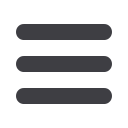
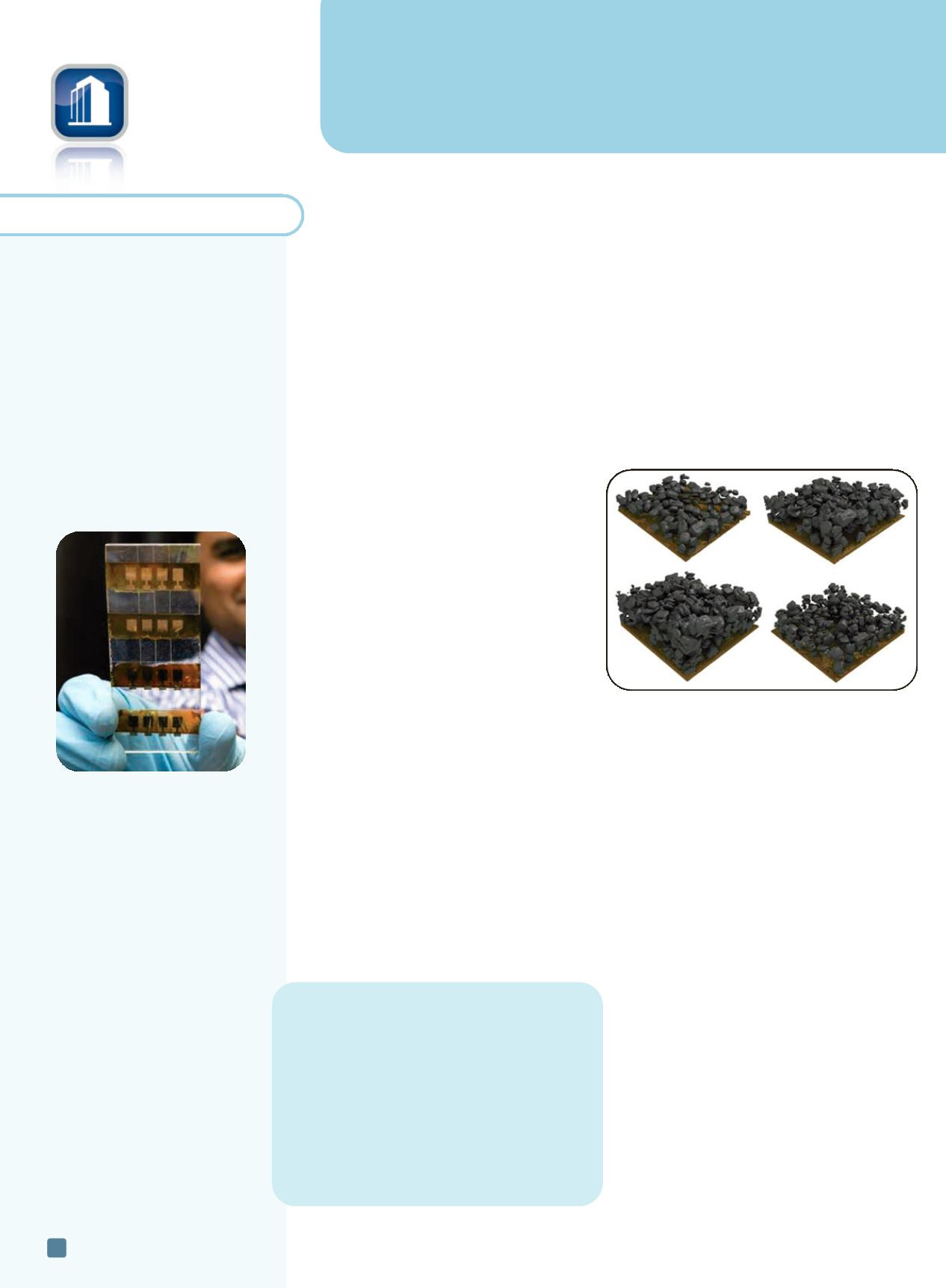
news
industry
Green magnets attract research
Researchers at Case Western Reserve University, Cleveland, received a second $1 mil-
lion federal grant to create an eco-friendly material for better power-converting magnets
in wind turbines and electric cars. The group believes it can make magnetic powder out of
inexpensive and plentiful iron and nitrogen, which can be compacted to form magnets
with the desired properties. Engineers are combining early materials science with recent
methods they developed to increase the carbon concentration in stainless steel way be-
yond the usual equilibrium solubility limit.
The Ames National Laboratory, Iowa, is providing a starting powder of specially engi-
neered spherical alloy particles. Engineers will design and build a fluidized-bed reactor at
Case to optimize the processing parameters.
For more information: David Matthiesen,
216/368-1366,
david.matthiesen@case.edu,
www.case.edu.
Why lithium-ion batteries fail
In the search for higher energy density
batteries, scientists have experimented for
more than 20 years with materials capa-
ble of repetitively alloying and de-alloying
with lithium. Laboratory-scale experi-
ments show that batteries with such ma-
terials have energy densities multiple
times that of intercalation materials; how-
ever, these alloying materials are not yet
exploited in industry due to limited life-
times. Martin Ebner, PhD student at the
Laboratory for Nanoelectronics in the
Department of Information Technology
and Electrical Engineering (D-ITET),
Zurich, explains, “Their capacity typically
fades after a couple of charging and dis-
charging cycles.” This is attributed to a massive—up to threefold—expansion of the elec-
trode material during charging. During discharge, the materials contract again, but do not
reach their original state. Electrode particles break apart, the electrode structure disinte-
grates, and the fragments lose contact with the rest of the cell.
www.lne.ethz.ch.
Tree hugging battery made of wood
An episode of the American Chemical Society’s (ACS’) Global Challenges/Chemistry
Solutions podcast series describes the development of a battery made from a sliver of
wood coated with tin. It shows promise for becoming a tiny, long lasting, efficient, and
environmentally friendly energy source. The device is 1000 times thinner than a sheet of
paper, according to researchers. It is well known that wood fibers from trees are supple
and naturally designed to hold mineral-
rich water, similar to the electrolyte used
in batteries. Researchers decided to ex-
plore using wood as the base of an exper-
imental sodium-ion battery. Using
sodium rather than lithium would make
the device environmentally friendly.
Lab experiments show the device per-
formed successfully though 400 charge-
discharge cycles, putting it among the
longest-lasting of all sodium-ion
nanobatteries.
www.acs.org/globalchallenges.ADVANCED MATERIALS & PROCESSES •
JANUARY 2014
12
E
NERGY
T
RENDS
briefs
Scientists at
Nanyang
Technological University (NTU),
Singapore, developed next
generation solar cells made of
organic-inorganic hybrid
perovskite materials. They are
about five times less expensive
than current thin-film solar cells,
due to a simpler solution-based
manufacturing process. Perovskite
is known to be a remarkable solar
cell material as it can convert up to
15% of sunlight to electricity, close
to the efficiency of current solar
cells, but scientists did not know
why or how, until now.
www.ntu.edu.sg.
Close-up of the new perovskite
solar cells made in NTU’s Energy
Research Institute. Courtesy of
Nanyang Technological
University.
Building on President Obama’s
broad-based plan to cut carbon
pollution and support clean energy
innovation across the country,
Energy Secretary Moniz recently
announced about $60 million to
support innovative solar energy
research and development. As part
of the department’s
SunShot
Initiative,
these awards will help
lower the cost of solar electricity,
advance seamless grid integration,
and support a growing U.S. solar
workforce.
www1.eere.energy.gov/solar/ sunshot.Particles of a tin oxide electrode experiencing
structural changes during charging (1-3) and
discharging (3-4). Courtesy of Martin Ebner,
Laboratory for Nanoelectronics, ETH Zurich.
Colorado State University,
Fort Collins, researchers are
nearing the prototype phase for a lithium ion battery that
could be safer, less expensive, faster charging, and more
environmentally friendly than conventional batteries. The
team developed one component at a time—starting with
a copper foam structure purchased to serve as the current
collector on the anode side of the battery. Foam is
relatively easy to manufacture and has a 3D structure that
increases the surface area of the electrodes and brings
them closer together, thereby increasing power density.
The intricate 3D structures use the electrode material
more efficiently than a flat surface.
www.colostate.edu.
1 2
3
4