advantages of solution derived
nanocomposite (SDN) technology
reportedly include excellent
uniformity and performance at
lower cost with high throughput
and material use. The coating can
substantially improve production
processes, which in turn enables
smaller chip size and longer
battery life for portable devices.
www.advenira.com.
Titan Spine,
Mequon, Wis.,
conducted a study that shows that
its implant surface technology
promotes superior production of
angiogenic growth factors as
compared with PEEK (poly-
ether-ether-ketone) and smooth
titanium alloy materials. The study
compared the production of
osteogenic (bone formation) and
angiogenic (blood vessel
formation) growth factors by
human osteoblast cells cultured on
PEEK, smooth titanium alloy, and
Titan Spine’s roughened titanium
alloy surface. This osteogenic
environment may enhance bone
formation, implant stability, and
fusion.
www.titanspine.com.
The
University of Central Florida,
Orlando, signed its first license
agreement with student-led
spinout company
Mesdi Systems
Inc.
Mesdi specializes in the
production and implementation of
advanced spray equipment used to
manufacture nanomaterials and
ultra-thin coatings. The agreement
gives Mesdi the tools it needs to
scale-up its proprietary equipment
that is currently being
implemented to manufacture next-
generation lithium-ion batteries.
www.ucf.edu.
New engine coatings promise longer life
Self-healing thermal barrier coatings (TBCs) designed to improve gas turbine engine
efficiency were developed by researchers at Delft University of Technology, the Nether-
lands. The TBCs were tested in aero-engines, but can potentially be used in ships, sub-
marines, and even for generating electrical power.
Researchers working on the self-healing thermal barrier coatings (SAMBA) project
wanted to develop a system of applying new ceramic TBCs to the most critical parts of en-
gines. This would enable operators to push the engines beyond the melting point of the
structural components. By allowing higher operational temperatures, the ceramic coatings
can save companies fuel and reduce CO
2
emissions. The ceramic TBCs’ ability to repair
small cracks therefore has the potential to prolong the lifetime of coatings by 20-25%, and
thus significantly reduce maintenance costs
.
www.sambaproject.eu.
Improved hydrophobic materials boost power plant efficiency
Researchers at Massachusetts Institute of Technology, Cambridge, say they found a
way to improve the efficiency of steam condensation—the key to worldwide production of
electricity and clean water. It has been known for years that making steam-condenser sur-
faces hydrophobic could improve the efficiency of condensation by causing the water to
quickly form droplets. But most hy-
drophobic materials have limited dura-
bility, especially in steamy industrial
settings. The new approach to coating
condenser surfaces should overcome
that problem, according to researchers.
The covalent-bonding process the
team developed is significantly more
stable than previous coatings, even
under harsh conditions. Tests of metal
surfaces coated using the team’s
process show “a stark difference,” says
Kripa Varanasi, professor of mechani-
cal engineering. The material stood up
well even when exposed to steam at
100°C in an accelerated endurance test.
The coating can easily be applied to
conventional condenser materials—
typically titanium, steel, copper, or alu-
minum—in existing facilities, using
a process called initiated chemical vapor deposition.
For more information:
Kripa Varanasi, 617/324-5608,
varanasi@mit.edu,
http://varanasi.mit.edu.
Coatings protect against rust
Rice University, Houston, researchers discovered that atomically thin sheets of hexag-
onal boron nitride (h-BN) protect what is underneath them from oxidizing even at very
high temperatures. Researchers made small sheets of h-BN via chemical vapor deposition
(CVD), a process they said should be scalable for industrial production. The thin material
was grown on nickel foil and was found to withstand high temperatures in an oxygen-rich
environment. Researchers also grew h-BN on graphene and found sheets of h-BN could be
transferred to copper and steel with similar results. “What’s amazing is that these layers are
ultrathin and they stand up to such ultrahigh temperatures,” says materials scientist Pulickel
Ajayan. “At a few nanometers wide, they’re a totally noninvasive coating. They take almost
no space at all.”
For more information: Pulickel Ajayan, 713/348-5904,
ajayan@rice.edu,
www.rice.edu.
On typical hydrophobic coatings, droplets forming
from high-temperature steam soon spread out
to coat the surface, quickly degrading their
performance. The coating seen here maintains its
ability to foster droplet formation over long periods.